OSART report on Torness nuclear power plant, 2018
Published 4 October 2018
International Atomic Energy Agency (IAEA) Report of the Operational Safety Review Team Mission to Torness Nuclear Power Station, United Kingdom
22 January – 8 February 2018
Division of Nuclear Installation Safety
Operational Safety Review Mission
IAEA-NSNI/OSART/199/2018
Preamble
This report presents the results of the IAEA Operational Safety Review Team (OSART) review of Torness Nuclear Power Station, UK. It includes recommendations for improvements affecting operational safety for consideration by the responsible UK authorities and identifies good practices for consideration by other nuclear power plants. Each recommendation, suggestion, and good practice is identified by a unique number to facilitate communication and tracking.
Any use of or reference to this report that may be made by the competent UK organizations is solely their responsibility.
Foreword
Director General
The IAEA Operational Safety Review Team (OSART) programme assists Member States to enhance safe operation of nuclear power plants. Although good design, manufacture and construction are prerequisites, safety also depends on the ability of operating personnel and their conscientiousness in discharging their responsibilities. Through the OSART programme, the IAEA facilitates the exchange of knowledge and experience between team members who are drawn from different Member States, and plant personnel. It is intended that such advice and assistance should be used to enhance nuclear safety in all countries that operate nuclear power plants.
An OSART mission, carried out only at the request of the relevant Member State, is directed towards a review of items essential to operational safety. The mission can be tailored to the particular needs of a plant. A full scope review would cover nine operational areas: leadership and management for safety; training and qualification; operations; maintenance; technical support; operating experience feedback; radiation protection; chemistry; and emergency preparedness and response. Depending on individual needs, the OSART review can be directed to a few areas of special interest or cover the full range of review topics.
Essential features of the work of the OSART team members and their plant counterparts are the comparison of a plant’s operational practices with best international practices and the joint search for ways in which operational safety can be enhanced. The IAEA Safety Series documents, including the Safety Standards and the Basic Safety Standards for Radiation Protection, and the expertise of the OSART team members form the bases for the evaluation. The OSART methods involve not only the examination of documents and the interviewing of staff but also reviewing the quality of performance. It is recognized that different approaches are available to an operating organization for achieving its safety objectives. Proposals for further enhancement of operational safety may reflect good practices observed at other nuclear power plants. An important aspect of the OSART review is the identification of areas that should be improved and the formulation of corresponding proposals. In developing its view, the OSART team discusses its findings with the operating organization and considers additional comments made by plant counterparts. Implementation of any recommendations or suggestions, after consideration by the operating organization and adaptation to particular conditions, is entirely discretionary.
An OSART mission is not a regulatory inspection to determine compliance with national safety requirements nor is it a substitute for an exhaustive assessment of a plant’s overall safety status, a requirement normally placed on the respective power plant or utility by the regulatory body. Each review starts with the expectation that the plant meets the safety requirements of the country concerned. An OSART mission attempts neither to evaluate the overall safety of the plant nor to rank its safety performance against that of other plants reviewed. The review represents a `snapshot in time’; at any time after the completion of the mission care must be exercised when considering the conclusions drawn since programmes at nuclear power plants are constantly evolving and being enhanced. To infer judgements that were not intended would be a misinterpretation of this report.
The report that follows presents the conclusions of the OSART review, including good practices and proposals for enhanced operational safety, for consideration by the Member State and its competent authorities.
Executive Summary
This report describes the results of the OSART mission conducted at Torness Nuclear Power Station in the UK from 22 January to 8 February 2018.
The purpose of an OSART mission is to review the operational safety performance of a nuclear power plant against the IAEA safety standards, make recommendations and suggestions for further improvement and identify good practices that can be shared with NPPs around the world.
This OSART mission reviewed twelve areas: Leadership and Management for Safety; Training and Qualification; Operations; Maintenance; Technical Support; Operating Experience Feedback; Radiation Protection; Chemistry; Emergency Preparedness and Response; Accident Management; Human, Technology & Organizational Interaction; and Long Term Operation.
The mission was coordinated by an IAEA Team Leader and Deputy Team Leader and the team was composed of experts from Belgium, Bulgaria, Canada, Finland, France, Hungary, The Netherlands, Russian Federation, Sweden, United States of America and the IAEA staff members. The collective nuclear power experience of the team was approximately 362 years.
The team identified 19 issues, resulting in 4 recommendations and 15 suggestions. 8 good practices were also identified.
Several areas of good performance were noted:
- The station adopted an Advanced Gas-cooled Reactor fuel floor mock-up in support of improved Fuel Route Training.
- The station developed a Marine Ingress Weather Alert System.
- The station developed Corrosion Cards to support the corrosion programme.
The most significant issues identified were:
- The station should improve its action plans, self-assessment programme, performance targets and measures in a more challenging and aggressive manner.
- The station should improve the quality and practice of using of operating procedures to fully ensure safe station operation.
The station should enhance its screening and categorization process to ensure that events are assigned the appropriate priority and investigated in accordance with their actual or potential significance.
The management of Torness NPS expressed their commitment to address the issues identified and invited a follow up visit in about eighteen months to review the progress.
Introduction and main conclusions
Introduction
At the request of the government of the UK, an IAEA Operational Safety Review Team (OSART) of international experts visited Torness Nuclear Power Station from 22 January to 8 February 2018. The purpose of the mission was to review operating practices in the areas of Leadership and Management for Safety; Training and Qualification; Operations; Maintenance; Technical Support; Operating Experience Feedback; Radiation Protection; Chemistry; Emergency Preparedness and Response; Accident Management; Human, Technology & Organizational Interaction; and Long Term Operation. In addition, an exchange of technical experience and knowledge took place between the experts and their plant counterparts on how the common goal of excellence in operational safety could be further pursued.
The Torness OSART mission was the 199th in the programme, which began in 1982. The team was composed of experts from Belgium, Bulgaria, Canada, Finland, France, Hungary, The Netherlands, Russian Federation, Sweden, United States of America and the IAEA staff members. The collective nuclear power experience of the team was approximately 362 years
Torness is owned and operated by EDF Energy, a subsidiary of EDF S.A. in France. The plant is situated on the east coast of Scotland near the town of Dunbar, approximately 50km east of Edinburgh. The plant consists of two Advanced Gas-cooled Reactors each with an associated turbine generator. Unit 1 commenced commercial operation in 1988 and Unit 2 in 1989. Each unit has a nominal net electrical output of approximately 615 MW and each is connected to the national 400kV power grid. Cooling water is drawn from the North Sea in a once-through cooling cycle. The reactors are normally refuelled on load at reduced reactor power. As a result, maintenance and inspection outages are conducted on a three-year cycle.
Before visiting the plant, the team studied information provided by the IAEA and the Torness station to familiarize themselves with the plant’s main features and operating performance, staff organization and responsibilities, and important programmes and procedures. During the mission, the team reviewed many of the plant’s programmes and procedures in depth, examined indicators of the plant’s performance, observed work in progress, and held in-depth discussions with plant personnel.
Throughout the review, the exchange of information between the OSART experts and plant personnel was very open, professional and productive. Emphasis was placed on assessing the effectiveness of operational safety rather than simply the content of programmes. The conclusions of the OSART team were based on the plant’s performance compared with the IAEA Safety Standards.
The following report is produced to summarize the findings in the review scope, according to the OSART Guidelines document. The text reflects only those areas where the team considers that a Recommendation, a Suggestion, an Encouragement, a Good Practice or a Good Performance is appropriate. In all other areas of the review scope, where the review did not reveal further safety conclusions at the time of the review, no text is included. This is reflected in the report by the omission of some paragraph numbers where no text is required.
Main conclusions
The OSART team concluded that the managers of Torness NPS are committed to improving the operational safety and reliability of their plant. The team found good areas of performance, including the following:
- The station adopted an advanced Gas Cooled Reactor Fuel Floor Mock-Up in support of improved Fuel Route Training.
- The station developed a Marine Ingress Weather Alert System.
- The station developed Corrosion Cards to support the corrosion programme.
Several proposals for improvements in operational safety were offered by the team. The most significant proposals include the following:
- The station should improve its action plans, self-assessment programme, performance targets and measures in a more challenging and aggressive manner.
- The station should improve the quality and practice of using of operating procedures to fully ensure safe station operation.
- The station should enhance its screening and categorization process to ensure that events are assigned the appropriate priority and investigated in accordance with their actual or potential significance.
Torness NPS management expressed a determination to address the areas identified for improvement and indicated a willingness to accept a follow up visit in about eighteen months.
1. Leadership and management for safety
1.2 Integrated management system
The Independent Nuclear Assurance (INA) activities at the station are proving very efficient due to the structure of the organisation, recruitment processes, the in-role training provided, highly developed processes supporting INA activities, and the deployment of tools to support the utility’s model of Internal Regulation. This has ensured that the INA function remains independent from line management. The team recognized this as a good performance.
The team observed that station action plans, self-assessment programme, performance targets and measures are not always sufficiently challenging or aggressively pursued to improve safety performance. Action plan gaps were identified in the fuel route performance and the number of oil leaks, reactor trips, maintenance and control rod backlog, Central Control Room alarms related to faulty equipment and some specific Industrial Safety issues such as transportation. Self-assessment gaps were identified in the Operating Experience and Aging Management programmes. In addition, the plant has experienced an elevated number of repeat significant events. Moreover, challenging targets or measures were not found in the following areas: Tier 1 KPI, Fire index, OE and Industrial Safety. The team made a recommendation in this area.
Detailed leadership and management for safety findings
1.2 Integrated management system
-
1.2(1) Issue: The station’s action plans, self-assessment programme, performance targets and measures are not always sufficiently challenging or aggressively pursued to improve safety performance.
- Lack of challenging action plans to improve performance has been identified in the
following areas:
- – The fuel route performance is recognized by the plant Senior Management as one
of the main challenges facing the station. It has become a primary focus area of the
Business Plan, however the station is facing difficulties to improve in the
following areas:
- – The action plan to improve the Fuel Route operations is more qualitative than result oriented and does not include performance indicators and action plan status.
- – The aggregated Fuel Route performance indicator shows a declining trend over the last 5 years.
- – One of the most significant equipment failures during 2017 second semester concerned the fueling machine hoist brake no longer complying with the safety case requirements resulting in an elevated potential for damaged fuel. This was self-identified by the station; however, Independent Nuclear Assurance (INA) considered it necessary to bring this event to the awareness of the plant senior management because the issue was not being addressed in a timely manner.
- – An INA corporate audit identified weaknesses in the tolerance to degraded standards and the lack of cross-functional engineering walk downs of the station.
- – Unresolved problems with Fuel Route seismic clamps have challenged the plant’s daily operations since 2012.
- – The Oil Leak Improvement plan established in May 2016 has not been effective in addressing the performance issue. At the time of the mission the number of oil leaks was at 56 against a target of 30, however the indicator is green in the Operational Focus Index.
- – In 2017, the plant identified a lack of challenging action plans leading to extended diesel generator unavailability. There has been a significant delay in the implementation of the diesel generator action plan.
- – The two last manual reactor trips were directly linked to maintenance activities and were due to loose connections on Single Point Vulnerability (SPV) equipment (repeat event). The last automatic trip, currently under investigation, was related to procedural, design knowledge and faulty equipment issues. The cumulative trip average at the plant for the past 2 years is over 0.5, this being the average result in the nuclear industry.
- – The non-outage defect backlog was 692 in December 2017, resulting in the Tier 2 KPI being red. The control rod backlog KPI Tier 2 was also red at the end of 2017 with a backlog of 8 rods against a target of 2.
- – Central Control Room Alarm Improvement plans have not been successful in addressing the following performance issues:
- – Although the OFI (Operational Focus Index) KPI on Central Control Room (CCR) alarms is showing green, there are 32 alarms related to faulty equipment in the Central Control Room. Common alarms are present on the same equipment on both units.
- – Out of a total of 32 alarms, 18 could be fixed online.
- – Analysis of the 2016 and 2017 accident record list shows that injuries to heads, hands and legs including ankles are predominant. The plans developed to address related training issues are not specific enough to support improvement in these persistent industrial safety related challenges.
- – Transportation at the plant is a long-standing challenge. There have been 9 events of vehicle collision or near misses in the car park since 2013 and 12 collisions or near misses at the A1 junction at the entry road to the site since 2013. Although plans are in place the issue remains a challenge for the plant.
- – The fuel route performance is recognized by the plant Senior Management as one
of the main challenges facing the station. It has become a primary focus area of the
Business Plan, however the station is facing difficulties to improve in the
following areas:
- Lack of Self-assessment has been identified in the following areas:
- – Over the past 3 years, the plant experienced an elevated proportion of repeat significant events, recurring issues or events for which a significant amount of past OE could have helped to prevent or minimize the event. In some cases the OE process has not been effective in preventing repeat events, but in the last 3 years there has not been a Self-Assessment of the effectiveness of the OE programme.
- – Over the last 3 years, the plant has not performed any self-assessment exercise of the aging management programme.
- – There is no overall systematic self-assessment plan. There is only a draft plan covering 2018.
- Challenging Targets or measures were not found in the following areas:
- – Although fire is a significant nuclear safety hazard at any nuclear power plant, the Fire Index (a composite KPI) is the only Tier 2 KPI on fire safety. The following metrics were not used in 2017 in the Fire Index KPI: FEC03 (minor fire events); FEC06 (Smouldering fire, or evidence of fire having occurred); F45 (passive fire protection reliability)
- – More than one third of the KPIs are regularly met even though their target is zero.
- – OE targets and measures:
- – There is also no KPI covering the screening process for events.
- – The plant target to complete root cause analyses is 50 days, however the KPI shows green if the root cause analysis is completed in 54 days.
- Lack of challenging Industrial Safety measures have been identified in the following
areas:
- – The Industrial Safety key risk tool used by the plant does not focus attention on the most common risks encountered at the plant such as Critical risks, Time Out for Personal Safety key risks and high probability risks (handling, rigging and lifting, slipping/tripping/falling hazards, lack of PPE…). The tool directs attention towards compliance with regulation issues rather than minimizing field industrial safety hazards.
- – Over the past 4 years the number of Industrial Safety Category 3 events, even though less significant, has been unexpectedly lower than the number of Category 2 events. Category 3 events are not adequately identified and reported at the plant to identify adverse trends.
- Lack of aggressive action plans, a rigorous self-assessment programme and suitable performance targets and measures could lead to some known safety related challenges not being resolved in a timely manner.
- Lack of challenging action plans to improve performance has been identified in the
following areas:
Recommendation: The station should ensure that its action plans, self-assessment programme, performance targets and measures are sufficiently challenging and aggressively pursued to improve safety.
IAEA Bases:
GSR Part 2
4.4. Senior management shall ensure that measurable safety goals that are in line with these strategies, plans and objectives are established at various levels in the organization.
4.5. Senior management shall ensure that goals, strategies and plans are periodically reviewed against the safety objectives, and that actions are taken where necessary to address any deviations.
6.1. The effectiveness of the management system shall be monitored and measured to confirm the ability of the organization to achieve the results intended and to identify opportunities for improvement of the management system.
6.3. The causes of non-conformances of processes and the causes of safety related events that could give rise to radiation risks shall be evaluated and any consequences shall be managed and shall be mitigated. The corrective actions necessary for eliminating the causes of nonconformances, and for preventing the occurrence of, or mitigating the consequences of, similar safety related events, shall be determined, and corrective actions shall be taken in a timely manner shall be monitored and shall be reported to the management at an appropriate level in the organization.
- 6.7. The management system shall include evaluation and timely use of the following:
- – Lessons from experience gained and from events that have occurred, both within the organization and outside the organization, and lessons from identifying the causes of events.
SSR-2/2 (Rev.1):
- 3.2. The management system, as an integrated set of interrelated or interacting components for establishing policies and objectives and enabling the objectives to be achieved in an efficient and effective manner, shall include the following activities:
- – (e) Review activities, which include monitoring and assessing the performance of the operating functions and supporting functions on a regular basis. The purpose of monitoring is: to verify compliance with the objectives for safe operation of the plant; to reveal deviations, deficiencies and equipment failures; and to provide information for taking timely corrective actions and making improvements. Reviewing functions shall also include review of the overall safety performance of the organization to assess the effectiveness of management for safety and to identify opportunities for improvement.
- 5.33. The operating experience programme shall be periodically evaluated to determine its effectiveness and to identify any necessary improvements.
NS-G-2.11:
- 8.2. The operating organization or licensee should periodically review the effectiveness of the process for the feedback of experience. The purpose of such a review is to evaluate the effectiveness of the overall process and to recommend remedial measures to resolve any weaknesses identified. Indicators of the effectiveness of the process should be developed.
