Report 04/2022: Runaway of a road-rail vehicle at Belle Isle Junction
RAIB has today released its report into a runaway of a road-rail vehicle at Belle Isle Junction, 16 May 2021.
The mobile elevated work platform involved in the incident.
Summary
At around 03:30 hrs on Sunday 16 May 2021, a road-rail vehicle (RRV) known as a Mobile Elevating Work Platform (MEWP) ran away while being on-tracked at a road-rail access point near Belle Isle Junction in north London. The MEWP ran downhill for approximately 600 metres before coming to a stop in a tunnel. Although no one was injured, the operator jumped from the road-rail vehicle before it entered the tunnel. There was no damage to the infrastructure or the MEWP. The incident took place at a time when the area was under possession for maintenance activities. As a result, there were no train services in the vicinity.
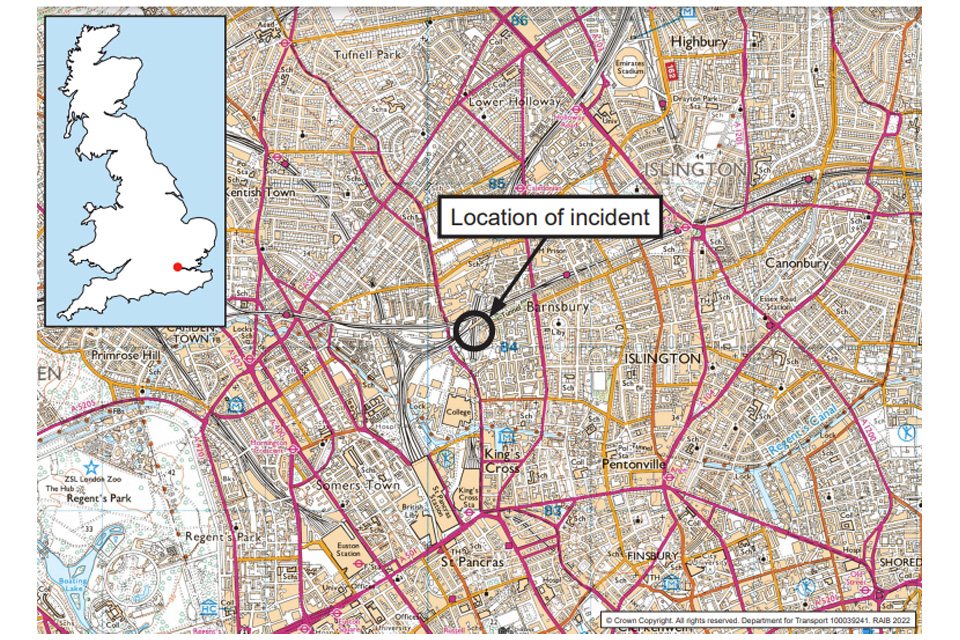
The MEWP ran away because it entered service with ineffective rail-wheel brakes and staff working with it were unable to stop the runaway. The brakes were ineffective because a valve in the braking system had been left open following maintenance. The possibility of this had not been recognised during the design or risk assessment of the brake system, and the situation had not been identified during operation or regular in- service testing.
Two underlying factors were identified following our investigation. These were that the risk assessment undertaken in support of a modification to the machine to fit a direct rail wheel braking system was incomplete, and that the company responsible possibly did not have a thorough understanding of the unmodified machine or its original conversion for rail use.
RAIB has made two recommendations. One is addressed to the company which designed and fitted the direct rail wheel braking system, to revise its process for risk assessment, and the second to the owner of the machine, to review its strategy for confirming the ongoing integrity of the direct rail wheel brake system.
We have also identified two learning points. These reinforce the importance of organisations which design and implement changes to on-track plant sourcing the original design information to inform their decisions, and of those supplying and operating road-rail vehicles ensuring that suitable facilities are available for in-service testing.
Organisations involved
Network Rail owns and maintains the railway infrastructure where the incident occurred.
Morgan Sindall Infrastructure (referred to as Morgan Sindall in the rest of this report) was a principal contractor to Network Rail for the King’s Cross remodelling project, on which the MEWP was being used.
