Defence scientists investigate helicopter engine erosion
Defence scientists are investigating how to protect helicopter engines from a common problem that occurs in Afghanistan.
![An RAF Chinook helicopter throws up dust clouds during landing (library image) [Picture: Petty Officer Hamish Burke, Crown copyright]](https://assets.publishing.service.gov.uk/media/5a620cfc40f0b63b5bc8f6cf/s300_Chinook.jpg)
An RAF Chinook helicopter throws up dust clouds during landing
Materials experts from the Defence Science and Technology Laboratory (Dstl) are working to protect helicopter engines from sand erosion.
Gas turbine engines in helicopters suck in air from the surrounding environment. In desert conditions, particularly during take-off and landing, the air contains sand particles that damage the engine’s components.
When components are damaged by sand erosion, the engine is forced to work harder, burning more fuel and struggling to produce the required power. Sand-eroded components need to be replaced more often, resulting in costly repair bills and loss of capability as helicopters are taken out of service for maintenance.
To investigate whether erosion-resistant coatings could be the answer, an international project was set up by The Technical Cooperation Program (TTCP).
TTCP enables technical collaboration on specific issues between defence organisations in the UK, United States, Canada, Australia and New Zealand.
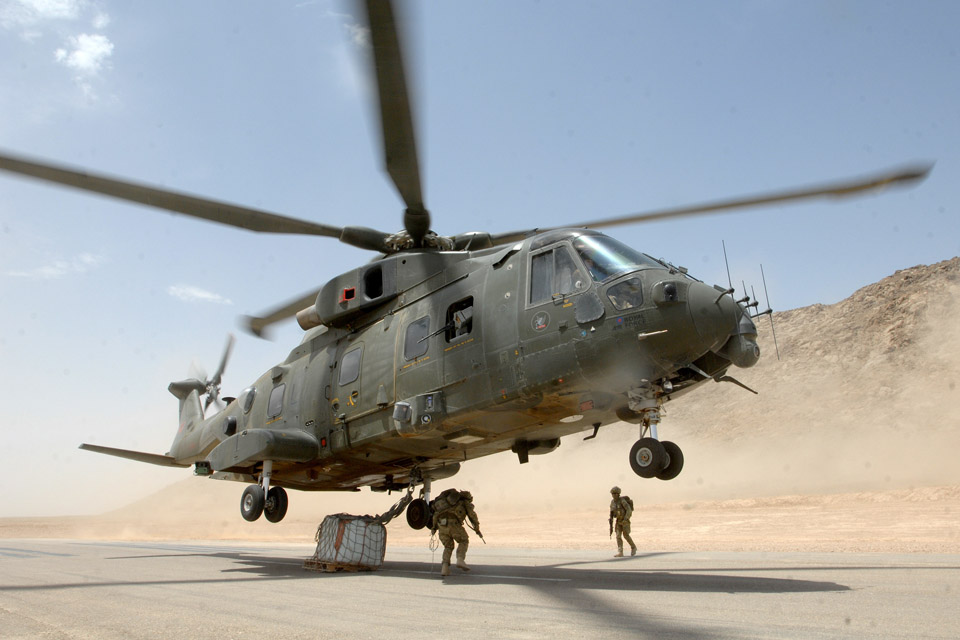
An RAF Merlin helicopter takes off with an underslung load in Afghanistan (library image) [Picture: Sergeant Andy Reddy, Crown copyright]
The UK contribution was to design and conduct effective and reliable tests that would indicate the relative strengths and limitations of a number of commercially available coatings.
Dstl identified that the University of Birmingham had suitable facilities within its metallurgy and materials department to support this work.
The tests that have been conducted include measuring bending stress on small specimens. Since the specimen is rotating at 3,000 revolutions per minute, a test of 1 million cycles can be conducted in around 11 hours.
Tests undertaken in Australia, Canada and New Zealand looked at hardness, adhesion and erosion, enhancing the international defence community’s understanding of commercially available products.
Industry suppliers in the UK and Canada applied their coatings to the test specimens without charge. In exchange, they will find out how their coatings performed in 5 tests and have ongoing support from the international defence organisations, helping them to improve their technology for defence applications.
Dstl’s involvement in this project was funded by the Ministry of Defence (MOD) via the Materials and Structures Science and Technology Centre.
The results of the tests are already being used by MOD as it assesses technologies to protect its helicopter engines.