Derailment of a rail head treatment train near Dunkeld & Birnam, 29 October 2018
Published 31 January 2019
1. Important safety messages
This accident demonstrates that the formation of large wheel flats on rail vehicles can lead to derailment. It is therefore important that:
- operators and maintainers of Rail Head Treatment Trains (RHTTs) closely monitor the condition of wheels and braking systems when operating in low adhesion conditions, due to the increased likelihood of the formation of large wheel flats
- operators of freight trains, and other specialist trains derived from freight wagons (including RHTTs), undertake suitable roll-by examinations on departure from yards, to detect non-rotating wheels
- maintainers of freight wagons have a process in place to control the isolation of handbrake interlocks on freight wagons
- staff preparing freight trains for departure, check that handbrakes are fully released and do not place sole reliance on handbrake interlocks
2. Summary of the accident
At around 22:15 hrs on 29 October 2018, a rail head treatment train (RHTT) comprising a Class 67 locomotive and two specialised wagons, operated by DB Cargo and travelling between Inverness and Perth, derailed just after passing Dunkeld and Birnam station. Both wheelsets of the 4th bogie in the train derailed at a set of trailing points, ran for around 100 metres causing significant track damage, and then rerailed at the next set of trailing points. The train then continued a further 15 miles to Perth.
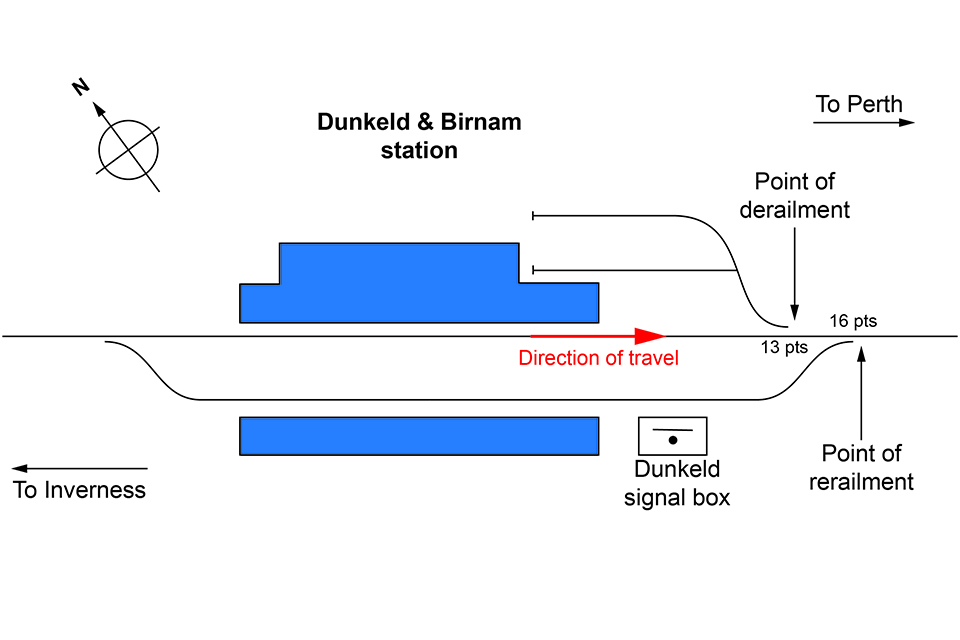
Simplified diagram of the track layout at Dunkeld and Birnam station
3. Cause of the accident
The RHTT was crewed by a driver, and an operative who operated the rail head treatment equipment in accordance with a pre-defined plan. At some point in the journey, the leading wheelset of the 4th bogie (the trailing bogie of the leading wagon) began to slide rather than rotate, resulting in the creation of a large wheel flat on both its wheels. As the train progressed on its journey, these flats developed, wearing a groove into the wheel treads and creating features on the outside edges of the wheels called ‘false flanges’.