- 8.3. The following should also be done as part of the self-assessment review:
- – It should be verified that corrective actions arising from the process for the feedback of operational experience are being implemented in a timely manner;
- – The effectiveness of the solution of the original problems and the prevention of their recurrence should be evaluated;
- – Recurring events should be reviewed to identify whether improvements can be made in the process for the feedback of operational experience.
2. Training and qualifications
2.1. Organization and functions
The station’s improvement plans for training Top Issues are clearly identified and in progress. The team noted, however, that due dates had not been established to assist in the timely resolution of these issues. For example: The station’s Training Committee Performance Issues document identifies the top issues in each training area yet there are no target dates by which to eliminate the issue. Additionally, some improvement activities do not have due dates for key milestones. For example: Maintenance Continuing Training has been scheduled for the next 5 years, however there are no due dates established to design and develop the Continuing Training courses needed to meet the schedule. The team encouraged the station to establish due dates for overall training performance gaps and some key strategic training initiatives to drive timely resolution.
2.2. Qualification and training of personnel
The station has developed a highly visible emphasis on developing and reinforcing strong fundamentals (Monitoring, Control, Conservatism, Teamwork and Knowledge). Their specific relevance to the training is discussed at the start of every training class and reenforced throughout the training. A simple form of the fundamentals has been developed against which personnel can be evaluated in each fundamental area. This form is used for evaluation of performance during formal assessments in the simulator and to capture trainee feedback in various other training areas. The team considered this a good performance.
Following an in-depth analysis of incidents and events involving Lifting and Rigging, the station established an accredited training centre for Lifting and Rigging, Fork Lift Truck Operation and the use of Mobile Elevating Work Platforms to address an identified performance gap in these areas. This resulted in the plant receiving a Globally Recognized Accreditation in Lifting & Rigging in 2015 and annual re-accreditation since then. As well as the improvement in the quality of the training the plant now has the flexibility to conduct all such training inhouse. The team considered this a good performance.
The station has created a mock-up of the fuel floor of the reactor. The mock up allows training to be carried out in a controlled, low contamination and radiation environment that does not compromise safety. Trainees can learn without consequences in the event of an error or misunderstanding. The facility has been used in the training of Fuel Route Operations Engineers, Fuel Route Technicians and Health Physics Monitors. The team considered this a good practice.
Detailed training and qualification findings
2.2. Qualification and training of personnel
2.2(a) Good Practice: Advanced Gas-cooled Reactor Fuel Floor Mock-Up in support of improved Fuel Route Training.
The station has created a mock-up of the fuel floor of the reactor. The mock up allows training to be carried out in a controlled, low contamination and radiation environment that does compromise safety. Trainees can learn without consequences in the event of an error or misunderstanding. The facility has been used in the training of Fuel Route Operations Engineers, Fuel Route Technicians and Health Physics Monitors in tasks such as:
- – Reactor fuel floor preparations
- – Control rod actuator brake fitting and removal
- – Fuel closure motor drive unit fitting and removal
- – Fuel closure pressure leak tests
- – Thermocouple tests
- – Radioactive contamination training
- – Human Performance Tools and Fundamentals
The mock up is used for initial and continuing training, On-the-Job Training, Task Performance Evaluation along with In-Service Inspection Training and Just-in-Time Training for outage rehearsals. This contributed to reducing the In-Service Inspection Programme for statutory outages by 3 days in 2017.
Station performance improvement is evident through the reduction in events related to fuel floor preparations, events during control rod floor preparation and excellent radiological safety during refuelling and reactor outages. The number of related personal contamination events reduced from 18 in 2014 to 8 in 2017.
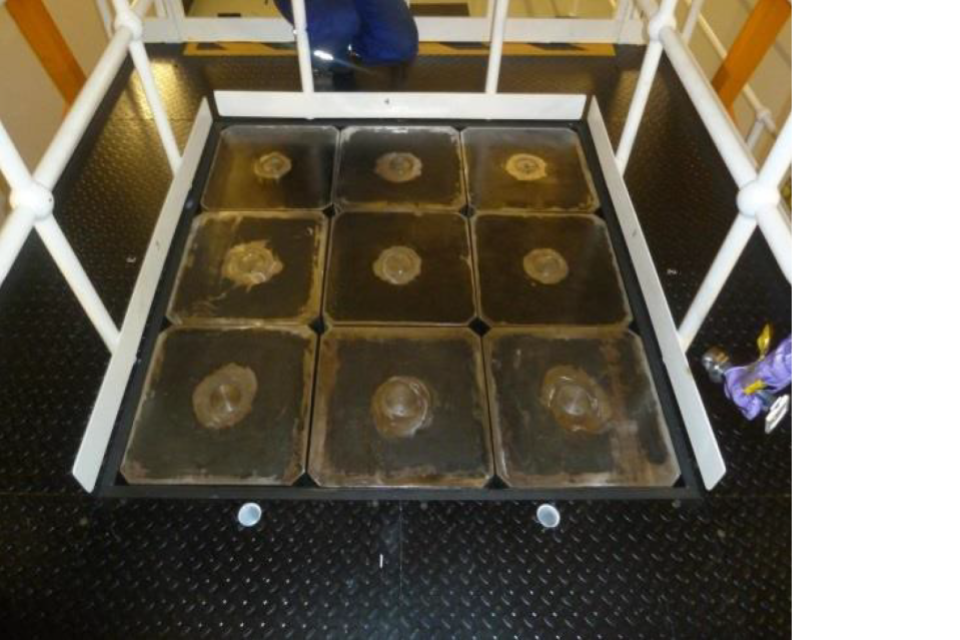
Fuel Floor Simulator – Floor Intact
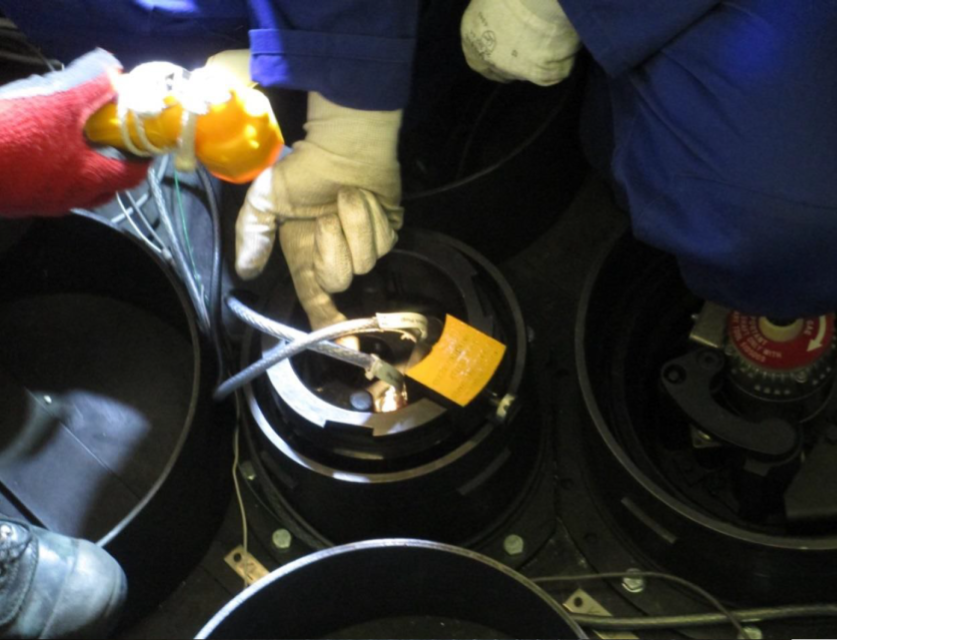
Trainees checking control rod cables – simulated contamination control area
3. Operations
3.1. Organization and functions
The operations organizational structure is robust with clear responsibilities. However, known demographic issues pose a challenge to the staffing of the operational department. To mitigate the anticipated loss of experience, monitoring and forecasting has been put in place to identify areas in which recruitment and training will need to be focussed. For the operations staff this has taken the form of Staffing Resilience Spider Charts which allow the authorisations held by each shift to be visualised in an easy to understand format. They can also be used to highlight potential future staffing shortfalls and allow proper planning to maintain compliance with site licence conditions. Using these charts and other methods of analysing the Operations staff data, periods of increased recruitment can be predicted well in advance of any risk to the station. The team recognized this as a good practice.
3.2. Operations equipment
The station recorded an elevated number of safety related configuration events between 2014 and 2016. While some were caused by operational activities, more than 50% were related to plant modification and maintenance activities, which highlights the cross-functional nature of the issue. To address this issue, the plant has reinforced the local Configuration Management Working Group (CMWG). The CMWG is now an effective cross-functional forum for driving Configuration Management improvements. The team reviews a ‘Heat Map’ monthly, this highlight ‘hot spot’ in the number of different misconfiguration condition reports across all departments and allows targeted analysis. As a result the numbers of inappropriate configuration events have recently significantly decreased. The practice was shared with fleet and is now used by all EDF Energy nuclear stations. The team recognized this as a good performance.
3.3. Operating rules and procedures
The team noted that quality and the practice of using operating procedures do not always ensure safe station operation. Gaps identified in some operating procedures could lead to human error-likely situations. Also some deviations in procedural use and adherence were observed. The team made a recommendation in this area.
3.4. Conduct of operations
Marine Ingress, related to sea weed and jelly fish, have caused operational issues during the life of the plant. The plant has implemented a comprehensive process to prepare and respond to marine ingress events. Updates have been made to the plant documentation associated with the marine ingress risk indicator. Also, a review of the information available to the Central Control Room, to aid decision making, was also carried out. In addition, the station has introduced a set of equipment improvements. The team identified this as a good practice.
Although the plant has a well-developed system of operator rounds supported by management coaching in the field, it is mainly focused on equipment in their own area of responsibility. The team noticed tolerance to minor deficiencies in the field and lack of challenging corrective actions being taken in a timely manner. The conduct and supervision of operator rounds is not always undertaken at a sufficient level to detect and report minor plant deficiencies. The team made a suggestion in this area.
The team observed that station fuel route activities do not always ensure rigorous application of the foreign materials exclusion (FME) program to prevent the intrusion of foreign materials into station systems and components. Gaps identified include inconsistent use of logs for tools used in FME areas, ineffective barriers around FME areas allowing introduction of foreign material into equipment, and use of transparent plastic in the fuel storage pond area. The team made a suggestion in this area.
3.5 Work control
The station has adopted a high standard work management process. However, the implementation of this process can be further developed to ensure the operators in the field are kept informed of plant status, repairs and to facilitate positive feedback and ownership of plant defects. The team encouraged the station to enhance the work management process to ensure that shift personnel are aware of ongoing work (scaffold, safety documents, temporary storage, defects, etc.) on the plant and the necessary repairs are planned and executed as scheduled.
3.6. Fire prevention and protection programme
A computer Fire System Program has been designed that allows a level by level view of the status of Fire Protection on all areas of site. The system can be accessed from a station overview page which can go into each location on-site and show the status of the fire protection system. The program also allows informed decisions to be made on the cumulative effect of fire protection systems being isolated or defective. The team identified this as a good practice.
The team noted that station processes for the control of combustible materials are not being fully implemented in the field to minimize fire burden and associated fire risk. Unauthorized storage of transient combustible materials was observed in multiple station compartments. Several lay down areas were not assessed and authorized. The team made a suggestion in this area.
The station has not developed firefighting strategies for each individual area of the plant identified as important to safety. The team encouraged the station to develop firefighting strategies for all areas identified as important to safety.
Detailed operations findings
3.1. Organization and functions
3.1(a) Good practice: Succession planning on operations using spider diagrams.
To mitigate against anticipated loss of experience, monitoring and forecasting has been put in place to identify areas in which recruitment and training will need to be focussed. For the operations staff this has taken the form of Staffing Resilience Spider Charts which allow the authorisations held by each shift to be visualised in an easy to understand format. They can also be used to highlight potential future staffing shortfalls and allow proper planning to maintain compliance with site licence conditions.
Different shift structures can be evaluated against an assessed optimal authorisation level, this allows for a direct comparison between shifts and can identify any potential shortfalls or areas for improvement. The chart in Figure 1 below is an example of the current ‘fingerprint’ of a central control room team showing which areas are in the green optimal zone, and which areas could be improved in the amber zone. It can also highlight members of staff that are currently training to show how the graph will look upon the attainment of their authorisation.
Figure 1. Current authorisation diagram for a shift
(Acronyms: CCRS – Central Control Room Supervisor, RDE – Reactor Desk Engineer, FRE – Fuel Route Engineer, PE – Plant engineer, SAP HV – Senior Authorised Person High Voltage, SAP NR – SAP Nuclear Radiation, NOISS – Nominated Oxygen Injection System Supervisor)
Figure 1: C Shift - Current - Data from radar chart
Name | Shift Manager | CCRS | RDE | FRE | PE | SAP HV | SAP NR | NOISS |
---|---|---|---|---|---|---|---|---|
Person 1 | x | x | - | - | - | x | x | x |
Person 2 | x | x | - | - | x | x | - | x |
Person 3 | - | x | x | - | x | x | x | x |
Person 4 | - | - | x | - | x | x | - | - |
Person 5 | - | - | - | x | t | - | t | - |
Person 6 | - | - | x | - | x | x | - | x |
Person 7 | - | - | - | x | x | x | t | - |
Person 8 | - | - | x | - | - | - | - | - |
Authorised | 2 | 3 | 4 | 2 | 5 | 6 | 2 | 4 |
Optimal | 2 | 3 | 4 | 2 | 8 | 3 | 3 | 3 |
Current Shift Authorisation |
100% | 100% | 100% | 100% | 63% | 200% | 67% | 133% |
Training | 0 | 0 | 0 | 0 | 1 | 0 | 2 | 0 |
Projected | 2 | 3 | 4 | 2 | 6 | 6 | 4 | 4 |
Projected Shift Authorisation | 100% | 100% | 100% | 100% | 75% | 200% | 133% | 133% |
This allows for the same goals all the way through the business to be visible and helps to drive operational excellence through the station. Clear and concise information and KPIs where applicable are shown to allow a common understanding of how everyone contributes to the overall business outputs and targets for improvement.
Figure 2. Forecast authorisation diagram for 2021
(See Acronyms above)
Figure 2: C Shift - 2021 - Data from radar chart
Name | Shift Manager | CCRS | RDE | N3 | D2 | SAP HV | SAP NR | NOISS |
---|---|---|---|---|---|---|---|---|
Person 1 | x | - | - | - | - | x | x | x |
Person 2 | - | - | - | - | - | - | - | - |
Person 3 | - | x | - | - | x | x | x | x |
Person 4 | - | x | x | - | x | x | - | - |
Person 5 | - | - | x | - | - | - | - | - |
Person 6 | - | - | x | - | x | - | - | x |
Person 7 | - | - | - | - | - | - | - | - |
Person 8 | - | - | - | x | x | - | - | - |
Authorised | 1 | 2 | 3 | 2 | 4 | 3 | 2 | 3 |
Optimal | 2 | 3 | 4 | 2 | 8 | 3 | 3 | 3 |
Current Shift Authorisation |
50% | 67% | 75% | 50% | 50% | 100% | 67% | 100% |
Training | 0 | 0 | 0 | 0 | 0 | 0 | 0 | 0 |
Projected | 1 | 2 | 3 | 1 | 4 | 3 | 2 | 3 |
Projected Shift Authorisation | 50% | 67% | 75% | 50% | 50% | 100% | 67% | 100% |
The chart on the right of Figure 2 shows how the shift will look in 2021 if no action is taken to maintain the current staffing levels. The forecast can be selected out as far as 2030 and automatically updates to reflect the predicted shift structure at that point in time considering any anticipated retirements or authorisation changes. Using these charts and other methods of analysing the Operations staff data, periods of increased recruitment can be predicted well in advance of any risk to the station, allowing the continuation of safe, reliable generation. This tool is used in succession planning workshops as the framework for shift staffing and training priority. The resultant information feeds directly into the operations staffing and succession plans.
3.3. Operating rules and procedures
-
3.3(1) Issue: The quality of operating procedures and the consistency of their use by plant personnel does not always ensure safe station operation.
- The team noted the following:
- – Work instruction SUT24(G) to test the Trip Control Valves requires three persons to perform the test. However, only two engineers were observed performing this test.
- – The procedure for secondary shutdown system nitrogen injection valves test requires checking the nitrogen pressure, which actuates the trip control valves, on three gauges. According to the procedure, the pressure should be 7.5 bars. However, the pressure in supply nitrogen tank is 7.2 bars and procedure does not require checking this pressure before the test. The procedure quality was not challenged by the personnel performing the test.
- – During performance of the procedure for secondary shutdown system nitrogen injection valves test, the pressure gauges indicated between 5.5 and 6.0 bars. However, two separate procedural steps to check for a pressure gauge indication of 7.5 bar were ticked as ‘OK’ by a Reactor Desk Engineer. The second individual who provided a peer check did not challenge this behaviour.
