Summary of learning - 5. Freight train derailments - v4. March 2023
Published 2 April 2020
1. Purpose of this summary
The purpose of this document is to provide a repository of some of the most important areas of learning identified in RAIB’s investigations to date, cross-referenced to relevant reports. It therefore provides a reference source for those looking to understand real-world railway safety issues and potential control measures.
When preparing this document, RAIB has selected those issues which:
- have recurred in different RAIB investigations
- have still to be fully addressed
- could be a factor in the cause of a fatal accident
RAIB is aware that many of the issues raised have already been the subject of actions by duty holders when responding to RAIB recommendations, or are in the process of being addressed. The inclusion of a topic in this document should not be taken to mean that no action has been taken in response to relevant recommendations. However, its inclusion indicates that RAIB is of the view that the issue still needs to be actively managed by duty holders.
The current status of each recommendation made by RAIB can be checked by reference to the Index of RAIB recommendations, and details of the actions taken are published by ORR.
It is not the purpose of this document to quantify the risk associated with each of the identified safety issues. Readers seeking to understand the overall risk of harm associated with various dangerous events should refer to RSSB’s Annual Safety Performance Report. This presents historical information on actual harm caused, and estimates of risk based on extensive modelling.
2. Overview
Freight train derailment makes up 40% of the risk of freight train operation (RSSB Annual Health and Safety Report 2022 [Freight]).
Every derailment on a running line creates the potential for derailed vehicles to collide with a passenger train (as occurred on 23 March 2020 at Bromsgrove, report 14/2020). Although this accident resulted in significant damage, no one was hurt in the collision. However, in other circumstances, a collision between a passenger train and derailed freight vehicles may have disastrous consequences. The derailment of a freight train on the East Coast main line near Thirsk in 1967 resulted in the death of seven passengers when an express train on the adjacent line ran into derailed freight vehicles.
Freight train derailments can also cause significant damage to railway infrastructure and result in major environmental damage (as occurred on 26 August 2020 at Llangennech, report 01/2022). They also have the potential to affect the safety of people in stations, on land adjoining the railway and more broadly in our towns and cities. For this reason, RAIB attaches great importance to understanding the sometimes complex causes of freight train derailment.
Derailments can have a number of causes. Some of these relate to the condition of the wagon: the way it has been loaded, the maintenance of the running gear and braking system, and the wear and profile of the wheel treads and flanges. Other factors can include the design of the vehicle (particularly the suspension), the geometry of the track, the condition of the railhead, or the effects of a combination of faults.
Wear and degradation of vehicles and track, even within the limits of industry’s standards for maintenance, may interact with each other and with the way the wagons are loaded to produce an unsafe condition which results in derailment. We believe that the industry needs to better understand this interaction and do more to avoid creating the conditions which lead to derailments.
3. Important areas for safety learning
The main topics of concern to RAIB are described below.
3.1 Vehicle design
It is important that vehicles are designed to maximise their resistance to derailment. RAIB has found in several investigations that the design of vehicle suspensions can contribute to poor dynamic performance, especially when combined with inadequate lubrication. This was a factor in the derailments at Washwood Heath in 2006 (report 39/2007) and Ely in 2007 (report 02/2009), as well as the derailments at Gloucester and Camden Road on the same day in 2013 (report 20/2014 and report 21/2014).
The likelihood of derailment can be increased by high rotational stiffness in a bogie, and by variations in vertical stiffness in primary suspension systems. Some derailments are associated with designs of wagon that have bogies that use, for example, friction rather than viscous damping. These characteristics can be the result of design decisions which, combined with less than adequate maintenance, can create a dangerous situation. Modern design standards have been revised to take account of these issues.
3.2 Vehicle condition
The standard of maintenance of freight wagons has been a matter of concern in several RAIB investigations. On the South Wales main line at Llangennech in August 2020 (report 01/2022), a freight train carrying oil products derailed at a diverging junction because a malfunction within the braking equipment of one of its wagons had generated significant wheel flats. The consequent damage to the wagons resulted in a significant spillage of fuel and a major fire. During its investigation, RAIB issued Urgent Safety Advice to the railway industry covering the need for appropriate arrangements to manage the safety risk associated with malfunction of wagon braking systems.