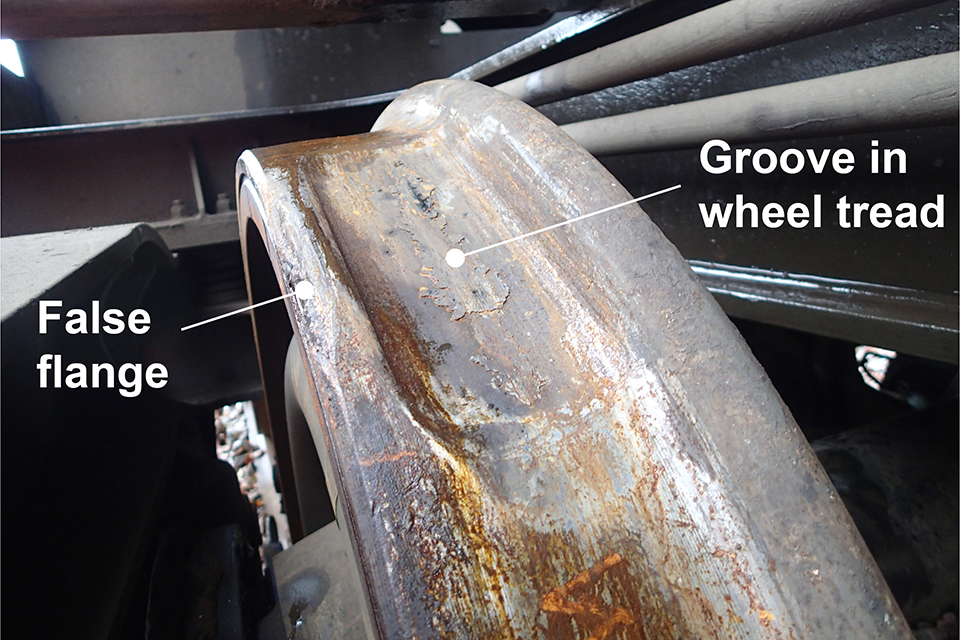
The large flat on the leading left-hand wheel of the 4th bogie and its associated false flange
As the flatted wheelset passed over number 13 points, just south of Dunkeld and Birnam station, the false flange on the left wheel engaged with the converging switch and stock rails. Rather than the wheel tread transferring from the switch rail to the stock rail in the normal way, the false flange on the left-hand wheel became trapped between the stock and switch rail. This caused the outside face of the wheel to run along the gauge face of the stock rail, while the right-hand wheel was pushed up against the opposite stock rail. This led to the wheelset pushing the rails apart, resulting in high lateral forces on the stock rails which in turn overloaded the rail fastenings and in some places the wooden sleepers.
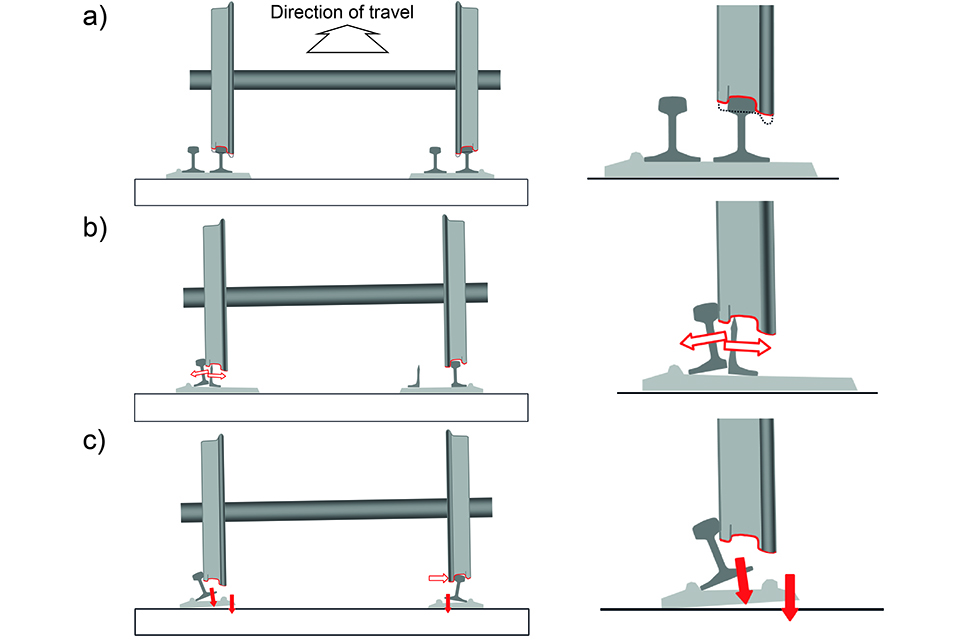
The derailment mechanism (and close up of the left wheel) showing: a) the false flange on the left wheel between the switch and stock rails, b) the false flange trapped between the rails and c) the resultant high lateral forces pushing the rails apart
This directly led to derailment of the leading wheelset of the 4th bogie, shortly followed by derailment of the bogie’s trailing wheelset. They ran derailed for approximately 100 metres, before rerailing at 16 points, the next converging set of points. The derailment caused extensive track damage through this section, including broken rails, which resulted in a signalling fault.