- – 2CX Invertor return to service was performed in accordance with Work instruction ‘Changeover to Maintenance Bypass condition and Return to Service of Inverter’. This procedure is not specific to each inverter and some decisions needed to be made promptly in field.
- – During execution of the plant item operating instruction ‘Verification of PTSE’ (PTSE - post trip sequence equipment) the Reactor Desk Engineer in the CCR did not complete the fields ‘time of trip’ and ‘signature on verification of PTSE operation’. Several steps were not completed (not marked). The completion of the procedure was not confirmed and authorized by the CCR supervisor by signature.
- – The plant item operating instruction ‘Operate technicians Actions Following a Unit Trip – Reactor plant operators’ and ‘Operate technicians Actions Following a Unit / Turbine Trip – WTP, Turbine & Outside plant operators’ should be used by field operators to check and confirm status of the parameters and equipment after reactor trip. However, after a reactor trip on 29/01/2018 there was no evidence in the station log or CCR documentation that these procedures had been used.
- – During execution of the working procedure ‘On load testing of LP Exhaust trip temperatures’ one of steps was missed resulting in unexpected indications.
- – One of the steps of the procedure ‘On load testing of LP Exhaust trip temperatures’ requires turning of a switch on the ‘LP Exhaust on Load Test’ panel to ‘Section 1 Position 1’. However, the positions labelled from top down are ‘NR012’, ‘NR013’, ‘NR014’ etc. This caused difficulties for the engineer performing the test in selecting the correct position of the switch.
- – Reactor sea water pump 1BY motor control buttons inside ‘RSW Pump BY Rack’ 1/679 in the circulating water pump house have been labelled by hand: green button – ‘OFF’, red button – ‘ON’. In the related surveillance test operating procedure these buttons are described as ‘STOP’ and ‘START’.
- – The station procedures do not require incorporating long term temporary instructions into related operating procedures. One of these supplemental procedures has been used in the Condensate Polishing Plant control room since 2010 without being integrated into the main procedure and involves safety related manipulations.
- – The station had an event in April 2017 ‘New Fuel Assembly L35 build order incorrect’ caused by incorrect use of a step-by-step procedure by Fuel Route staff.
- Without high quality operating procedures and their rigorous and consistent use, safe and reliable operation could be compromised.
- The team noted the following:
Recommendation: The station should improve the quality and consistency of use of operating procedures to ensure safe and reliable station operation.
IAEA Bases:
SSR-2/2 (Rev.1):
Requirement 26: Operating procedures:
Operating procedures shall be developed that apply comprehensively (for the reactor and its associated facilities) for normal operation, anticipated operational occurrences and accident conditions, in accordance with the policy of the operating organization and the requirements of the regulatory body.
7.1. The level of detail for a particular procedure shall be appropriate for the purpose of that procedure. The guidance provided in the procedures shall be clear and concise and, to the extent possible, it shall be verified and validated. The procedures and reference material shall be clearly identified and shall be readily accessible in the control room and in other operating locations if necessary. They shall be made available to the regulatory body, as required. Strict adherence to written operating procedures shall be an essential element of safety policy at the plant.
7.4. Operating procedures and supporting documentation shall be issued under controlled conditions, and shall be subject to approval and periodically reviewed and revised as necessary to ensure their adequacy and effectiveness. Procedures shall be updated in a timely manner in the light of operating experience and the actual plant configuration.
3.4. Conduct of operations
3.4(a) Good practice: Marine Ingress Weather Alert System
Marine Ingress into cooling water intakes, primarily related to seaweed and jelly fish, has caused operational issues during the life of the plant. Episodes of significant seaweed ingress have challenged nuclear safety and have led to reactor trips. The plant has implemented a comprehensive process to prepare for and respond to marine ingress events. Updates have been made to the plant documentation associated with the marine ingress risk indicator. This indicator is based on meteorological forecasts of wind direction, wave height and wave direction. In addition, a review of the information available to the Central Control Room, to aid decision making, was also carried out.
- Improvements implemented include:
- – A new comprehensive procedure and flow chart place which defines the process to assess marine debris risk to aid operations personnel to take appropriate mitigating actions to minimise the potential impact on the station cooling water systems.
- – Improved drum screen and circulating water pump instrumentation to give accurate and reliable indications to the Central Control Room to support operator decision making.
- – Enhanced drum screen protection system improvement - prevents drum screen failures, loss of reactor sea water system flow and automatic trips from condenser circulating water pass loss of prime, by preventing excessive drum screen differential pressure.
- – Drum screen wash water augmentation uses the reactor sea water system to augment wash water supply which has addressed the lack of redundancy on existing system and greatly improves wash water availability.
- – Installation of a raking system to reduce the likelihood of high drum screen differential pressure developing by removing larger weed upstream of the drum screens.
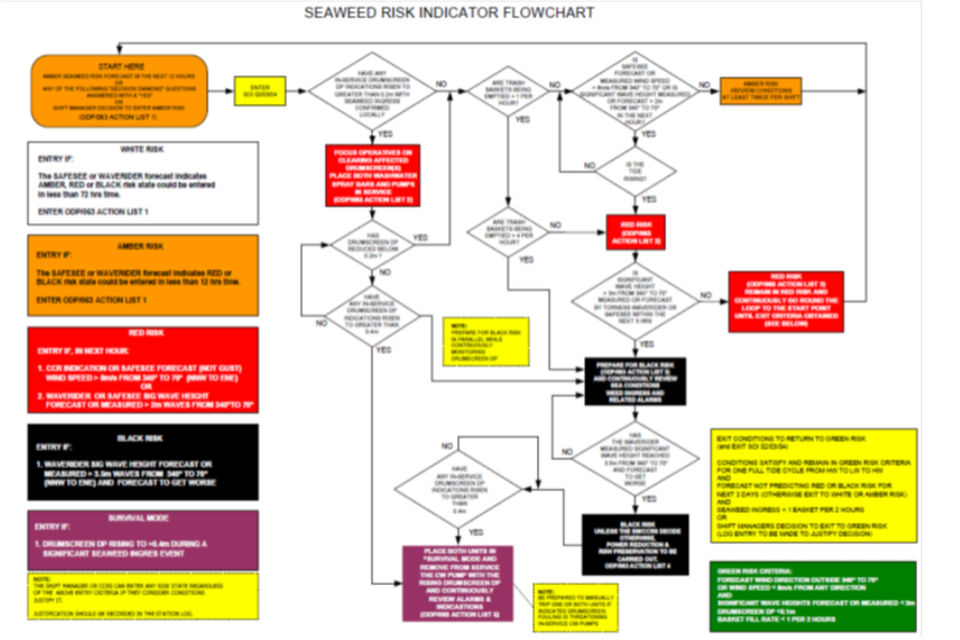
-
3.4(1) Issue: The conduct and supervision of field operations is not always effective in ensuring that minor plant deficiencies are identified and reported.
- The plant has a well-developed system of operator rounds supported by management coaching in the field.
- However, the team noted the following deficiencies that were not identified and reported or challenged by plant personnel:
- General housekeeping:
- – Steel beam left on the floor in the turbine hall + 37 m level not far from the hatchway to 0 m.
- – During an observation of the turbine hall outside area, concrete debris was visible on the stairs to the Relief Valve and the ceiling is crumbling.
- – During an observation of the operator manipulation on TG1 lubricating oil system, heavy parts (valve, shaft-coupling) had been dismantled and left on top of the main oil tank.
- – In the turbine hall basement an FME bag had been left in a drainage tray.
- – During an observation several previously identified, reported, long standing deficiencies were discovered in the electrical cabinets and cable corridors. The defect tags were dated between 2012 and 2016.
- – A lock and the chain was observed inside an FME area in the Charge Hall during a plant tour. This deviation was not identified and fixed by field operators during the following week.
- Equipment status:
- – The Central Control Room zone I central processing unit (CPU) battery charger current measurement failed (oscillated between ends) but there was no Defect tag in place.
- – The turbine hall 0 m level area: A Padlock was missing from LP Heater Steam Isolating Valve Pneumatic Control Panel and 2 large screws were found inside the Control Panel.
- Leakages:
- – Turbine hall 0 m level area: Oil puddles were visible at two locations on the turbine jacking oil pumps.
- – In the turbine hall on the -4,5 m cable hall (TH1B1-10) fire system water leakage was found and the water was dripping onto cables.
- – On the TG1 lubricating oil system, several small oil leakages were observed on various equipment, most of them were collected using absorbent matting.
- – All the three oil pumps for the AX Diesel (AX, DGAX-OLD-A3, DG-AX1, DGAX2) have leakage from the seals, but none of the leaks were reported by station personnel.
- Storage areas:
- – At the turbine hall 0m level a heavy item storage space is in the central area close to the hatch to the underground level. Items could fall over the barriers.
- – An unauthorized storage place is located storing extension cords and flexible pipes in a corner of the Turbine Hall at the -4,5 m level.
- Labelling of safety related equipment:
- – In turbine hall + 37 m the ID label R1-AV-0107C (at Reserve Feedwater Tank) was not fixed on the equipment.
- – Multiple cases of broken, painted, handwritten not fixed or missing equipment labelling.
- – According to the database of Torness NPS 2017 Site excellence internal evaluation the poorest performance values are at areas of cleanliness, fire prevention, firefighting and electrics.
- Without consistent and timely identification and reporting of minor deficiencies in the field the condition of Structures Systems and Components could gradually deteriorate.
Suggestion: The station should consider improving the conduct and supervision of field operations to ensure that minor plant deficiencies in the field are identified and reported.
IAEA Bases:
SSR-2/2 (Rev.1):
5.3. The plant management should ensure that all valves, switches, breakers and components are labelled using the same labelling nomenclature as that prescribed in current design documents. Furthermore, operations procedures and documents should also reflect the same nomenclature. When discrepancies are found, they should be reported and corrected in accordance with the established procedure. To assist in the management of the labelling programme, the number of discrepancies awaiting correction should be tracked and monitored.
5.31. The operating organization shall be responsible for instilling an attitude among plant personnel that encourages the reporting of all events, including low level events and near misses, potential problems relating to equipment failures, shortcomings in human performance, procedural deficiencies or inconsistencies in documentation that are relevant to safety.
7.5. A system shall be established to administer and control an effective operator aids programme. The control system for operator aids shall prevent the use of non-authorized operator aids and any other non-authorized materials such as instructions or labels of any kind on the equipment, local panels, boards and measurement devices within the work areas. The control system for operator aids shall be used to ensure that operator aids contain correct information and that they are updated periodically reviewed and approved.
Requirement 28: Material conditions and housekeeping:
The operating organization shall develop and implement programmes to maintain a high standard of material conditions, housekeeping and cleanliness in all working areas.
7.10. Administrative controls shall be established to ensure that operational premises and equipment are maintained, well lit and accessible, and that temporary storage is controlled and limited. Equipment that is degraded (owing to leaks, corrosion spots, loose parts or damaged thermal insulation, for example) shall be identified, reported and corrected in a timely manner.
7.12. The operating organization shall be responsible for ensuring that the identification and labelling of safety equipment and safety related equipment, rooms, piping and instruments are accurate, legible and well maintained, and that they do not introduce any degradation.
-
3.4(2) Issue: Fuel route activities do not always ensure rigorous application of the foreign materials exclusion program to prevent the intrusion of foreign materials into station systems and components.
- The station has implemented a ‘Company specification on Foreign Materials Exclusion’ (FME) providing necessary requirements and instructions to prevent the introduction of foreign materials into station mechanical, electrical and control & instrumentation systems and components.
- However, the team noted the following:
- – Several foreign items (plastic pipe, tape, cover) found on the floor inside the Unit 2 pile cap FME area in the Charge Hall.
- – The plastic bin with radioactive waste was not secured inside the Unit 2 pile cap FME area in the Charge Hall. This can lead to dissemination of small waste in the case of a seismic event.
- – Open equipment in the irradiated fuel buffer store in the Unit 2 Charge Hall (FME area) was observed not covered while no work was being performed.
- – The refuelling machine is not subject to the FME program during normal operation, however it moves frequently or can be positioned above FME areas and open equipment in the Charge Hall. No precaution has been taken to prevent items falling from the machine into open equipment.
- – Workers involved in maintenance work in the Charge Hall on the refuelling machine believe that it is not needed to maintain an FME tool log if the work is not on the machine pressure vessel.
- – A Purge Air Filter for Vessel Entry was being prepared for installation in the Charge Hall with no visible barriers or signs related to FME protection zone, as required by the station procedure ‘Company specification on Foreign Materials Exclusion’. The working area was partially fenced with an ordinary tape barrier. Unnecessary tools and items were present and a tool was lying on the floor inside the fenced area.
- – There are no expectations for operations personnel to control FME program implementation by maintenance staff during routine field rounds, only as a part of observations and coaching program.
- – The last entry on 08/01/2018 in the FME control log for the ‘High risk FME area’ in the New Fuel Build Cell showed that a working party logged tools into the area, but there was no corresponding entry for their removal.
- – Unnecessary items and foreign materials were observed inside a ‘High risk FME area’ in the New Fuel Build Cell, such as locker keys (with tags) and a bolt.
- – Personnel were observed working in the Fuel Storage Pond area without maintaining the appropriate FME control log.
- – Transparent plastic is widely used in Fuel Storage Pond area.
- – The barrier around the Fuel Storage Pond is not solid and does not protect the pond from debris.
- – Debris was observed in various places around the Fuel Storage Pond.
- – Chairs on the crane above the Fuel Storage Pond are not secured to prevent them falling into the pond.
- Without rigorous application of an effective foreign material exclusion programme to fuel route activities, the potential for FME intrusion could be significantly increased.
Suggestion: The station should consider ensuring rigorous application of the foreign materials exclusion program to the fuel route activities to prevent the intrusion of foreign materials into station systems and components.
IAEA Bases:
SSR-2/2 (Rev.1):
Requirement 28: Material conditions and housekeeping:
The operating organization shall develop and implement programmes to maintain a high standard of material conditions, housekeeping and cleanliness in all working areas.
7.11. An exclusion programme for foreign objects shall be implemented and monitored, and suitable arrangements shall be made for locking, tagging or otherwise securing isolation points for systems or components to ensure safety.
NS-G-2.5:
3.9. The areas for the handling and storage of fresh fuel should be maintained under appropriate environmental conditions (in respect of humidity, temperature and clean air) and controlled at all times to exclude chemical contaminants and foreign materials.
4.2. The steps necessary to assemble fresh fuel and to prepare it for use in the reactor should be specified in the procedures, including any arrangements for holding it in intermediate storage. Only approved fuel should be loaded into a reactor core. Checks should be carried out to confirm that the fuel has been assembled correctly. In all procedures for fuel handling and maintenance, it should be ensured as far as possible that no foreign material is introduced into the reactor.
5.19. A policy for the exclusion of foreign materials should be adopted for all storage of irradiated fuel. Procedures should be in place to control the use of certain materials such as transparent sheets, which cannot be seen in water, and loose parts.
NS-G-2.14:
- 4.36. Factors that should typically be noted by shift personnel include:
- – Deterioration in material conditions of any kind, corrosion, leakage from components, accumulation of boric acid, excessive vibration, unfamiliar noise, inadequate labelling, foreign bodies and deficiencies necessitating maintenance or other action;
6.20. Plant housekeeping should maintain good conditions for operation in all working areas. Working areas should be kept up to standard, well lit, clean of lubricants, chemicals or other leakage and free of debris; the intrusion of foreign objects should be prevented and an environment should be created in which all deviations from normal conditions are easily identifiable (such as small leaks, corrosion spots, loose parts, unauthorized temporary modifications and damaged insulation). The effects of the intrusion of foreign objects or the long term effects of environmental conditions (i.e. temperature effects or corrosion effects or other degradations in the plant that may affect the long term reliability of plant equipment or structures) should be evaluated as part of the plant housekeeping programme.
3.6. Fire prevention and protection programme
3.6(a) Good practice: Fire System Program
A computerized Fire System Program has been designed that allows a level by level view of the status of Fire Protection on all areas of site.
- The system can be accessed from a station overview page and show the status of the fire protection system at each location on-site. It shows if there are any defects on the system, if the system is isolated and provides a link which gives details to the defect attached to the system. The system takes information from live plant such as the signals being received from fire alarm panels and deluge valves. This allows for live up to date information on the status for the panels and valves. The system also highlights isolations on fire systems as well as any identified defects on control panels and valves thus providing a live view of the health of the Fire Protection system on-site.
- – The Program provides the station with live up to date information on the health of all fire protection systems, in one place.
- – Allows informed decisions to be made on the accumulative effect of fire protection systems being isolated and or defective.