Pod-Trak Ltd (referred to as Pod-Trak in the rest of this report), a subsidiary of Pod-Trak Group, owned, maintained and supplied the MEWP involved.
The MEWP was manufactured in Italy and supplied to the UK in 2013 by ProMax Access Ltd (referred to as ProMax in the rest of this report), the manufacturer’s UK agent.
Allan J Hargreaves Plant Engineers Ltd (referred to as Hargreaves in the rest of this report) modified the MEWP with its own design of direct rail wheel braking system (DRWB) in 2014.
Network Rail, Morgan Sindall, Pod-Trak, ProMax and Hargreaves all freely co- operated with the investigation.
Rail equipment involved
The MEWP was a Platform Basket RR14 Evo weighing 12.8 tonnes. It is known as a type 9b4 ‘high-ride’ RRV.
In rail mode, the rail wheels of this type of high-ride RRV are lowered onto the rails and driven and braked by friction forces transmitted through the tyres of the road wheels onto stubs fitted at the ends of each rail axle.
During road use these axles are raised out of contact with the road wheels.
When being configured for use on rail, the rail wheels are hydraulically lowered onto the track. When the rail wheels come into contact with the rail, they lift the MEWP, and this movement continues until the rail wheel stubs are pressed firmly against the road wheel tyres.
Actions reported as already taken or in progress relevant to this report
In June 2021 Hargreaves issued a bulletin to owners of OTP with the Hargreaves DRWB system. This bulletin described an engineering solution intended to prevent machines entering service with their park brake valve left open. Hargreaves required that MEWPs fitted with its DRWB system be modified at the earliest available opportunity.
Hargreaves reported that it has been developing its approach to the risk assessment of its designs and modifications since the design of the DRWB system in early 2014, and believes that its risk assessment process is more rigorous than at the time of the design of the machine involved in the incident.
Since the incident, Morgan Sindall has ensured that all of its safe system of work planners who missed the briefing on Module 5 of NR/L2/OHS/019 have now been briefed. It has undertaken some sampling of Safe Work Packs to understand the level of compliance and to ensure that appropriate consideration has been given to the risk of runaway plant.
Recommendations and learning points
Recommendations
The following recommendations are made:
-
The intent of this recommendation is for Hargreaves to fully identify and appropriately mitigate the risks associated with its on-track plant designs. Hargreaves should continue to review and revise as necessary its process and associated guidance for assessing the risks from its designs of rail plant, so that it specifically requires consideration of errors that may occur during operation and maintenance. This should include a requirement to update and revise risk assessments based on operational feedback and the contents of, and any changes to, operating and maintenance procedures.
-
The intent of this recommendation is for Pod-Trak to have a regime that provides it with a reliable understanding of the integrity of the direct rail wheel brake systems on its on-track plant, so that the machines only enter service with fully functional brakes. Pod-Trak should review its strategy for confirming the ongoing functional performance of the direct rail wheel brake systems on its on-track plant to confirm that it gives sufficient confidence in the integrity of the system throughout its time in service. This review should include consideration of the checks to be undertaken before vehicles are reintroduced into service following maintenance and inspection, the checks to be undertaken on an ongoing basis and any necessary pre-use checks. It should also identify and mitigate the risks associated with live testing. From the revised strategy Pod-Trak should issue updated procedures based on this strategy and brief them to relevant staff as part of their implementation.
Note: this recommendation may also apply to other plant operators.
Learning points
RAIB has identified the following important learning points:
-
Organisations that design and implement changes to on-track plant are reminded of the importance of ensuring that original design information is sourced to allow for informed design decisions and accurate risk assessments.
-
Suppliers and operators of RRVs are reminded of the importance of ensuring that suitable facilities are available for undertaking regular in service testing.
Notes to editors
- The sole purpose of RAIB investigations is to prevent future accidents and incidents and improve railway safety. RAIB does not establish blame, liability or carry out prosecutions.
- RAIB operates, as far as possible, in an open and transparent manner. While our investigations are completely independent of the railway industry, we do maintain close liaison with railway companies and if we discover matters that may affect the safety of the railway, we make sure that information about them is circulated to the right people as soon as possible, and certainly long before publication of our final report.
- For media enquiries, please call 01932 440015.