The signaller at Dunkeld signal box heard loud noises as the train derailed and contacted the train driver by radio. The driver reported to the signaller that he heard a rumble and experienced a reduction of speed. However, because the train had rerailed, its behaviour had returned to normal. The driver believed he had run over some sand on the track and confirmed to the signaller that he was able to continue. Due to the noise, and the signalling fault, the signaller decided to visually inspect the track in person, rather than caution the next train. Upon discovering the track damage, he blocked the line and contacted the route control office, by which time the RHTT had arrived in Perth. The signaller at Perth spoke to the route control office, then informed the driver of the RHTT about the track damage at Dunkeld and that the train would not be permitted to continue further.
The RHTT fleet is deployed during the autumn leaf-fall season to combat low adhesion conditions caused by leaves on the line. This is done through a combination of cleaning of the rail head with high pressure water, and application of an adhesion modifier. The RHTT involved in this derailment consisted of a Class 67 locomotive and two FEA F wagons specifically built to carry the rail head treatment equipment. The first wagon in the direction of travel included two high pressure water jets positioned immediately behind the leading bogie. Each wagon carries three modules that can be selected to suit the tasks of the train at any particular time, including a generator and pumping equipment, water tanks and/or adhesion modifier tanks.
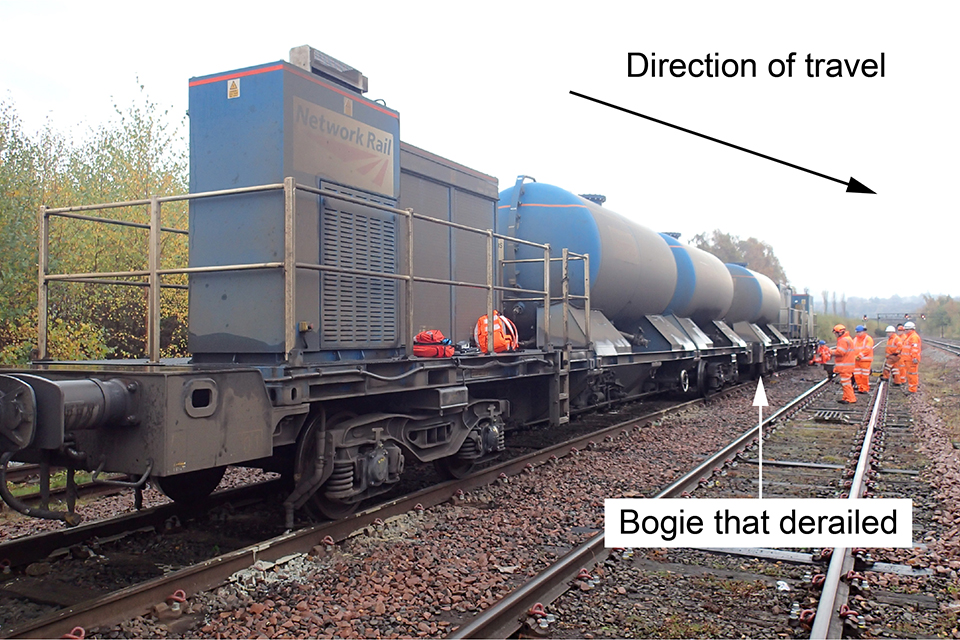
The RHTT wagons involved
Each wagon wheel has a single brake block. When the train brakes are applied, the geometry of mechanical links in the brake system cause the brake blocks on the wheels closest to the centre of the wagon (the inboard wheels) to touch first, closely followed by the brake blocks against the outboard wheels. Each wagon also has a mechanical handbrake which applies the brake blocks to one of the wagon’s bogie. The handbrake is activated and released by turning a wheel.
Wheel flats occur when a train’s wheels slide along the rail instead of rotating. This can be caused by the brakes failing to release when commanded to; a handbrake being left on; brakes being applied too heavily; or the train braking normally in an area of low adhesion.