- – Provides details of the zone and panel / valve of all fire systems on-site.
- This has contributed to a greater focus on Fire Safety System performance as demonstrated by an improving trend in the station’s Fire Safety Focus Index, which includes a measure for fire events and near misses, during 2017 (improving from 77 in January 2017 to 83 in December 2017, above the station target of 82).
Figure 1: General Layout of the Station
Figure 2: Detailed view of the Fire Station Systems Status in Maintenance Workshop Area
-
3.6(1) Issue: The station processes for the control of combustible materials are not fully implemented in the field to minimize fire burden and associated fire risk.
- The station has established a process to evaluate, authorize and control combustible and flammable materials. ‘Company specification: Operator plant tours’ requires control of the fire loading of compartments. Also, the station has established requirements for fire patrols. According to ‘Company specification: Site Excellence in material condition’, a review of contents and time limits of lay down areas shall be carried out during normal area tours, walkdowns, inspections, and operator tours.
- However, the team noted the following:
- – The Generation Team Leader does not expect field operators to observe and check lay down areas when doing the regular plant tours although it is required by the station procedure.
- – Several lay down areas in Reactor 1 and 2 buildings and in the Turbine Hall were observed without a ‘Lay down area authorization form’ as required by the station procedure. Combustible materials such as wooden pallets, wooden beams, cardboard boxes, plastic pipes, canisters, and scaffold end caps were observed inside these areas.
- – An approved lay down area in the turbine hall loading bay contains unauthorized wooden pallets.
- – Approved lay down area T0243 in the Outside Plant had an expired authorization date.
- – The Turbine Lubricating Oil Store, designed as a separate compartment in turbine hall, level -9.00m (laydown area T0029) is authorized for storage of 6 drums (205 litres) of oil. However, additional unauthorized combustibles such as plastic pipes, plastic canisters with chemicals and metal canisters with oil were observed inside the store.
- – The station has no requirements to document the maximum permissible fire load in areas significant to safety.
- – Permanent lay down area P0028 in the Fuel handling building, Unit 2 is labelled with an obsolete authorization form and contains unassessed wood, plastic, and paper items stored close to cable trays.
- – Multiple cases of plastic and paper litter and bird feathers on the floor and cable trays were observed in Unit 2 Reactor building rooms.
- – Over 50 oil leaks were observed, some on safety related equipment (for example diesel generators and gas circulator lubricating oil systems). These leaks increase fire loading.
- Without consistent, rigorous implementation of station processes for the control of combustible materials the rise of fire may increase.
Suggestion: The station should consider implementing fully, its processes for the control of combustible materials in the field to minimize fire burden and associated fire risk.
IAEA Bases:
SSR-2/2 (Rev.1):
Requirement 22: Fire safety:
The operating organization shall make arrangements for ensuring fire safety.
- 5.21. The arrangements for ensuring fire safety made by the operating organization shall cover the following: adequate management for fire safety; preventing fires from starting; detecting and extinguishing quickly any fires that do start; preventing the spread of those fires that have not been extinguished; and providing protection from fire for structures, systems and components that are necessary to shut down the plant safely. Such arrangements shall include, but are not limited to:
- (b) Control of combustible materials and ignition sources, in particular during outages.
NS-G-2.1:
6.1. Administrative procedures should be established and implemented for effective control of combustible materials throughout the plant. The written procedures should establish controls for delivery, storage, handling, transport and use of combustible solids, liquids and gases. Consideration should be given to the prevention of fire related explosions within or adjacent to areas identified as important to safety. For areas identified as important to safety, the procedures should establish controls for combustible materials associated with normal plant operations and those which may be introduced in activities related to maintenance or modifications.
6.2. Written procedures should be established and enforced to minimize the amount of transient (i.e. non-permanent) combustible materials, particularly packaging materials, in areas identified as important to safety. Such materials should be removed as soon as the activity is completed (or at regular intervals) or should be temporarily stored in approved containers or storage areas.
6.3. The total fire load due to combustible materials in each area identified as important to safety should be maintained as low as reasonably practicable, with account taken of the fire resistance rating of the compartment boundaries.
6.5. Administrative controls should be established and implemented to ensure that areas important to safety are inspected periodically in order to evaluate the general fire loading and plant housekeeping conditions, and to ensure that means of exit and access routes for manual fire fighting are not blocked. Administrative controls should also be affected to ensure that the actual fire load is kept within permissible limits.
NS-G-2.14:
4.36. Factors that should typically be noted by shift personnel include:
Deviations in fire protection, such as deterioration in fire protection systems and the status of fire doors, accumulations of materials posing fire hazards such as wood, paper or refuse and oil leakages, or industrial safety problems such as leakages of fire resistant hydraulic fluid, hazardous equipment and trip hazards.
4. Maintenance
4.2. Maintenance facilities and equipment
The plant has a well-managed Loan Tools Facility. The traceability of equipment used for an activity is ensured by recording the ID of the equipment on the work permit. This is then logged in the database, so that it is easy to trace which work has been performed with a given tool and where. This is not limited to only measurement and test equipment. Due to the capacity of the workshop, it can support not only the maintenance department but also the contractors, even during an outage. This was recognized as a good performance by the team.
4.5. Conduct of maintenance work
The team noted that in the maintenance department all staff members are encouraged to improve safety margins, work practices and reduce rework based on station Maintenance Fundamentals. This has led to the positive development of improvements made by employees. This was recognized as a good performance by the team.
4.6. Material condition
Although the station has several improvement plans in place, such as the Corrosion Management Process and the Leak Reduction Program, the team found examples where consistent high standards were not maintained. The team also noted a lack of attention to the state of lighting and the installation of cables. The team made a suggestion to continue, and in some cases accelerate, the improvement plans for material condition and correct the faulty lighting and incorrect mounted cabling.
4.7. Work control
One challenge for the station is to reduce the backlog on lower prioritized actions to improve the overall material state of the equipment. The number of P3 prioritized items is 903 and P4 prioritized items 1754 with a rising trend in 2017.
The team encouraged the station to achieve a sustained reduction in the overall defect backlog.
4.8. Spare parts and materials
Spare parts and material requests are identified early in the work management process to support their timely delivery. There is also a fleet database (POMS) to record and prioritize obsolete equipment. The station is also working on improvements regarding repairable safety related stock items. However, the team found several instances in which return to service of equipment was delayed, or direct repair was not possible due the lack of spare parts, or insufficient quality of spare parts. The team made a recommendation in this area.
4.9. Outage management
To address an issue found in previous outages, where gaps in engagement from different departments were recognized during the outage preparation, the station has developed a Pre- Outage Milestone Plan (POMP) database for Outage accountability. The results of the last outage showed a significant improvement in POMP adherence with 65 of 69 of the milestones completed on time. At the time of the mission, POMP adherence for the 2018 outage was currently 100%. This was recognized as a good performance by the team.
Detailed maintenance findings
4.6. Material condition
-
4.6(1) Issue: The material condition of equipment is not always appropriately maintained to support safe and reliable operation.
- Although the station has several improvement plans for material condition in place, the team noted the following:
- – Some cables are not well fixed to cable trays, due to missing cable ties or missing support over a greater distance than the station-specification allows:
- – Cooling Water pump 2A: several vertical cables not fixed with cable ties.
- – South East Essential Supplies building: cables to new alarm fire cabinets are not supported and fixed with cable ties (unsupported for more than 1 metre).
- – Junction Box 272992, cables not fixed with cable ties.
- – AY3 generator jacket secondary water, cable unsupported for about 3 metres.
- – Leaks and corrosion are evident on some components:
- – Common cause failures (leaks on rubber gaskets) on radiators providing cooling for all the 8 diesels have several times resulted to 1 or 2 unavailable diesel generators, when the ambient temperature is above 15º.
- – Secondary Liquid Nitrogen Vaporizer 2 is heavily corroded.
- – A Nitrogen pipe by survey point 43 is corroded.
- – The total number of oil leaks shows e degrading trend in the last 10 weeks, at the time of the mission there were 56 active leaks.
- – The overall number of leaks, including air, chemicals, gas, oil, steam and water is 221.
- – A significant amount of installed lighting is defective:
- – Room E023R01A, 5 defects
- – Room E02B02R01 6 defects
- – Turbine floor, 11 defects
- – RCA 1 Stair house, 5 defects
- – Some cables are not well fixed to cable trays, due to missing cable ties or missing support over a greater distance than the station-specification allows:
- Degraded condition of equipment, which is not identified and reported in a timely manner, could lead to equipment failure adversely affecting reliable plant operation and safety.
- Although the station has several improvement plans for material condition in place, the team noted the following:
Suggestion: The station should consider improving the material condition of equipment to support safe and reliable operation.
IAEA Bases:
SSR-2/2 (Rev.1):
Requirement 28: Material conditions and housekeeping:
The operating organization shall develop and implement programmes to maintain a high standard of material conditions, housekeeping and cleanliness in all working areas.
28. The operating organization shall develop and implement programs to maintain a high standard of material condition.
7.10 Equipment that is degraded (leaks and corrosion for example) shall be identified and reported and deficiencies shall be corrected in a timely manner.
8.1 Maintenance, testing, surveillance and inspection programmes shall be established that include predictive, preventive and corrective maintenance activities. These maintenance activities shall be conducted to maintain availability during the service life of structures, systems and components by controlling degradation and preventing failures. In the event that failures do occur, maintenance activities shall be conducted to restore the capability of failed structures, systems and components to function within acceptance criteria.
NS-G-2.14:
- 4.36. Factors that should typically be noted by shift personnel include:
- – Deterioration in material conditions of any kind, corrosion, leakage from components, accumulation of boric acid, excessive vibration, unfamiliar noise, inadequate labelling, foreign bodies and deficiencies necessitating maintenance or other action;
4.8. Spare parts and materials
-
4.8(1) Issue: Spare parts are not always available in a timely manner to support the availability of safety related equipment and systems.
- – During the mission, the team observed the following:
- – Quality of spare parts:
- – There are no preventive maintenance activities on rotating equipment spare parts in the station.
- – Spare parts for safety related equipment on stock, including Single Point Vulnerabilities (SPV), 80% are not checked if they are fit for purpose.
- – During a planned valve overhaul the new actuator taken from stock appeared to be inoperable as it was not correctly wired. Fault finding and repairing the actuator resulted in one-day delay on the fuel route outage.
- – Diesel generator BY was unavailable 2 to 3 days longer than planned, because of incorrect assembly of a spare part by the supplier.
- – Locking plates were removed from stores and found completely covered with rust.
- – Spare kits used for oxygen probe overhaul were found to have foreign material intrusion (a plastic like substance).
- – Quantity of spare parts:
- – On 20-1-2018 the AX diesel was unavailable due to problems with the starting valve. The last spare part in stock was used in April 2017. No action had been taken to get this spare part for a safety related component back in stock.
- – A pressure valve which is vital to refuelling activities is identified as a nonstock item.
- – A new diaphragm required for the overhaul of valve and actuator R2CX-WT-0617 was registered as 1 in stock but actually there was none in stock
- – A degraded vent valve on polisher cation bed 1-WC-105B could not be replaced in November 2017 due a lack of spare parts on stock. Valve replacement is planned on 10/04/2018.
- – In the third quarter of 2017, twenty condition reports were related to spare parts availability. The station recognized this as an adverse trend.
- Without the timely supply of spare parts, the availability of equipment and system may be adversely impacted.
Recommendation: The station should improve the availability of spare parts in a timely manner to support the availability of equipment and systems.
IAEA Bases:
SSR-2/2 (Rev.1):
8.17. The operating organization shall ensure that materials, spare parts and components are available and in proper condition for use.
NS-G-2.6:
8.23. The maintenance group should be responsible for ensuring that adequate spare parts and components, tools and resources for achieving its objectives are available. It should also be responsible for establishing stock levels and authorizing the issue and use of spare items and components.
GS-G-3.5:
153. Maintenance should be performed on certain items held in storage, such as large pumps and motors. Such maintenance should include periodically checking energizing heaters, periodically changing desiccants, rotating shafts on pumps and motors, and changing oil on rotating equipment and other maintenance required by the vendor.
5. Technical support
5.1. Organization and functions
The station initiated a corrosion programme for station specialists to proactively monitor, evaluate and measure corrosion processes. Corrosion cards have been provided to staff to help them identify different categories of corrosion. In parallel, the reporting of corrosion related issues has been simplified in a format that can be consistently tracked and trended. The team identified this as a good practice. The seismic assessment has been proceduralized at the station. The procedure provides instruction on how to minimize hazards in seismic events related to mobile items like trolleys and access steps, as well as scaffolds. However, the team found that some controls of potential seismic hazards were missing or not in compliance with the procedure. The team made a suggestion in this area.
5.6. Surveillance programme
The station surveillance programme was developed based on the industry process for equipment reliability. However, the team identified opportunities to act more proactively in predicting potential problems related to the reliability of the refuelling machine and safety related equipment like diesel generators. The team made a suggestion in this area.
5.7. Plant modification system
The station has a web-based modification tool where all relevant processes linked to modifications are available to the project users. This includes the supporting documentation, tools, clear requirements and interrelationships. The station personnel are expected to follow the same procedure for implementation of both permanent and temporary modifications. However, not all aspects of the control and implementation of temporary modifications are properly implemented and formalized. The team made a suggestion in this area.
Detailed technical support findings
5.1. Organization and functions
-
5.1(1) Issue: Movable items in seismic controlled areas are not systematically secured to ensure equipment safety in case of seismic events.
- The team noted the following:
- – When questioned, plant staff could not clearly explain which standards apply with regards to different classifications of seismic areas on site.
- – In the Unit 2 Reactor Pile cap, which is designated as a seismic controlled area, many items were found not secured or fixed (for example: movable carts, radiation protection devices, waste collection bins).
- – In the Unit 2 Decay heat/ventilation room, which is designated as a seismic controlled area, many items were found not secured or fixed (for example: fire extinguishers, SERT Training Rigs, wood cabinets & COSHH cupboards in the laydown area within the room).
- – In the Reactor 2 Boiler Annexe 2A room R2A05R01A, long scaffolds were not fixed to the wall as required by the seismic requirements.
- Movable items not properly secured in seismic controlled areas plant areas could pose a hazard to safe operation of plant and equipment required to support nuclear safety during the seismic event.
- The team noted the following:
Suggestion: The station should consider ensuring movable items are systematically secured in seismic controlled areas to prevent adverse effects on equipment important for safety.
IAEA Bases:
GSR Part 2, Requirement 10:
4.32. Each process or activity that could have implications for safety shall be carried out under controlled conditions, by means of following readily understood, approved and current procedures, instructions and drawings.
SSR 2/2 (Rev.1):
Requirement 8: Performance of safety related activities:
The operating organization shall ensure that safety related activities are adequately analysed and controlled to ensure that the risks associated with harmful effects of ionizing radiation are kept as low as reasonably achievable.
4.26 All activities important to safety shall be carried out in accordance with written procedures to ensure that the plant is operated within the established operational limits and conditions. Acceptable margins shall be ensured between normal operating values and the established safety system settings to avoid undesirably frequent actuation of safety systems.
SSR 2/2 (Rev. 1):
Requirement 9: Monitoring and review of safety performance:
The operating organization shall establish a system for continuous monitoring and periodic review of the safety of the plant and of the performance of the operating organization.
4.35 Monitoring of safety performance shall include the monitoring of: personnel performance; attitudes to safety; response to infringements of safety; and violations of operational limits and conditions, operating procedures, regulations and licence conditions.
The monitoring of plant conditions, activities and attitudes of personnel shall be supported by systematic walk downs of the plant by the plant managers.
NS-G-2.13:
5.33. Plant walkdowns are one of the most significant components of the seismic safety evaluation of existing installations… These walkdowns may serve many purposes, such as: evaluating in-plant vulnerabilities of SSCs, specifically issues of seismic system interaction (impact, falling, spray, flooding); identifying other in-plant hazards, such as those related to temporary equipment (scaffolding, ladders, equipment carts, etc.); and identifying the ‘easy fixes’ that are necessary to reduce some obvious vulnerabilities, including interaction effects. Walkdowns should also be used to consider outage configurations that are associated with shutdown modes.
5.6. Surveillance programme
-
5.6(1) Issue: The station’s equipment reliability programme is not always effective in preventing abnormal conditions that challenge operational safety.
- Overall plant performance has improved in a several areas in the recent years. However, the team noted opportunities to improve equipment reliability in some areas:
- Fuelling Machine Reliability:
- – The fuel route performance indicator in recent years is lower than plant target; for 2017 the indicator is 70.2 versus a year-end projection of 92.0. Refuelling machine reliability is a major contributor to the shortfall.
