Typhoon support solutions
The Defence Electronics and Components Agency (DECA) continues to grow support solutions for Typhoon. Ian Ford and Derek Underwood explain how we are working to reduce costs by providing innovative repair-not-replace solutions.
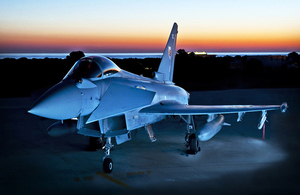
Typhoon at RAF Akrotiri in Cyprus © Crown copyright
For the past six years, we has been working closely with the Typhoon In-service Delivery Team to provide cost effective alternative support solutions to avoid unnecessary costs and extended lead times on replacement Typhoon items. We have worked together to produce repair schemes where items could be repaired not replaced, work that originally focused around cables, but is now expanding into aircraft components.
Similarly, we have produced calibration solutions after the Delivery Team identified issues with the existing supply chain. With the signing and launch of the new Typhoon Total Availability eNterprise (TyTAN) contract, we are well positioned to continue to offer further innovative solutions contributing to significant cost savings as well as improving equipment availability.
Here Derek and I explain specific examples where we have provided best value for defence.
Typhoon headset cable modification
We have carried out modifications to Typhoon headset extension lead cables to support MOD operational requirements.
This important modification enabled improved communication between pilot and ground crew helping to ensure effective aircraft release.
Our ability to apply our own skill and knowledge, in the absence of access to any manufacturer information, enabled our team to produce electrical schematic drawings that ensured the Test Equipment Product Lines department could modify the cables.
Just two days after receiving the equipment at DECA, 41 squadron successfully tested an initial modified cable at RAF Coningsby. On proof of concept, further cables shortly followed with the final consignment hand delivered to the Typhoon Support Centre at RAF Coningsby.
In a letter D Rhodes, from the Typhoon Support Centre in Coningsby, said,
On behalf of the Typhoon Support Centre I want to take the time to express my appreciation for the exceptional service provided by the DECA Engineering Development Team during the development and delivery of this requirement for Typhoon.
Typhoon generator test stand
Currently Typhoon power generator testing is undertaken by the Original Equipment Manufacturer (OEM). To overcome extended turn-round-times a new test facility has been commissioned by the MOD and is located at DECA. This compliments the existing Power generator test and repair capability allowing the filter bench testing of Typhoon generators.
Key milestones already achieved:
- Typhoon Generator Test Rig arrived at DECA in February
- purpose built facility ready for installation and commissioning
- first Integrated Drive Generator stripped and re-built to prove tooling, DECA capability and procedures
Repair-not-replace test equipment cables
Over the past four years, we have provided consultancy support to the Typhoon In-service Delivery Team in developing repair solutions for test equipment cables. The portfolio has increased to 84 different cable types resulting in over 720 cable repairs. This includes fibre optic repair capabilities as well as cable production and manufacture.
On-Shore special-to-type test equipment calibration
DECA has provided calibration consultancy expertise to Typhoon for many years. This has resulted in the development of in-house calibration solutions for over 75 different line items in our Tri-service calibration laboratory including a managed service to sub-contractors.
TEMPEST and Electro Magnetic Compatibility (EMC) capability
We supported the Typhoon In-service Delivery Team to overcome an operational issue and improve the solution for aircraft cryptographic data fill cables.
As part of this, we developed a relationship with the Communications Electronic Security Group approved Test House for Tempest and EMC testing.
After successful Tempest/EMC testing and In-service Delivery Team approval of the prototype cables, DECA are now manufacturing cables to support the Typhoon fleet.
Typhoon maintenance platform inspection contract
We have recently won a contract to provide routine maintenance to Typhoon adjustable maintenance platforms at RAF Coningsby.
The contract will involve on-site inspections of the equipment that is vital for the maintenance of Typhoon. Maintenance will be carried out to meet Lifting Operations and Lifting Equipment Regulations ensuring the compliance and safety of the platforms. Under this contract, the RAF has agreed that our team will now service all of these platforms at the Coningsby site.
Typhoon composite cylinders inspection and test
The DECA Airborne Bottle Bay has begun to inspect composite cylinders in support of Typhoon following on from the successful work carried out in support of Tornado by our team at Stafford.
The specialist cylinders, which carry nitrogen and air, are smaller and lighter than the steel cylinders traditionally used and require our specialist support capabilities. The cylinders are sent to us for inspection, examination, hydrostatic test to BSEN 11623:2002 and BSEN 1802:2002 standards and pressure tested up to 6526 psi before being prepared for dispatch to front line Typhoon units.
The Airborne Bottle Bay is UKAS accredited and is able to perform hydrostatic testing up to a massive 10,000psi!
Bespoke container provides storage solution for Typhoon 18CWT hoist
DECA Carpentry and Lifting Tackle teams have designed and provided a bespoke container solution for the Typhoon 18 CWT hoist.
The Typhoon airframe teams found that separating the hoist arm from the winch to store had the potential to lead to problems with over-winding. The Typhoon teams approached us for a storage solution to enable the hoist arm to remain attached to the winch mechanism for storage preventing this from occurring.
We designed a specific-to-content-container to accommodate the hoist arm, adding internal furniture to ensure the hoist fitted in its entirety into one container together with any accessories. The team also ensured the design was weighted in such a way that the container was balanced throughout the whole length overcoming any issues when moving the container given the considerable weight of the winch!
DECA Head of Account Management Derek Underwood concluded by saying.
Through this work, we are providing real and tangible cost savings to MOD as well as significantly reducing turn -round-times. This benefits Typhoon operations both in the UK and worldwide by increasing the availability of the Typhoon platform.
These recent increases in the our portfolio prove the growing confidence that the customer and industry have in our capability to support Typhoon. This reinforces DECA’s involvement in the new TyTAN supply chain.
Aled Evans Project Manager for Typhoon Avionic Test equipment also said,
I have, over the last few years, worked with DECA developing innovative support solutions which has included calibration of test equipment, manufacture and repair of associated cables. This service has provided improved turn-round times along with value-for-money solutions.
Flexibility of the service has seen DECA provide support to the Typhoon at various locations in the UK and overseas. Recent initiatives have included providing EMC and TEMPEST clearance for newly designed cryptographic cables and a soon to be installed Typhoon Generator Test Stand to provide a test and repair service for various generators. DECA continues to provide a responsive, flexible and cost saving service, which will continue under the new TyTAN contract.