In order to mitigate against a handbrake being left on, the RHTT wagons are fitted with a handbrake interlock system. If the handbrake has been applied, the train’s brake pipe will not be allowed to pressurise and the train brake cannot be released. Escaping air from the brake pipe is usually audible to train preparation staff in this situation.
It is normal practice in freight yards, for train preparers to carry out a ‘roll-by’ test when a freight train leaves the yard in order to check that all the train’s wheels are freely rotating. However, DB Cargo’s instructions for dispatching the RHTT from Inverness Millburn yard did not include a roll-by test. The operative of the RHTT, who prepared the train before the journey to Perth, reported to the RAIB that he checked the handbrakes but he did not undertake a roll-by test. He believed that both wagons were fitted with a working handbrake interlock which should have prevented the train from moving if a handbrake had been left on.
When the RHTT wagons were inspected after the derailment, the handbrake interlock on the first wagon had been isolated. The RAIB has not been able to identify why the handbrake interlock had been isolated, or by whom. The operative who prepared the train reported to the RAIB that he was not aware the handbrake interlock had been isolated. There was no card or other sign on the affected wagon to warn about the isolation. According to records provided to the RAIB, a rolling stock technician had also examined the RHTT earlier that day and signed off the handbrakes, amongst other equipment, as being fit for service. Because the handbrake interlock was isolated, there was nothing to stop the driver driving the RHTT with the handbrake accidentally left fully or partially applied.
It has not been possible to confirm the exact status of the handbrake during the journey. The brake blocks associated with the wheels which had the large flats showed signs of excessive heat being generated, consistent with the brake blocks rubbing against the wheels for a significant period of time. However, the other wheelset on the same bogie did not exhibit any wheel flats or heat marks indicating that its brake blocks had not been rubbing against the wheels and that the handbrake was not fully applied on this bogie. Although the RHTT operative stated that he performed handbrake checks, the condition of the inboard brake blocks indicates that they were rubbing against the wheels. If this was the case, the inboard wheels would have been susceptible to wheel flats in low adhesion conditions.
The operative of the RHTT stated to RAIB that the last time he had used the handbrakes was during a short run to Moy the day before. On that trip he reported that he had only applied the handbrake on the other wagon while at Moy and removed it for the return journey. He reported that he did not operate the handbrakes on the wagons after the journey on the previous day. He also reported that, other than to check the handbrakes were off prior to departure, he did not operate the handbrakes at the start of the journey to Perth.
The nature of the RHTT’s daily work, and the conditions it operates in, means that it regularly experiences very low adhesion conditions. Evidence from Network Rail’s engineers responsible for the RHTT fleet indicates that wheel flats are common on RHTTs, and that wheels are routinely changed once or twice during the leaf-fall season, which usually lasts from early October to early December each year. The wheelsets either side of the water jets (the two inboard wheelsets on the wagon) are considered the most susceptible to wheel flats as they are exposed to airborne water and jetting debris, and pass over a saturated rail during rail treatment operations.
4. Previous similar occurrences
There are significant similarities between this accident and a derailment at Hatherley, near Cheltenham Spa, on 18 October 2005 (RAIB report 08/2006). That derailment was caused by false flanges forming on one of the wagon’s wheelsets. The wagon ran derailed for around four miles, causing extensive track damage and partially blocking the line for eight days. The false flanges on the derailed wheel had been caused by the wheelset being dragged from its origin at Bescot Yard, with its handbrake applied. The applied handbrake and the dragging wheelset were not detected during the preparation, dispatch or journey of the train. The wagon was not fitted with a handbrake interlock. The RAIB made recommendations relating to handbrakes checks, and the effectiveness and availability of roll-by examinations.
On 5 January 2006, large wheel flats developed on a freight train travelling from Meldon Quarry, Devon (RAIB report 27/2006). These flats caused high impact loads to be exerted on the track, resulting in a broken rail at Urchfont, Wiltshire, and two further broken rails at Kennington, near Oxford. The wheel flats were likely formed by the wheels sliding under low-adhesion conditions on a long descending gradient from Meldon Quarry. No roll-by test was undertaken at the exit from the Meldon Branch line, and the flats were not detected during the subsequent journey. The wagon involved was fitted with a working handbrake interlock and therefore the flats were not caused by a handbrake being left on. The RAIB attributed the most likely cause to a combination of the long descents in slippery rail head conditions and a driving style which was not appropriate for those conditions.