- – The indicator reflects that, in the last four months in 2017, there were 6 times when the plant unavailability was greater than 7 days due to fuelling machine unavailability.
- – In last four months in 2017 six temporary modifications were performed due to equipment deficiencies.
- – The plant has faced recurrent equipment failures. These recurrences have been attributed to insufficient preventive maintenance in the past, however to solve this problem, the station recently put in place a living maintenance policy.
- – In last three years more than 120 condition reports (priorities 1-3) were initiated related to fuel route.
- – In last 4 months of 2017, eight significant condition reports (priorities 1-2) were initiated related to fuelling machine.
- Diesel Generator Reliability:
- – AX Diesel Generator (DG) was unavailable more than 10 days, and the root cause has not been identified. At the time of the mission technical fault finding was underway and the root cause was not expected to be determined until completion of a test run.
- – The overall performance indicator on reliability of emergency generation (all DGs included) was red on three occasions in Q3/Q4 of 2017. This indicator covers all 8 diesel generators, and the metric can mask the real condition of the emergency generation. It can be red even if it has experienced issues with just one engine.
- – In the last three years more than 30 condition reports (priority 2 and 3) were initiated related to diesel generators.
- – In 2016/2017 there were common cause radiator leakages on AY2, BY3, BY4, CY1, CY3, DX1, DX2, DY3. On 6/09/2016 and 5/09/2017 till 13/09/2017 radiator leakages caused 2 emergency diesels to be unavailable at the same time. Issues related to radiators (rubber gaskets) started quite a long time ago. The first engineering change was performed around 2010, and after that, three additional solutions were evaluated. One further engineering change has been initiated to solve the problems with radiator leakages.
- Without a proactive equipment reliability programme, the plant may miss the opportunity to prevent abnormal conditions that challenge operational safety.
- Overall plant performance has improved in a several areas in the recent years. However, the team noted opportunities to improve equipment reliability in some areas:
Suggestion: The plant should consider enhancing its equipment reliability programme to prevent abnormal conditions that challenge operational safety
IAEA Bases:
SSR 2/2 (Rev.1):
Requirement 31: Maintenance, testing, surveillance and inspection programmes:
The operating organization shall ensure that effective programmes for maintenance, testing, surveillance and inspection are established and implemented.
8.4. Preventive maintenance should be of such a frequency and extent as to ensure that the levels of reliability and functionality of the plant’s SSCs important to safety remain in accordance with the design assumptions and intent.
- 8.5. The frequency of maintenance, testing, surveillance and inspection of individual structures, systems and components shall be determined on the basis of:
- a) The importance to safety of the structures, systems and components, with insights from probabilistic safety assessment taken into account;
- b) Their reliability in, and availability for, operation;
NS-G-2.6:
2.11. The objectives of the surveillance programme are: to maintain and improve equipment availability, to confirm compliance with operational limits and conditions, and to detect and correct any abnormal condition before it can give rise to significant consequences for safety. The abnormal conditions which are of relevance to the surveillance programme include not only deficiencies in SSCs and software performance, procedural errors and human errors, but also trends within the accepted limits, an analysis of which may indicate that the plant is deviating from the design intent.
2.12. The operating organization should establish a surveillance programme to verify that the SSCs important to safety are ready to operate at all times and are able to perform their safety functions as intended in the design. Such a surveillance programme will also help to detect trends in ageing so that a plan for mitigating the effects of ageing can be prepared and implemented.
4.7. Following any abnormal event, the operating organization is required to revalidate the safety functions and the structural and functional integrity of any SSCs that may have been challenged by the event. Necessary corrective actions are required to include maintenance, surveillance and in-service inspection, as appropriate.
5.7. Plant modification system
-
5.7(1) Issue: Temporary modifications are not systematically controlled to minimize their cumulative effect on plant operation.
- The station’s Asset Management System (AMS) contains a record of the installed Temporary Modifications (TM). At the time of the mission there were 20 installed.
- The team observed the following:
- – Temporary modifications are not ‘time-limited’ and their duration can be extended. The station’s procedure states the following: ‘A temporary modification will primarily be used for time limited modifications, which then return the plant to its original state’.
- – R2 Main boiler SRV B2BY-SS-R0007 flexible hose fitting of temporary restrain, installed in 2015, has been extended twice to date. Revision 1 states the following justification for extension: ‘EC revised to extend expiry date to 14/09/15, in line with 2015R2 outage end date’. Revision 2 states the following justification for extension: ‘EC revised to extend expiry date to 19/12/18. This is due to the deferral of bellows fitment from the 2015R2 outage to the S11R2 (2018) outage’. Inspection of the restraint assembly during the 2015R2 outage has confirmed it to be in good condition and suitable for a further three years’ service.
- – A temporary modification to remove of 3 out of 4 interlocking on Low Voltage Air Circuit Breakers (ACBs) to allow additional ACB maintenance was installed in 2014. It is still on the list of Temporary Modifications, however should have been created as a permanent modification. Topic Notes state that the shorting link will be removed when the M80 breaker is replaced under project 4A-710. This Engineering Change (EC) should be revised and closed.
- – Temporary modification on mismatch monitor was installed in 2017 and has been revised 5 times to date. Revision 5 states the following justification for extension: ‘Raised due to the inability to trace the reason for random failure of the mismatch monitor. This temporary EC will now be kept open until a replacement mismatch monitor is installed or justification has been made for permanent operation without mismatch monitor’. Permanent EC 360697 started, for mismatch monitor replacement. Justifications for previous revisions were related to different failures of the mismatch monitor.
- – Temporary modifications are not labelled at their location. This is not in accordance with local procedure on implementation of modifications which states: ‘Temporary plant modifications shall be labelled’.
- – It is not clear who controls temporary modifications and how often they are reviewed. There is no clear requirement for informing relevant staff in appropriate time of temporary modifications and of their consequences for the safe operation of the station. Recently a Configuration Control Management Team run by Operations with Design Engineering Group Head in Attendance, has been established and reviews temporary modifications monthly (5 minutes is assigned for this task).
- Without properly controlled temporary modifications, the current plant status might not be fully understood and safety may be diminished.
Suggestion: The plant should consider strengthening control of temporary modifications to ensure their cumulative effect on safe plant operation is fully understood.
IAEA Bases:
SSR 2/2 (Rev. 1):
Requirement 11: Management of modifications:
The operating organization shall establish and implement a programme to manage modifications.
4.41 Temporary modifications shall be limited in time and number to minimize the cumulative safety significance. Temporary modifications shall be clearly identified at their location and at any relevant control position. The operating organization shall establish a formal system for informing relevant personnel in good time of temporary modifications and of their consequences for the operation and safety of the plant.
NS-G-2.3:
6.3. The number of temporary modifications should be kept to a minimum. A time limit should be specified for their removal or conversion into permanent modifications.
NS-G-2.3:
6.5. The plant management should periodically review outstanding temporary modifications to consider whether they are still needed, and to check that operating procedures, instructions and drawings and operator aids conform to the approved configuration. The status of temporary modifications should be periodically reported (typically at monthly intervals) to the plant manager. Those that are found to be needed permanently should be converted in a timely manner according to the established procedure.
NS-G-2.4:
6.72. The operating organization should establish a procedure to ensure the proper design, review, control and implementation of all permanent and temporary modifications. This procedure should ensure that the plant’s design basis is maintained, limits and conditions are observed, and applicable codes and standards are met. A record of the review shall be made available to the regulatory body. The operating organization maintains responsibility for safety implications of the modification and for obtaining the appropriate review and approval by the regulatory body if required.
6.73. Requests for modification should be evaluated on the basis of their impact on plant safety and reliability, plant operation and performance, personnel safety and the fulfilment of regulatory requirements. Considerations should include the need for training upgrades and associated hardware.
NS-G-2.14:
5.40. Tagging should be used to designate clearly that the modification in the field is approved for use. A tagging programme should be maintained by operations personnel. Each approved modification should be assigned a unique number.
5.41. Control room operators should maintain a listing of the temporary modifications that have been made. The listing should identify each modification by its number and should include copies of the description of the modification made and of its reviews and approvals.
5.42. Operations personnel should review periodically all temporary modifications for their continued applicability and proper implementation.
5.1(a) Good Practice: Corrosion Cards
- Corrosion is a growing concern in the station that can lead to significant nuclear, industrial or environmental safety events and/or a loss of generation. As part of a fleet wide Corrosion Programme, station needs to be able to appropriately act to highlight risks in a format that allows for tracking and trending. To achieve this:
- – Personnel are being provided with corrosion cards to be able to categorise Cases of Corrosion, to assign Corrosion Priorities and to know the further actions associated with each Priority.
- – The station developed a way for personnel to be able to easily report corrosion related condition reports & working requests in a format that will enable tracking & trending.
- Benefits include:
- – Risk mitigation for corrosion vulnerable plant has been assessed (and assigned a grade: CV1 to CV4), and action plans undertaken to improve the plant.
- – Staff awareness is heightened by distribution of corrosion identification cards with pictorial guidance.
- – The ‘Work Request’ panel has been amended so that analysis and recording the ‘asfound’ condition can be investigated promptly.
- – Essential plant areas such as Auxiliary Boiler Exhaust Stack, Diesel Generator Exhaust Stack, CO2 Storage Plant and Nitrogen Storage plant have been improved greatly.
- – Plant investment strategy can be influenced on a risk based approach to improve value and efficiency.
- – Toolbox talk 160 was distributed to raise awareness throughout the plant.
6. Operating experience feedback
6.2. Reporting of operating experience
The station provides recognition and visibility to staff identifying and reporting particularly good findings. To achieve this, condition reports (CRs) of interest are selected at the screening meeting and the most valuable ones are awarded CR of the day, of the week or of the month. This has allowed an increased quality of event reporting and the team recognised it as a good performance.
6.4. Screening of operating experience information
The prioritisation and categorisation process is not based on the explicit safety significance of the event but rather on the degree of acceptance by the station of the event to reoccur. The team found several CRs for which the priority level or the depth of investigation was not commensurate with the actual or potential safety significance. The team recommended that the plant enhance the screening and categorization process to ensure that events are investigated in accordance with their actual or potential significance.
6.5. Investigation and analysis
Event investigations are not concluded in a timely manner. Root cause analyses are often initiated too late and concluded after their initial due date, on average after 65 days. Apparent cause analyses are concluded on average after 55 days and equipment failures on average after 76 days. The team encouraged the station to complete event investigation in a timely manner, without jeopardizing the necessary quality level.
6.6. Corrective actions
The station has progressively improved the quality of its corrective action programme. However, the team noted an elevated proportion of recurring events and events that had a significant amount of past operating experience (OE) that could have helped to prevent or minimize consequences of the event. Deficiencies in the use of past OE are rarely addressed by corrective actions (CAs). Repeat or recurring events are not always used to better define the CAs and CAs are often rescheduled. Among other things, the team found several root cause analyses (RCAs) without CA to prevent recurrence, and that some CAs are not specific, targeted or measurable; while some CAs are incorrectly, partially or not at all implemented. Some CAs contain no effectiveness review, some do not have the extent of condition or extent of cause adequately assessed; and others with adequate assessment but without appropriate corrective actions. The team suggested the plant consider ensuring that corrective actions are adequately defined and implemented in a timely manner to prevent recurrence.
6.7. Utilization and dissemination of operating experience
The station has an organisational learning portal in place where external operating experience (OE) is easily accessible. A tool has been developed that allows all staff to customize automatic newsletters with recent events, based on coding. This facilitates the communication and use of external OE by all staff and the team recognised this as a good performance.
6.9. Effectiveness review of the operating experience programme
As already mentioned, the station has experienced an elevated proportion of repeat significant events, recurring issues, or events for which a significant amount of past OE could have helped to prevent or minimize the event. However, the station does not collectively assess this information to find opportunities to improve the OE process and derive overarching corrective actions. The team also found several gaps in the self-assessment of the effectiveness of some of the plant safety-related programmes and in some key performance indicators. The team made a broader recommendation about this in the leadership and management area.
Detailed operating experience feedback findings
6.4. Screening of operating experience information
-
6.4(1) Issue: The station processes for event screening and categorization do not always ensure that events are assigned the appropriate priority and investigated in accordance with their actual or potential significance.
- The team found the following:
- – The screening and prioritisation process is not based on explicit safety significance of the event. It is rather based on the degree of acceptance by the station for the event to reoccur. Priority 1 events (high priority, leading to mandatory root cause analysis) are defined as events that the Station does not accept to reoccur at all. Priority 4 events are events which the station accepts to reoccur. Priority 2 and 3 events are events which the Station accepts to reoccur but less often. The prioritisation procedure also provides a list of illustrative examples clarifying the type of events within each category.
- – The recent/ongoing issues leading to inoperability of the BY and later the CX emergency diesels have all been investigated under the initial BY diesel related condition report with priority 2, using only an apparent cause evaluation. Despite the repetition of these issues, the priority and the level of investigation have not been increased.
- – The condition report (CR) related to marine ingress involving unplanned plant manoeuvring was categorized priority 1; however, no root cause analysis was performed, only a self-assessment of a procedure. There is no evidence of an assessment of the actual or potential consequences on safety. The duration of entry into Tech Spec Required Actions is not indicated in the report. This has not been flagged as a ‘repeat event’ by the station even though it should have been according to procedure. At least one reactor trip caused by marine ingress occurred after this CR was raised.
- – A potential challenge to the reactor safety case led to a complex and long investigation. Despite its significant potential impact on safety, this event was categorized as priority 2 and investigated by a panel of technical experts, without any root cause analysis (RCA). They focused on finding the most probable cause, rather than on finding the root cause. Deviations with high potential safety consequences (‘route 4’) are handled by multidisciplinary teams of highly skilled experts, but not using RCA methods.
- – In April 2017 a fuel assembly was assembled in the wrong order. The corresponding CR was categorized as priority 3 only, and only the actual consequences on nuclear safety were assessed, not the potential safety consequences.
- – The CR related to tripping of a control computer automatically controlling feedwater to the main boilers was categorized as priority 4 at the screening meeting on 26/01/2018. The trip has an indirect effect on safety and could have led indirectly to a reactor trip. According to procedure, only events that can be accepted to recur without a frequency limit should be categorized with priority 4 or lower. Two further failures of a control computer occurred just 3 days later (29/01/2018).
- – The CR involving electric shock risk with an actuator remaining live after its supply fuse had been removed was categorized as priority 2 by the station. Only a minor apparent cause analysis was requested by the screening committee. However, the CR was closed without performing any minor apparent cause analysis.
- – During the screening of OE, a lower level or no investigation may be applied where the cause of the event is, or is thought to be, known. The station performed no investigation in about 20% of the priority 2 events over the last 3 years. For priority 3 events the figure was about 48% over the last 3 years.
- – The priority 1 CR involving reactor trip repeated 3 times was not analysed using an RCA because the RCA following the second occurrence was issued only 2 months before.
- Without ensuring that events are assigned the appropriate priority and investigated in accordance with their actual or potential significance, some avoidable events could occur and some learning opportunities could be missed.
- The team found the following:
Recommendation: The station should enhance its event screening and categorization process to ensure that events are assigned the appropriate priority and are investigated in accordance with their actual or potential significance.
IAEA Bases:
SSR-2/2 (Rev.1):
5.28. Events with safety implications shall be investigated in accordance with their actual or potential significance. Events with significant implications for safety shall be investigated to identify their direct and root causes, including causes relating to equipment design, operation and maintenance, or to human and organizational factors.
NS-G-2.11:
3.1. Screening of event information is undertaken to ensure that all significant matters relevant to safety are considered and that all applicable lessons learned are taken into account. The screening process should be used to select events for detailed investigation and analysis. This should include prioritization according to safety significance and the identification of adverse trends.
4.3. The level of the investigation carried out should be commensurate with the consequences of an event and the frequency of recurring events. Significant factors that would influence the magnitude of an investigation may include the following: whether a similar occurrence has taken place earlier.
6.6. Corrective actions
-
6.6(1) Issue: Corrective actions are not always adequately defined and implemented in a timely manner to prevent event recurrence.
- The station is progressively improving the quality of its corrective action programme (CAP). However, the team found the following:
- – Of the 10 root cause analyses (RCA) performed in the last 3 years and reviewed by the team, 4 are repeat events and 4 others had significant amounts of past OE that could have helped to prevent or minimize the consequences of the events.
- – On 13/05/2012, Unit 2 tripped during a test following loss of 11kV power due to Grid Disturbance Protection. On 21/11/2014, Unit 2 tripped again during the same test, due to failure of the same relay. The corrective action (CA) after the first trip was closed in the system and was only partially implemented. The root cause identified for this repeat event is that corrective actions were not implemented in a timely manner. The corrective actions had not been sufficiently challenged to ensure actions have been fully completed and that actions taken will prevent repeat events. On 26/03/2015, the same test led to the failure of the same type of relay. On this occasion a reactor trip was avoided because the test was performed at a lower reactor power. The cause of this third occurrence is a lack of timely implementation of the corrective actions from the previous failure (replacement of the relays).
