Homes England
Featured
Government has approved funding package to accelerate the creation of new homes, public realm and commercial space at Forth Yards
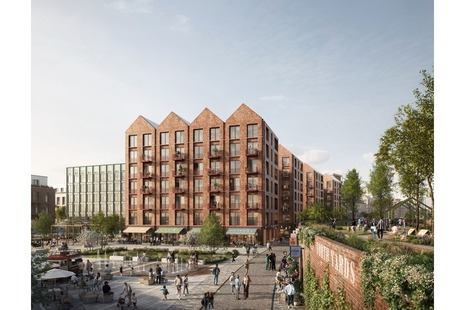
Homes England appoints Amy Rees CB as Chief Executive to lead bold housing and regeneration agenda
News story
Amy will lead the Agency’s mission to tackle the housing crisis and accelerate the delivery of 1.5 million new homes this Parliament.
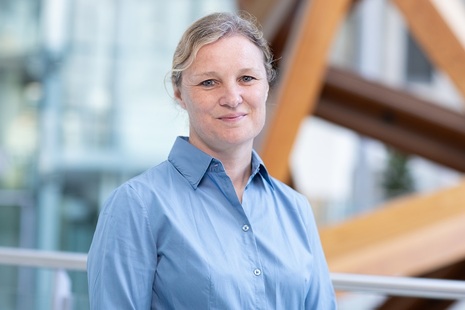
Residents and visitors can now enjoy safer, greener and more attractive journeys into York city centre as new travel routes through the York Central development open.
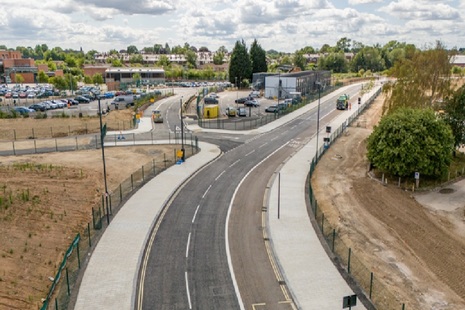
Homes England, NatWest and WMCA to support Aviva and Moda in £200m deal for major rental community in Birmingham
Press release
Homes England, Aviva Capital Partners, Moda Group, NatWest, and the West Midlands Combined Authority, have completed a landmark investment deal to unlock a 1,000-home rental community in Digbeth, Birmingham.
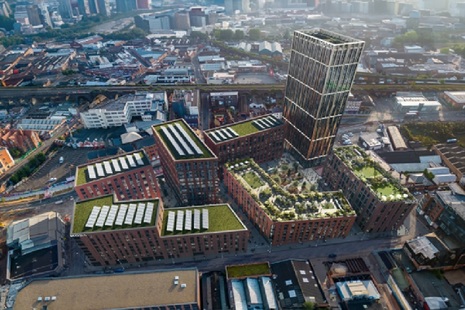
Homes England supports Greencore Homes to build new affordable sustainable homes in Oxfordshire
News story
£8 million development finance loan will help SME housebuilder as it seeks to reach its ambitious target to build 10,000 better than net zero homes by 2035.
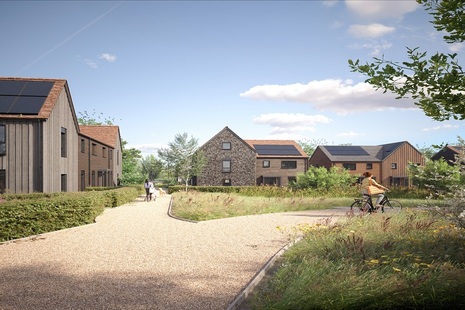
Through the Home Building Fund, we offer a range of direct lending and investment solutions to accelerate housebuilding.
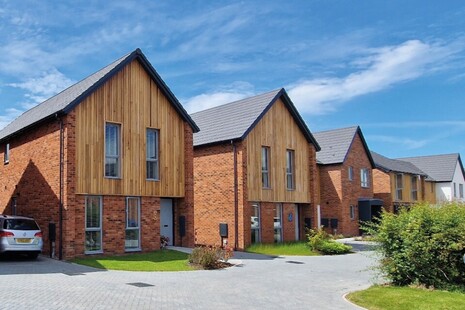
Latest from Homes England
What we do
As the government’s housing and regeneration agency we believe that affordable, quality homes in well-designed places are key to improving people’s lives.
Together with our partners, we’re accelerating the pace of house building and regeneration across the country, as we seek to deliver homes and places people are proud to live in – for generations to come.
Homes England is an executive non-departmental public body, sponsored by the Ministry of Housing, Communities and Local Government.
Follow us
Documents
Transparency and freedom of information releases
Our management
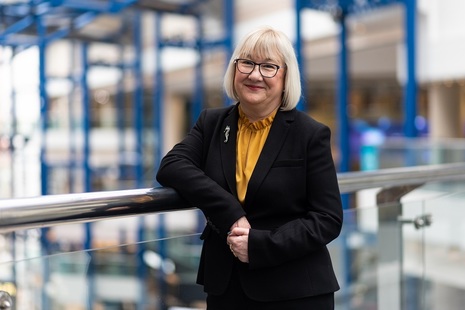
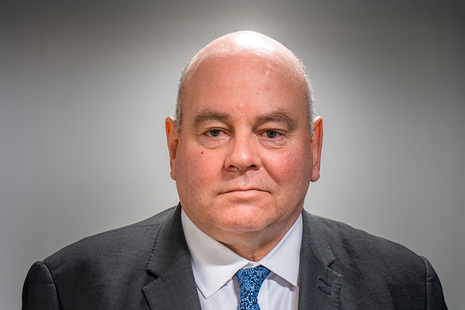
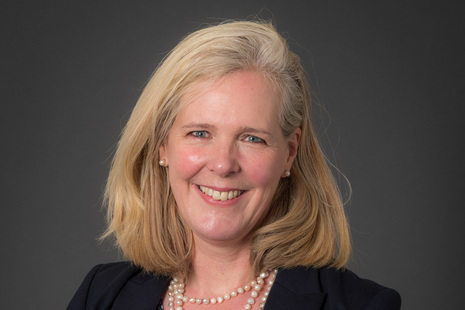
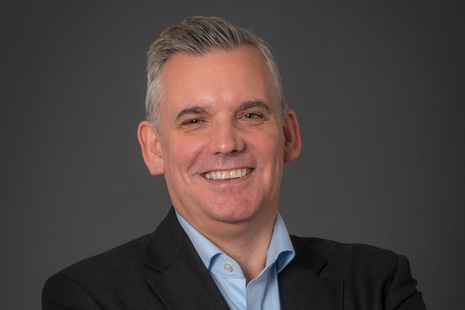
Contact Homes England
Contact Homes England
Telephone
0300 1234 500
Make an FOI request
- Read about the Freedom of Information (FOI) Act and how to make a request.
- Check our previous releases to see if we’ve already answered your question.
- Make a new request by contacting us using the details below.
Make a Freedom of Information request
Homes England
10 South Colonnade
Canary Wharf
London
E14 4PU
United Kingdom
Telephone
0300 1234 500
Corporate information
Jobs and contracts
Read about the types of information we routinely publish in our Publication scheme. Our Personal information charter explains how we treat your personal information.