- – On 14/12/2015 a reactor trip occurred following a quadrant trip. This was identified as a repeat event with 3 previous occurrences. The previous investigations had mainly tried to identify the direct cause, or root cause of the direct fault, but not the underlying issues. The terms of reference of all previous RCAs have been heavily weighted towards the direct cause and immediate actions. As a result the station has experienced several repeat events of quadrant trips leading to reactor trips which may have been avoided.
- – On 22/11/16, marine ingress led to a reactor trip. This was identified as a multiple repeat event for which corrective actions from previous investigations have not been implemented. The root cause is that the organisation had not fully prioritised and implemented the necessary measures to protect the station the plant from all adverse sea conditions. A significant proportion of the proposed actions in all previous investigations were not completed and/or were closed ‘to a promise’. Several key actions were not effective. For example, the reactor service water auto vents were found to be incorrectly installed. In summary, the issues experienced by the station have happened before. At the time of the mission the station had yet to implement adequate prevention measures, many of which have been recommended on several occasions. This had been based on choice primarily driven by financial considerations, and therefore it was a conscious decision to not implement recommendations based on previous OE. The team also noted deficiencies in the corrective actions following the 22/11/16 trip.
- – Deficiencies in the use of past OE when identified in RCAs are almost never addressed by CAs. Repeat or recurring events are not always used to better define the CAs.
- – Only priority 1 events (significant events, numbering about 10 over the last 3 years) are checked whether they are repeat events or not. As there are very few priority 1 events each year, this is a very narrow definition. The CAP coordinator and the screening meeting members also identify ‘recurring events’. These are considered repeat events that do not meet the strict definition (for instance CRs with a priority lower than 1). The Station flagged 830 CRs as being ‘recurring events’ in 2017.
- – Corrective actions (CAs) in RCAs often lack several expected attributes, in particular:
- – Several RCAs have no CAPR (Corrective Action to Prevent Recurrence) as allowed by station procedure, others with a CAPR addressed only part of the root cause.
- – Some CAs are not specific, targeted, or measurable.
- – Some CAs have been incorrectly, partially, or not implemented.
- – Some CAs have had no effectiveness review performed, and in some cases the effectiveness review was performed using too generic criteria.
- – Some RCAs did not adequately assess the extent of cause and in some other cases the assessment was adequate but was not addressed by any corrective action.
- – One case occurred where the root cause was not addressed by CAs.
- – Some cases where the extent of condition was not adequately assessed and other cases where the assessment was adequate but was not addressed by any action.
- – A few CAs in the tracking system do not fully match the CAs in the RCA report.
- – Corrective actions associated with RCAs are often rescheduled.
- – A review of a sample of 6 apparent cause analyses by the team highlighted some lack of quality of corrective actions and a significant proportion of recurring events.
- – Over the last 3 years, half of the CAs to prevent recurrence (CAPRs) had their due date extended. 3 out of 8 have had 2 extensions, 1 CAPR was extended 3 times.
- – There are currently 388 open corrective actions tracked in the CAP. Their average age is 214 days. The average age of open corrective actions for P1 (priority 1, highest priority) events is 556 days, 419 days for P2 events, 219 days for P3 events, and 166 days for P4 events.
- – Of the 10 root cause analyses (RCA) performed in the last 3 years and reviewed by the team, 4 are repeat events and 4 others had significant amounts of past OE that could have helped to prevent or minimize the consequences of the events.
- Without adequately defined and timely implemented corrective actions, events can reoccur.
- The station is progressively improving the quality of its corrective action programme (CAP). However, the team found the following:
Suggestion: The station should consider ensuring that corrective actions are adequately defined and implemented in a timely manner to prevent recurrence of events.
IAEA Bases:
SSR-2/2 (Rev.1):
5.30. As a result of the investigation of events, clear recommendations shall be developed for the responsible managers, who shall take appropriate corrective actions in due time to avoid any recurrence of the events. Corrective actions shall be prioritized, scheduled and effectively implemented and shall be reviewed for their effectiveness.
NS-G-2.11:
5.2. The development of recommended corrective actions following an event investigation should be directed towards the root causes and the contributory causes, and should be aimed at strengthening the weakened or breached barriers that failed to prevent the event. Personnel at nuclear installations are responsible for implementing corrective actions promptly and effectively.
- IV.3. Factors that should be considered in the formulation of corrective actions include the following:
- – Whether the proposed corrective action addresses the fundamental problem;
- – Whether the corrective action has been taken before and with what results;
- IV.4. The plan for corrective action should include a provision for verification of the effectiveness of the actions.
7. Radiation protection
7.3. Radiation work control
Since late 2017, there has been an adverse trend regarding the number of personal contamination events. The team encouraged the station to keep focusing on analyzing the causes and contributors to these events as well as developing and implementing corrective measures.
The operating status of the Radiation Controlled Area exit monitors can be remotely viewed and interrogated from any network personal computer in the station. The instances where events are not reported have been eliminated by use of the remote viewing system. The team considered this a good practice.
7.4. Control of occupational exposure
The monthly dose constraint for Category A workers is not sufficiently challenging. The constraint should give more emphasis to the optimization of radiation exposure to keep doses as low as reasonably achievable (ALARA). The team encouraged the station to review the monthly dose constraint for Category A workers.
7.5. Radiation protection instrumentation, protective clothing and facilities
The station has taken an initiative to develop a program of fleet-wide inter-calibration and comparison measurements in radiochemistry. This approach has improved control of the status of radiation protection instrumentation. This was recognized by the team as good performance.
7.6. Radioactive waste management and discharges
Since 2009, the station has cleared a large amount of legacy waste and refurbished the active solid waste building. Measures have been taken to raise awareness of the importance of good radioactive waste practices. The amount of metal waste cleared as non-radioactive has nearly doubled. Also, the amount of waste bags requiring additional hand-sorting has been greatly reduced. In 2016 the station’s radiological waste fleet indicator result was 100%, a fleet first. The team considered this a good performance.
7.8. Use of PSA, PSR and OEF
At present, large amounts of Radiation Protection (RP) data (such as extensive results from surveys) are stored in different databases and systems. There is no easy, effective way of searching for results, trending or drawing conclusions. The team encouraged the station to improve data display and trending of RP related information.
Detailed radiation protection findings
7.3(a) Good Practice: Remote viewing of Radiation Controlled Area contamination monitors.
The operating status of the Radiation Controlled Area exit monitors can be remotely viewed and interrogated from any networked personal computer (PC) in the station. This enable verification that all alarms are investigated and reported as well as early reporting of defects. The system software enables the user to trend results for individuals working in the Radiation Controlled Area.
The previous version of the Radiation Controlled Area exit monitors could not be remotely interrogated in this way, which led to some events (approximately 2 events per calendar month) going unreported. This has now been eliminated.
- The station has also identified other benefits of using networked Radiation Controlled Area monitors, such as:
- – The ability to remotely view individual monitor operating performance improves ease of fault finding and early reporting of instrument faults.
- – The ability to trend sub-alarm, low level build-up of chronic contamination on worker clothing. This enables early intervention by Radiation Protection personnel to reduce the number of unnecessary alarms by suggesting laundering the personal protective equipment (PPE).
8. Chemistry
8.2. Chemistry surveillance and control programme
To reduce carbon deposition inventory on boiler and fuel cladding that can lead to fuel failures and boiler tube fouling, carbonyl sulphide (COS) is injected into the primary coolant. The injection systems have been operating continuously for seven years preventing or slowing carbon deposition formation. Since the addition of COS in 2011, the station has seen progressive improvement in the boiler heat transfer impairment (HTi) and an improvement in fuel failures, with no fuel failures in the last four years. The team recognized this as a good performance.
The chemistry control of plant systems is in general well controlled within the normal action level limits. However, equipment supporting the control of chemistry conditions is not always maintained available to prevent the potential of adverse system component corrosion or fouling. Chemistry related equipment deficiencies for a few systems such as the raw cooling water chlorination and turbine generator hydrogen dryer requires frequent chemistry and maintenance interactions to return the systems to desired chemistry conditions. The team noted that the reliability of chemistry related equipment is degraded, affecting the chemistry function’s ability to maintaining system chemistry specifications and minimize the potential of adverse system component corrosion and fouling. The team made a suggestion in this area.
Corrective actions to avoid reaching chemistry action levels are not always proactively initiated to ensure chemistry parameters stay within the specified target range. Stator cooling water pH, boiler feedwater hydrazine to oxygen ratio, and emergency diesel antifreeze pH frequently challenge or exceed the corporate established target bands. In the case of the emergency diesel antifreeze pH issue, the station has received corporate dispensation to control at a lower pH value with acknowledgement that the low pH could increase component corrosion rates. Without proactively controlling system chemistry within the specified target range system component degradation may increase. The team made a suggestion in this area.
Most system chemistry diagnostic parameters are not routinely monitored to establish a normal baseline and aid recognition of developing abnormal conditions. For example, the makeup water treatment plant product is monitored for conductivity but the diagnostic parameters of chloride, sulphate, and sodium are not routinely monitored. The team encouraged the station to periodically monitor the diagnostic chemistry parameters specified in the corporate guidance.
When the decay heat boiler (DHB) is placed in service the water chemistry is typically outside specifications for chlorides, sulphates, and oxygen. The DHB system and storage tank vents are open to the atmosphere which allows rain ingress containing chlorides and sulphates. The DHB circulating water requires monthly flushing to lower the chlorides and sulphate contaminants and replenish the hydrazine that has been consumed. The team encouraged the station to enhance the DHB system preservation and operational practices to provide adequate protection from corrosion.
Data collected from various instrument computers, including on-line chemistry instrumentation, is interrogated and trended using the Pi Historian and Babel fish tools. Multiple parameters can be trended together to provide insights into causes of adverse chemistry trends, necessary purging/flushing time requirements, and time to achieve target levels. These on-line monitoring tools have enabled a reduction in outage time and improved optimization of demineralizer and desiccant performance. The system also provides alerts via email for adverse developing chemistry trends and other on-line monitor performance such as reduced flow. The team recognised this as a good performance.
Detailed chemistry findings
8.2. Chemistry surveillance and control programme
-
8.2(1) Issue: Equipment supporting the control of chemistry conditions is not always maintained available to prevent the potential of adverse system component corrosion or fouling.
- During the mission, the team observed the following:
- – Circulating water hypochlorite dosing system failures have resulted in over 50% insufficient treatment time in the last four months and failures have been reported every month since January 2017.
- – Since 2016, reactor gas dryer multi-port valve operational problems have contributed to several core life loss events in both units, even though core life loss has been reduced in 2017.
- – Turbine generator hydrogen dryer equipment problems have resulted in the dryer being out of service since June 2017.This has adversely affected hydrogen purity control and required intermittent purging to maintain chemistry within action limits. Without reliable equipment that supports control of system chemistry conditions, longterm system and component reliability may be adversely affected.
- During the mission, the team observed the following:
Suggestion: The station should consider improving the reliability of equipment that supports the control of system chemistry specifications, to prevent adverse system and component corrosion or fouling.
IAEA Bases:
SSR-2/2 (Rev. 1):
7.14 Chemistry surveillance shall be conducted at the plant to verify the effectiveness of chemistry control in plant systems and to verify that structures, systems and components important to safety are operated within the specified chemical limit values.
SSG-13:
- 3.4. In the chemistry programme, it should be ensured that:
- – 3.4(g) There is a timely response to correct any deviations from normal operational status, such as small deficiencies, adverse trends or fast transients of chemistry parameters.
- – 3.4(e) Appropriate chemistry controls and diagnosis parameters are applied to verify safe and reliable operation.
- – 3.4(k) There is support to the station ageing management programme in order to ensure safe and long term operation of the station.
- – 5.5. The chemistry control programme should support the production of high quality water and should include the following:
- – The specification and application of a suitable chemical treatment (e.g. oxygen control) for the minimization of corrosion processes, and hence reduction of the amounts of corrosion products in the water.
- – The specification and application of a suitable chemical treatment (e.g. oxygen control) for the minimization of corrosion processes, and hence reduction of the amounts of corrosion products in the water.
-
8.2(2) Issue: Proactive actions to avoid reaching action levels are not always initiated to ensure chemistry parameters stay within their specified target range.
- During the mission, the team observed the following:
- – Stator cooling water pH is frequently below the target value of 8.5 and periodically near action level 1 for several weeks without prompt chemistry correction. This may be a contributor to turbine generator 2 copper being above the upper target value of 5.0 ppb for four of the last nine months.
- – Unit 2 boiler feedwater hydrazine is frequently below the hydrazine to oxygen ratio target range of 2.0. This is a reduction of margin to ensure that boiler water is depleted of oxygen by the time it reaches the stainless (316) steel section since there is no way to measure oxygen in this location.
- – Emergency diesel antifreeze pH is frequently below the target and action level range. Even though corporate chemistry has approved temporary dispensation to allow pH values as low as 7.5, it was acknowledged that the low pH could increase component corrosion rates.
- Without proactively controlling system chemistry within the specified target range, system component degradation may increase.
- During the mission, the team observed the following:
Suggestion: The station should consider taking more proactive actions to ensure chemistry parameters stay within their specified target range.
IAEA Bases:
SSG-13:
- 3.4. In the chemistry programme, it should be ensured that:
- (d) The chemistry programme for auxiliary systems is in accordance with the material intent to preserve their full integrity and availability.4.4. If a control parameter is outside its limit values, degradation of conditions for structures, systems and components may occur in the long term and may result in unavailability of safety systems.
- 6.2. The objectives of a chemistry surveillance programme are:
- (c) To detect and thus permit early corrective action for any abnormal chemistry condition before it becomes a consequence significant for safety
9. Emergency preparedness and response
9.1. Organization and functions
EDF Energy has a Central Emergency Support Centre (CESC) located at its central offices in Barnwood, Gloucester. This facility is maintained in a state of readiness with on-call staff able to provide technical and logistical support to the station. The facility allows the station to concentrate on its actions within the site boundary and pass all other tasks to the CESC to manage.
The off-site emergency centre (Strategic Co-ordination Centre, SCC) is located in Macmerry, about twenty miles from the station. The prime function of the SCC is to decide on the actions to be taken off-site to protect the public, to ensure that those actions are implemented effectively, and to ensure that information and advice is passed to the public. The SCC is well equipped and provides good co-operation with the station.
During genuine event exercises and demonstrations; the emergency services (police, fire, and ambulance) send liaison officers to the Emergency Control Centre at the station to support the onsite organisation. This ensures the emergency services are fully aware of and can align to the onsite priorities, as well as provide up-to-date information on casualty treatment, fire and rescue support, and police liaison.
In an ‘off-site nuclear emergency’, the station sends two vehicles off-site to take various contamination and radiation readings. Contamination samples are taken into a Maypack sampler module that previously had to be stored within the vehicle and then returned to a laboratory for analysis. The station has now installed mobile gamma spectrometry devices within these off-site vehicles. This enables the operator to analyse the samples at the point of measurement and immediately send the result back to facilitate appropriate countermeasure advice. This saves time and allows processing of the data and timelier direction of the survey vehicles to the next appropriate location.
The team considers all these arrangements for the off-site support as a good performance.
9.2. Emergency response
The station utilizes Beta Hood protective equipment that is an improvement over the normal flash hood and provides enhanced protection to the responders. The benefit is that any possibly contaminated water runs down and off the responders, rather than inside the protective clothing and putting them at risk. The team recognized the use of Beta Hoods as a good practice.
The station has created an on-site fire training facility that consists of a main heat and smoke area, a hot box fire rig, and welfare buildings. The allocated space, a fenced-off area just outside the main security fence, has scope for further future enhancements. The facility is fabricated from six shipping containers joined together to form three levels. Lesson plans have been developed in line with the generic training model and the facility is now routinely used as part of the Emergency Preparedness and Response training program. In return for utilisation of the facility, Scottish Fire & Rescue service provides instructors for staff training days. The main benefit of the facility is that it ensures a realistic training environment specific to the site. The team noted this as a good performance.
9.3 Emergency preparedness
Habitability of on-site emergency facilities under radiological conditions that could be encountered during the emergency response has not been ensured against radiological conditions by hermetic sealing and air intake filtration. The station follows the company practice to rely on use of alternative emergency facilities to mitigate loss of habitability of the main emergency facilities. The evacuation of on-site personnel has not been subject to real time exercise at the station. The exercises have been only conducted as table tops during Level 2 demonstration exercises. Benchmarking the applied practices and their effectiveness in relation to nuclear industry practices elsewhere could be beneficial for assuring good safety practices and standards. The team made a suggestion in this area.
Detailed emergency preparedness and response findings
9.2. Emergency response
9.2(a) Good Practice: Beta Hood – Protection of emergency responders from skin contact with radioactive water.
During an emergency event, responders could be exposed to contamination water runoff. In a normal fire kit of flash hood and tunic, this water can run down into the clothing and meet the skin of the responders. Any beta contamination within the water will then irradiate the skin and cause harm to the responder. To address this station now provides Beta Hoods that improve on the normal flash hood and provide enhanced protection to the responders. They add a covering to the shoulders of the responders that is incorporated into the hooded protection for the face. The benefit is that any possibly contaminated water runs down and off the responders, rather than inside the protective clothing.

9.3. Emergency preparedness
-
9.3(1) Issue: The station has not extensively benchmarked its applied approach to emergency facilities’ habitability and on-site personnel evacuation to ensure that they provide optimal safety benefits.
- The team noted the following:
- – Inhabitability of emergency facilities including the Central Control Room (CCR), Emergency Control Centre (ECC) and Access Control Point (ACP): under credible radiological conditions that could be encountered in an emergency, these facilities are not protected against radiological conditions by sealing and intake filtering.
- – EDF Energy practice, followed by the station, is to rely on use of alternative emergency facilities to mitigate loss of habitability of the main emergency facilities.
- – The evacuation of on-site personnel has not been subject to real time exercise at the station. The exercises have only been conducted as table tops during Level 2 demonstration exercises.
- – The evacuation of on-site personnel takes place with significant support from the Central Emergency Support Centre (CESC) at Barnwood and is assisted by the local police (in relation to both traffic arrangements and bus service arrangements).
- – Real evidence and learning have been obtained (for example in a recent Heysham 2 Site Incident), where non-essential staff were gradually released without incident.
- Without comparing the chosen practices to those applied elsewhere in the nuclear industry, the station cannot be assured these approaches represent best practice.
- The team noted the following:
Suggestion: The station should consider benchmarking its applied approach to emergency facilities’ habitability and on-site personnel evacuation and consider effectiveness of these arrangements in relation to nuclear industry practices elsewhere.
IAEA Basis:
GSR Part 7:
Requirement 24: Logistical support and facilities for emergency response:
The government shall ensure that adequate logistical support and facilities are provided to enable emergency response functions to be performed effectively in a nuclear or radiological emergency.
6.22. Adequate tools, instruments, supplies, equipment, communication systems, facilities and documentation (such as documentation of procedures, checklists, manuals, telephone numbers and email addresses) shall be provided for performing the functions specified in Section 5. These items and facilities shall be selected or designed to be operational under the conditions (such as radiological conditions, working conditions and environmental conditions) that could be encountered in the emergency response, and to be compatible with other procedures and equipment for the response (e.g. compatible with the communication frequencies used by other response organizations), as appropriate. These support items shall be located or provided in a manner that allows their effective use under the emergency conditions postulated.
6.25. These emergency response facilities shall operate as an integrated system in support of the emergency response, without conflicting with one another’s functions, and shall provide reasonable assurance of being operable and habitable under a range of postulated hazardous conditions, including conditions not considered in the design.
GSR Part 7:
Requirement 25: Training, drills and exercises for emergency preparedness and response:
The government shall ensure that personnel relevant for emergency response shall take part in regular training, drills and exercises to ensure that they are able to perform their assigned response functions effectively in a nuclear or radiological emergency.
6.30. Exercise programmes shall be developed and implemented to ensure that all specified functions required to be performed for emergency response, all organizational interfaces for facilities in category I, II or III, and the national level programmes for category IV or V are tested at suitable intervals. These programmes shall include the participation in some exercises of, as appropriate and feasible, all the organizations concerned, people who are potentially affected, and representatives of news media. …
GS-G-2.1:
- Table 15 (in Characteristics of Emergency operations facility):
- – Access to the information required to coordinate on-site and off-site response decisions;
- – Reliable communications with on-site and off-site response centres and organizations;
- – Continuous monitoring of radiation levels; security to prevent unauthorized access.
- If located within the UPZ, it should be provided with sufficient protection to remain habitable*a during an emergency or provided with a backup. Activation time: within 1 hour of declaration of a site area or general emergency.
*a This should include provisions to monitor and control radiological exposures and contamination, to control other hazards (e.g. heat, air quality) and to meet human needs (e.g. with food, water and sanitary and sleeping arrangements) if the facility may be isolated for an extended period during an emergency.
10. Accident management
10.1. Organization and functions
Emergency personnel are required to have a comprehensive understanding of the strategy for Severe Accident Managements (SAM) for decision making when responding to severe accidents. They also need to be highly familiar with the use of equipment for mitigatory actions, depending on each assigned role. However, the team identified the training program regarding SAM does not always provide sufficient refresher training. The refresher training for Deployable Back Up Equipment (DBUE) on site is only performed as a station walk down without demonstrating the actions to install and operate the equipment, and the refresher training for Severe Accident Guidelines (SAGs) is not routinely performed. The team made a suggestion in this area.
10.4. Development of procedures and guidelines
The station has Symptom Based Emergency Response Guidelines (SBERGs) and Severe Accident Guidelines (SAGs) that provide SAM guidance. The SBERGs have already been extended to cover all station states (including unit outage condition - SBERG 7) and fuel route accidents (SBERG A–D), (development of SAGs for fuel route accidents are still in progress). The team encouraged the station to ensure the timely integration of SAGS for fuel route accidents as planned.
The station has proactively made efforts to improve the user-friendliness of emergency procedures. SBERGs and the Emergency Response Procedures for connecting the Deployable Back Up Equipment have been designed with colour pictures and flow charts. These take into account Human Factors assessments based on the operators’ request, and in a format that aids the operators to perform their role in a highly stressful environment during a severe accident condition. The team recognized this as good performance.
10.5. Plant emergency arrangements with respect to SAM
The station has a number of deployable back-up equipment for responding to severe accidents such as a high-pressure water pump, diesel generators, unimogs etc. They are housed off-site in the Strategic Storage Facility and can be transported to the Staging Post (a pre-designated location adjacent to the plant) in the event of an ‘Off-site nuclear emergency’. The equipment includes the Mobile Command and Control Centre (‘Pod City’) which consists of containerised modules for various functions. It provides a flexible, mobile facility for use if all other on-site facilities and alternative facilities are uninhabitable. The team recognized this as a good performance.
Detailed accident management findings
10.1 Organization and functions
-
10.1(1) Issue: The training program for Severe Accident Management (SAM) does not always provide sufficient refresher training to ensure continued capability of response to severe accident conditions.
- The station is implementing a project to provide many types of equipment for severe accident both on site and off site. However, during the mission the team observed the following:
- – Training for Deployable Back Up Equipment (DBUE) is performed annually for all Standby Emergency Response Team (SERT) members. Initial training is conducted off-site, at Bellshill near Glasgow, and confirms SERT members’ ability to lay out, connect hoses and cables, and operate equipment. However, refresher training is only performed on site as a plant walk down, as the DBUE is only located at Bellshill.
- – DBUE has never been deployed at Torness site, but exercised at a sister site (Heysham 2) in 2014. An exercise which includes deployment of DBUE at Torness is scheduled for a level 1 exercise in 2019.
- – Training on Severe Accident Guidelines (SAGs) is provided only in the form of table top training for a new person. For the last major revision in December 2013, dedicated update training was provided for all operators and staff who have a technical role in the emergency plan, but refresher training is not routinely performed.
- – Emergency exercises are typically performed on scenarios that do not use SAGs. This is because operator actions cannot be practiced at the site and the station perception of the low probability of occurrence.
- Without sufficient refresher training, emergency staff may not be able to perform the duties assigned to them when responding to severe accident conditions.
- The station is implementing a project to provide many types of equipment for severe accident both on site and off site. However, during the mission the team observed the following:
Suggestion: The station should consider enhancing the training programme regarding SAM to provide sufficient refresher training to ensure continued adequate response to severe accident conditions.
IAEA Bases:
SSR-2/2 (Rev.1):
Requirement 19: Accident management programme:
The operating organization shall establish, and shall periodically review and as necessary revise, an accident management programme.
5.8E. The accident management programme shall include training necessary for implementation of the programme.
NS-G-2.8:
- 4.33. They should also receive specialized training relevant to the duties they will have to perform in an emergency. The purpose of this training should be:
- – to verify that all individuals participating in the exercise are familiar with, and capable of performing, the emergency duties assigned to them;
- – to verify that emergency response and all related duties can be carried out in a timely manner according to the planned schedule and in stressful situations.
NS-G-2.15:
3.104. The training should be commensurate with the tasks and responsibilities of the functions; hence, in-depth training should be provided for the key functions in the severe accident management programme, that is, the technical support centre evaluators, decision makers and implementers.
3.108. Initial training as well as refresher training should be developed. Refresher training should take place at regular intervals that are compatible with the plant’s overall training programme. A maximum interval for refresher training should be defined; depending on the outcome of exercises and drills held at the plant, a shorter interval may be selected.
11. Human-Technology-Organization interaction
11.3 Continuous improvement/learning organization (monitoring and assessment)
The station has organized a leadership club that support leaders by refreshing their knowledge and skills on a variety of subjects. The leadership club provides training for all leaders on behavioural, leadership and process management topics. Workshops are leader-led and designed to fully engage leaders and encourage them to share their operational experience. Problems arising in the field are the focus. Topics have included: absence management, difficult conversations, outage, unconscious bias, navigating inclusion, security for leaders, mediation, effective communications, and development of people. The club workshops are typically conducted during an outage. The team recognized this as a good performance.
The team identified that knowledge management (KM) is not systematically implemented at the station to ensure effective knowledge acquisition, transformation, transfer and retention. The station strategy and associated key performance indicators for KM have not been developed. The station has not trained and qualified personnel in KM. The procedure linked to KM does not include requirements for KM attributes such as knowledge gaps, critical knowledge identification, and knowledge mapping. Knowledge preservation is more focused on ‘tacit-to-tacit’ then ‘tacit-to-explicit’ knowledge transfer. The team made a suggestion in this area.
11.4. Safety culture
The team identified that the nuclear safety culture (NSC) self and independent assessments are not sufficiently conducted at the station to continuously improve nuclear safety culture. Procedures to conduct NSC assessment have not been developed. Not all NSC assessment tools have been used to gather initial data and respondent profiles are not used to fully analyse the gathered data. The team made a suggestion in this area.
Detailed Human-Technology-Organization Interaction findings
-
11.3(1) Issue: Knowledge management (KM) is not systematically implemented at the station to ensure effective acquisition, transformation, transfer and retention of knowledge.
-
The station implements KM activities. A new edition of ‘Knowledge Management and Retention within Nuclear Generation’ procedure has recently been developed to replace previous one issued in 2016. However, the team observed the following:
- – A station policy regarding KM has not been developed.
- – The station has not developed and implemented a set of key performance indicators specifically linked to KM.
- – The station has not conducted a self-assessment of KM.
- – The implementation plan to introduce the new edition of ‘Knowledge Management and Retention within Nuclear Generation’ procedure has not been approved.
- – The new specification does not include requirements for KM attributes such as knowledge gaps, critical knowledge identification and knowledge mapping.
- – The fleet procedure defines few triggers to transfer knowledge such as ‘project work’, ‘outage work’, ‘external contacts’, ‘event, incident, accident’, ‘identified knowledge shortfall’. The main trigger used is ‘personnel leaving’.
- – ‘Knowledge transfer’ has been identified as a critical subject in both the annual personnel engagement and nuclear safety culture surveys.
-
Without the systematic implementation of KM the station might miss opportunities to ensure effective acquisition, transformation, transfer and retention of knowledge.
-
Suggestion: The station should consider measures to improve KM implementation to ensure effective acquisition, transformation, transfer and retention of knowledge.
IAEA Bases:
GSR Part 2:
4.21. Senior management shall make arrangements to ensure that the organization has inhouse, or maintains access to, the full range of competences and the resources necessary to conduct its activities and to discharge its responsibilities for ensuring safety at each stage in the lifetime of the facility or activity, and during an emergency response.
4.27. The knowledge and the information of the organization shall be managed as a resource.
- GS-G-3.1:
- 4.4. Data should be converted to information for the continual development of an organization’s knowledge, and senior management should treat information as a fundamental resource that is essential for making factually based decisions and stimulating innovation. To manage information and knowledge, senior management:
- – Should identify the organization’s information needs;
- – Should identify and access internal and external sources of information;
- – Should convert information to knowledge of use to the organization;
- – Should use the data, information and knowledge to set and meet the organization’s strategies and objectives;
- – Should ensure appropriate security and confidentiality;
- – Should evaluate the benefits derived from the use of the information in order to improve the management of information and knowledge;
- – Should ensure the preservation of organizational knowledge and capture tacit knowledge for appropriate conversion to explicit knowledge.
- SSR-2/2 (Rev.1) Requirement 2:
- 3.2. The management system, as an integrated set of interrelated or interacting components for establishing policies and objectives and enabling the objectives to be achieved in an efficient and effective manner, shall include the following activities:
- – Policy making for all areas of safety, which includes:
- – Setting management objectives;
- – Establishing the policy for safety;
- – Developing management and staff who value learning, have skills in creating, acquiring and
- – transferring knowledge, and can adapt the organization on the basis of new knowledge and
- – insights.
- – Policy making for all areas of safety, which includes:
-
11.4(1) Issue: The plant’s tools, techniques and performance indicators for nuclear safety culture self and independent assessment are not sufficient to fully assess nuclear safety culture.
- The station conducts a survey of the nuclear safety culture on a 2-year basis using an external organization. However, the team noted the following:
- – The station has not developed and implemented a set of key performance indicators specifically linked to the NSC.
- – The integrated company profile document for management of human performance (HU) and NSC requires the station to maintain oversight of the NSC survey. Currently the requirement to perform NSC self-assessment is not included as an accountability in the human performance lead post training profile.
- – Procedures to conduct regular NSC assessment do not exist.
- – The station set of tools to assess NSC is not complete. For example, there is no requirement for document analysis.
- – NSC survey results are not fully analysed in respect of a respondent profile.
- – NSC Survey uses an online questionnaire as the only tool to gather data. Other assessment tools such as observations, interviews, focus-groups and document analysis are not employed.
- Without the use of comprehensive nuclear safety culture assessment techniques, the station may miss the opportunity to understand and make improvements to improve nuclear safety culture.
- The station conducts a survey of the nuclear safety culture on a 2-year basis using an external organization. However, the team noted the following:
Suggestion: Station should consider enhancing its nuclear safety culture assessments and indicators.
IAEA Bases:
SSR-2/2 (Rev.1) Requirement 2:
4.34 Self-assessment by the operating organization shall be an integral part of the monitoring and review system. The operating organization shall perform systematic self assessments to identify achievements and to address any degradation in safety performance.
GSR Part 2:
6.9. Senior management shall ensure that self-assessment of leadership for safety and of safety culture includes assessment at all organizational levels and for all functions in the organization. Senior management shall ensure that such self-assessment makes use of recognized experts in the assessment of leadership and of safety culture.
6.10. Senior management shall ensure that an independent assessment of leadership for safety and of safety culture is conducted for enhancement of the organizational culture for safety.
GS-G-3.1:
2.32. The management system should provide structure and direction to the organization in a way that permits and promotes the development of a strong safety culture together with the achievement of high levels of safety performance.
6.3. Self-assessment should be conducted at all levels in the organization to assess performance and safety culture. At the organizational level it can be carried out by senior management. At the unit or work group level other managers and individuals can carry it out.
12. Long term operation
12.1. Organization and functions
The station uses an integrated asset management system to trend station risk and manage station investment. The integrated system has allowed lifetime threats to be identified and mitigating actions including investments to be planned until end of life, rather than just the usual 5 year planning cycle. The system usage is related to avoidance of future output loss by planned work to mitigate identified safety and lifetime threats. The team considered this a good practice.
The station personnel responsibilities for long term operation (LTO) are described in the appropriate Post and Training Profiles (PTP) however some of these have only very general descriptions. For example: there is only one PTP for Engineering Group Head which covers all five positions in the Engineering Department. The documents have no specification of duties and responsibilities regarding Plant Life Extension (PLEX) activities, specific competences and the required training. The team encouraged the station to develop and implement comprehensive and detailed job profiles with the required skills and competences of the personnel.
A clear corporate policy regarding ageing management and LTO has been developed. The station senior management’s commitment to provide the necessary resources is ensured through the Station and Engineering Business Plans. All PLEX projects are covered by the Business Plan, however, a PLEX concept and approach description were not in place. The team encouraged the station to develop a PLEX concept and approach description.
12.2. Scoping and screening, and plant programmes relevant to LTO
All systems, structures and components (SSCs) are in the PLEX project scope, however the scoping and screening process is not well documented and traceable. A classification of the equipment regarding lifetime management arrangements is assigned by the station which is not based on the safety classification. Commodity groups in the scope of PLEX project were formed according to their functions but there is no written methodology with grouping criteria. The team made a suggestion in this area.
12.3 Review of ageing management and ageing management programmes, and revalidation of time limited ageing analyses
Principal ageing effects and degradation mechanisms, materials and environments are described in the Technical Guidance Notes as are the necessary activities for monitoring and detecting the effects of ageing. Critical locations are described in the Intention Document before every outage with a description of types and frequency of inspections. However, there is no description or consideration of the potential degradation mechanisms in these documents. The team encouraged the station to take into account the potential degradation mechanisms to ensure continued safe operation of SSCs during the PLEX period.
The indicator ‘Physical Condition’ has been mostly red and sometimes amber for the last 3 years. The Maintenance, Inspection and Test Schedule Safety System review of Decay Heat Boiler Primary and Secondary Cooling System from 2016 contains analyses of defects and trending however, there is a conclusion about the trend of defects of only one system. There is no determination of the defect trends of the rest of the systems. The station has not applied International Generic Ageing Lessons Learned (IGALL) on site. The team encouraged the station to perform a self-assessment to take into account of IGALL, to ensure all applicable international best practices and lessons learned regarding ageing management and LTO are being taken into account.
Safety analyses will be carried out during the next license period for different safety and safety related equipment (for example: the graphite moderator). The results of these analyses will support the station decision for further operation beyond the design lifetime. The team encouraged the station to revalidate the residual lifetime assessments prior to the intended period of LTO so that the safe operation is ensured beyond the design lifetime.
Detailed long term operation findings
12.1. Organisation and functions
12.1(a) Good Practice: The station uses an integrated asset management system to trend station risk and manage station investment.
Risk Management:
The Risk Management System (Nuclear Generation Risk Log – NGRL) is used to monitor and control station risk. The system assigns a risk value based on the annualised probability of a risk occurrence multiplied by the consequence of the risk should it occur. It monitors Nuclear Safety, Industrial Safety and Generation risks and ranks them to allow prioritisation and focus. Mitigations are then raised to reduce either the probability or the consequence of the risk and these are monitored over time to ensure risk reduction. This integrates with the investment management system and asset management.
Investment Management System (IMS):
The investment management system uses risk and mitigation information from NGRL and aligns this with a request for funding. The risk information is used to prioritise which station to invest in on a risk-informed basis. IMS is then used to manage the investment until it is completed with the benefits being reflected back into the risk log.
During 2017 the station planned and executed work that reduced lifetime risk by approximately £200M. In real terms, this related to avoidance of future output loss by planned work to mitigate identified safety and lifetime threats. An example is the gas circulator lifetime research project. This work cost £2.5M and justified, through physical testing, the suitability of the gas circulator motor windings for extended life. This avoided early shutdown of Torness and Heysham 2 and hence eliminated over £80M of risk of future output loss.
The Integrated Management system brings considerable benefits to the stations LTO programme. It has allowed lifetime threats to be identified and mitigations and investments to be planned until end of life, rather than just the usual 5-year planning cycle. The station can predict investment requirements up to its current expected lifetime.
12.2. Scoping and screening and plant programmes relevant to LTO
-
12.2(1) Issue: The scoping and screening process is not well documented and traceable to ensure that the safe operation of systems, structures and components (SSCs) is guaranteed to continue during the LTO period.
- During the mission the team observed the following:
- – Equipment classification regarding lifetime management arrangements assigned by the station is not based on the safety classification. No comparison was performed between the safety classification and the station classification and the conformity between both classifications cannot be demonstrated.
- – All systems and components are included in the PLEX project scope, however, it cannot be demonstrated. For example, system B34 (Core Components) contains 13,390 components according to the Fleet Asset Information Register (FLAIR). There are 51 projects concerning PLEX activities regarding these 13,390 components. However, in the project documentation it is not specified which components are covered by a particular project. Functional groups (valves, pumps etc) are presented without component identifications. There is no clear evidence that these 13,390 components are covered by these 51 projects.
- – Commodity groups in the scope of PLEX project were formed according to their functions. There is no written methodology for the grouping criteria.
- – There is no interface between the master list of the equipment in Fleet Asset Information Register (FLAIR) and PLEX project scope.
- Without well documented and traceable scoping and screening process, it cannot be ensured that the safe operation of SSCs is guaranteed to continue during the LTO period.
- During the mission the team observed the following:
Suggestion: The Station should consider improving documentation and traceability of the scoping and screening process to ensure that the safe operation of systems, structures and components (SSCs) is guaranteed to continue during the LTO period.
IAEA Bases:
GSR Part 2:
Requirement 8:
The management system shall be documented. The documentation of the management system shall be controlled, usable, readable, clearly identified and readily available at the point of use.
SSR-2/2, rev.1:
- 4.54. The comprehensive programme for long term operation shall address:
- a) Setting the scope for all structures, systems and components important to safety;
NS-G-2.12:
4.15. To ensure that the ageing management review is resource effective, the list of identified structural elements and components important to safety that are susceptible to ageing degradation should be arranged into generic groups.
SRS-57:
- 4.1. Scope Setting Process
- The SSCs within the scope of LTO are those that perform the following safety functions [11]:
- a) All SSCs important to safety that ensure the integrity of the reactor coolant pressure boundary;
- b) All SSCs important to safety that ensure the capability to shut down the reactor and maintain it in a safe shutdown condition;
- c) All SSCs important to safety that ensure the capability to prevent accidents that could result in potential off-site exposure or that mitigate the consequences of such accidents.
- d) Other SSCs within the scope of LTO are those whose failure may impact upon the safety functions specified above.
Documentation:
The activities and results of the LTO evaluation are recorded and documented in a systematic and auditable manner that complies with the quality assurance programme in effect at the plant, and in accordance with the requirements of the national regulatory body.
Definitions
Definitions – OSART Mission
Recommendation
A recommendation is advice on what improvements in operational safety should be made in that activity or programme that has been evaluated. It is based on IAEA Safety Standards or proven, good international practices and addresses the root causes rather than the symptoms of the identified concern. It very often illustrates a proven method of striving for excellence, which reaches beyond minimum requirements. Recommendations are specific, realistic and designed to result in tangible improvements. Absence of recommendations can be interpreted as performance corresponding with proven international practices.
Suggestion
A suggestion is either an additional proposal in conjunction with a recommendation or may stand on its own following a discussion of the pertinent background. It may indirectly contribute to improvements in operational safety but is primarily intended to make a good performance more effective, to indicate useful expansions to existing programmes and to point out possible superior alternatives to ongoing work. In general, it is designed to stimulate the plant management and supporting staff to continue to consider ways and means for enhancing performance.
Note: if an item is not well based enough to meet the criteria of a ‘suggestion’, but the expert or the team feels that mentioning it is still desirable, the given topic may be described in the text of the report using the phrase ‘encouragement’ (e.g. The team encouraged the plant to…).
Good practice
A good practice is an outstanding and proven performance, programme, activity or equipment in use that contributes directly or indirectly to operational safety and sustained good performance. A good practice is markedly superior to that observed elsewhere, not just the fulfilment of current requirements or expectations. It should be superior enough and have broad application to be brought to the attention of other nuclear power plants and be worthy of their consideration in the general drive for excellence. A good practice has the following characteristics:
- novel
- has a proven benefit
- replicable (it can be used at other plants)
- does not contradict an issue
The attributes of a given ‘good practice’ (e.g. whether it is well implemented, or cost effective, or creative, or it has good results) should be explicitly stated in the description of the ‘good practice’.
Note: An item may not meet all the criteria of a ‘good practice’, but still be worthy to take note of. In this case it may be referred as a ‘good performance’, and may be documented in the text of the report. A good performance is a superior objective that has been achieved or a good technique or programme that contributes directly or indirectly to operational safety and sustained good performance, that works well at the plant. However, it might not be necessary to recommend its adoption by other nuclear power plants, because of financial considerations, differences in design or other reasons.
List of IAEA references (Basis)
Safety standards:
- SF-1; Fundamental Safety Principles (Safety Fundamentals)
- GSR Part 3; Radiation Protection and Safety of Radiation Sources: International Basic Safety Standards, Interim Edition
- SSR-2/1; Safety of Nuclear Power Plants: Design (Specific Safety Requirements)
- SSR-2/2; Safety of Nuclear Power Plants: Operation and Commissioning (Specific Safety Requirements)
- NS-G-1.1; Software for Computer Based Systems Important to Safety in Nuclear Power Plants (Safety Guide)
- NS-G-2.1; Fire Safety in the Operation of Nuclear Power Plans (Safety Guide)
- NS-G-2.2; Operational Limits and Conditions and Operating Procedures for Nuclear Power Plants (Safety Guide)
- NS-G-2.3; Modifications to Nuclear Power Plants (Safety Guide)
- NS-G-2.4; The Operating Organization for Nuclear Power Plants (Safety Guide)
- NS-G-2.5; Core Management and Fuel Handling for Nuclear Power Plants (Safety Guide)
- NS-G-2.6; Maintenance, Surveillance and In-service Inspection in Nuclear Power Plants (Safety Guide)
- NS-G-2.7; Radiation Protection and Radioactive Waste Management in the Operation of Nuclear Power Plants (Safety Guide)
- NS-G-2.8; Recruitment, Qualification and Training of Personnel for Nuclear Power Plants (Safety Guide)
- NS-G-2.9; Commissioning for Nuclear Power Plants (Safety Guide)
- NS-G-2.11; A System for the Feedback of Experience from Events in Nuclear Installations (Safety Guide)
- NS-G-2.12; Ageing Management for Nuclear Power Plants (Safety Guide)
-
NS-G-2.13; Evaluation of Seismic Safety for Existing Nuclear Installations (Safety Guide)
- NS-G-2.14; Conduct of Operations at Nuclear Power Plants (Safety Guide)
- NS-G-2.15; Severe Accident Management Programmes for Nuclear Power Plants Safety Guide (Safety Guide)
- SSG-13; Chemistry Programme for Water Cooled Nuclear Power Plants (Specific Safety Guide)
- SSG-25; Periodic Safety Review for Nuclear Power Plants (Specific Safety Guide)
- GSR; Part 1 Governmental, Legal and Regulatory Framework for Safety (General Safety Requirements)
- GS-R-2; Preparedness and Response for a Nuclear or Radiological Emergency (Safety Requirements)
- GS-R-3; The Management System for Facilities and Activities (Safety Requirements)
- GSR Part 4; Safety Assessment for Facilities and Activities (General Safety Requirements 2009)
- GS-G-4.1; Format and Content of the Safety Analysis report for Nuclear Power Plants (Safety Guide 2004)
- SSG-2;; Deterministic Safety Analysis for Nuclear Power Plants (Specific Safety Guide 2009)
- SSG-3; Development and Application of Level 1 Probabilistic Safety Assessment for Nuclear Power Plants (Specific Safety Guide 2010)
- SSG-4; Development and Application of Level 2 Probabilistic Safety Assessment for Nuclear Power Plants (Specific Safety Guide 2010)
- GS-R Part 5; Predisposal Management of Radioactive Waste (General Safety Requirements)
- GS-G-2.1; Arrangement for Preparedness for a Nuclear or Radiological Emergency (Safety Guide)
- GSG-2; Criteria for Use in Preparedness and Response for a Nuclear and Radiological Emergency
- GS-G-3.1; Application of the Management System for Facilities and Activities (Safety Guide)
- GS-G-3.5; The Management System for Nuclear Installations (Safety Guide)
- RS-G-1.1; Occupational Radiation Protection (Safety Guide)
- RS-G-1.2; Assessment of Occupational Exposure Due to Intakes of Radionuclides (Safety Guide)
- RS-G-1.3; Assessment of Occupational Exposure Due to External Sources of Radiation (Safety Guide)
- RS-G-1.8; Environmental and Source Monitoring for Purpose of Radiation Protection (Safety Guide)
- SSR-5; Disposal of Radioactive Waste (Specific Safety Requirements)
- GSG-1; Classification of Radioactive Waste (Safety Guide 2009)
- WS-G-6.1; Storage of Radioactive Waste (Safety Guide)
- WS-G-2.5; Predisposal Management of Low and Intermediate Level Radioactive Waste (Safety Guide)
INSAG, Safety Report Series:
- INSAG-4; Safety Culture
- INSAG-10; Defence in Depth in Nuclear Safety
- INSAG-12; Basic Safety Principles for Nuclear Power Plants, 75-INSAG-3 Rev.1
- INSAG-13; Management of Operational Safety in Nuclear Power Plants
- INSAG-14; Safe Management of the Operating Lifetimes of Nuclear Power Plants
- INSAG-15; Key Practical Issues In Strengthening Safety Culture
- INSAG-16; Maintaining Knowledge, Training and Infrastructure for Research and Development in Nuclear Safety
- INSAG-17; Independence in Regulatory Decision Making
- INSAG-18; Managing Change in the Nuclear Industry: The Effects on Safety
- INSAG-19; Maintaining the Design Integrity of Nuclear Installations Throughout Their Operating Life
- INSAG-20; Stakeholder Involvement in Nuclear Issues
- INSAG-23; Improving the International System for Operating Experience Feedback
- INSAG-25; A Framework for an Integrated Risk Informed Decision Making Process
- Safety Report Series No.11; Developing Safety Culture in Nuclear Activities Practical Suggestions to Assist Progress
- Safety Report Series No.21; Optimization of Radiation Protection in the Control of Occupational Exposure
- Safety Report Series No.48; Development and Review of Plant Specific Emergency Operating Procedures
- Safety Report Series No. 57; Safe Long Term Operation of Nuclear Power Plants
Other IAEA Publications:
- IAEA Safety Glossary; Terminology used in nuclear safety and radiation protection 2007 Edition
- Services series No.12; OSART Guidelines
- EPR-EXERCISE-2005; Preparation, Conduct and Evaluation of Exercises to Test Preparedness for a Nuclear or Radiological Emergency, (Updating IAEATECDOC-953)
- EPR-METHOD-2003; Method for developing arrangements for response to a nuclear or radiological emergency, (Updating IAEA-TECDOC-953)
- EPR-ENATOM-2002; Emergency Notification and Assistance Technical Operations Manual
International Labour Office publications on industrial safety:
- ILO-OSH 2001; Guidelines on occupational safety and health management systems (ILO guideline)
- Safety and health in construction (ILO code of practice)
- Safety in the use of chemicals at work (ILO code of practice)
Team composition of the OSART Mission
MARTYNENKO, Yury – IAEA
Division of Nuclear Installation Safety
Review area: Team Leader
Years of Nuclear Experience: 34
JIANG, Fuming - IAEA
Division of Nuclear Installation Safety
Review area: Deputy Team Leader
Years of nuclear experience: 21
DUTTO, Jean-Baptiste – France
EDF
Review area: Leadership and Management for Safety
Years of nuclear experience: 24
MAGUIRE, Paula – Canada
Consultant
Review area: Training & Qualification
Years of nuclear experience: 31
Tarnoy, Laszlo – Hungary
MVM Paks NPP Ltd
Review area: Operations 1
Years of nuclear experience: 27
TARARIN, Aleksei – Russian Federation
Leningrad NPP
Review area: Operations 2
Years of nuclear experience: 15
TRAAS, William - The Netherlands
N.V. EPZ
Review area: Maintenance
Years of nuclear experience: 21
BILIC ZABRIC, Tea – IAEA
Division of Nuclear Installation Safety
Review area: Technical Support
Years of nuclear experience: 29
NOEL, Marc – Belgium/European Commission
EC-Joint Research Centre
Review area: Operating Experience Feedback
Years of nuclear experience: 18
NILSSON, Virva – Sweden
Forsmarks Kraftgrupp
Review area: Radiation Protection
Years of nuclear experience: 25
BURKE, Bill – United States of America
INPO
Review area: Chemistry
Years of nuclear experience: 39
TUOMISTO, Harri Juhani - Finland
Fortum Power and Heat Oy
Review area: Emergency Preparedness and Response
Years of nuclear experience: 40
SUGAHARA, Jun – IAEA
Division of Nuclear Installation Safety
Review area: Accident Management
Years of nuclear experience: 17
VOLKOV, Eduard - Russian Federation
Science Research Centre ‘PROGNOZ’
Review area: Human-Technology-Organization Interaction
Years of Nuclear Experience: 22
KIRILOVA, Desislava – Bulgaria
Consultant
Review area: Long Term Operation
Years of Nuclear Experience: 17
OZEROV Evgenii – Russian Federation
ROSENERGOATOM
Observer
Years of Nuclear Experience: 14