RAIB’s investigation concluded that poor maintenance was probably a factor in the accident, and that insufficient action had been taken in response to a similar but less serious accident in 2017. RAIB also found that the rail freight sector’s approach to the maintenance and monitoring of the condition of wagons was not based upon best practice. Consequently, we have made recommendations covering a comprehensive review of the management of the maintenance of wagons carrying dangerous goods.
A poor standard of maintenance was also found in our investigation into an accident at Carpenters Road North Junction, London, in 2019 (safety digest 07/2019), when components of a wagon’s braking system fell off during the journey, and got under the wagon’s wheels and derailed it.
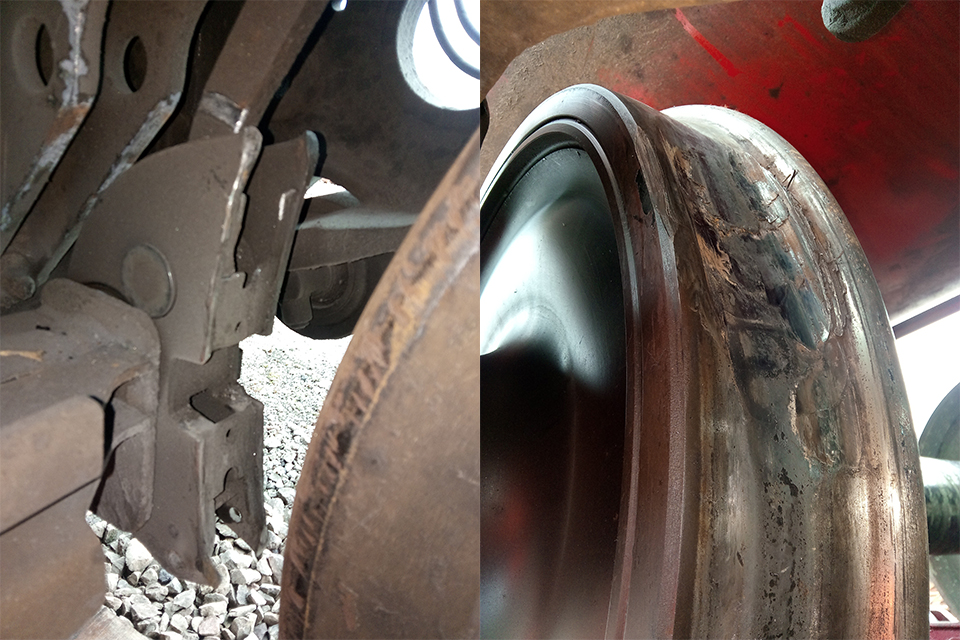
Missing components and damaged wheel treads following locking of a wagon brake mechanism.
Inadequate maintenance processes can also result in deterioration of suspension components, leading to an increased likelihood of derailment. This was a factor in the derailments at Heworth in 2014 (report 16/2015) and at Washwood Heath in 2015 (report 01/2016), in which maintenance interventions had not kept up with the wear of components.
At Ely West Junction in 2017 (report 09/2018), our investigation of a derailment found that the wagon maintenance processes were not compatible with the design intent of the suspension system, and did not take account of future wear before the next intervention. These are failures in basic engineering management, which highlight the need for the entities in charge of maintenance (a legally defined role on the GB rail network) to properly define maintenance requirements.
Freight vehicles are fitted with manual parking brakes, commonly known as hand brakes, which must be released before a train begins its journey. If this is not done, one or more sets of wheels will not rotate, leading to flats being worn on the tread of the wheel. The consequence of this can be track damage and/or derailment when the affected wheels reach pointwork. RAIB recommended better arrangements for checking that all wheels are rotating properly as trains depart in two of its earliest investigations (report 08/2006 and report 27/2006), but we continue to see reports from the industry which indicate that the problem is still occurring. At Dunkeld & Birnam in 2018 (safety digest 01/2019), a railhead treatment train derailed and rerailed, causing significant track damage. Our investigation found that the handbrake interlock on the wagon concerned had been isolated at some time before the derailment, and that the wheelset which derailed had run for a long distance sliding rather than rotating, leading to substantial damage to its surface.
In our investigation of a derailment at Willesden High Level Junction in 2019 (report 07/2020), we found that the suspension adjustment arrangement was susceptible to introducing a diagonal wheel load imbalance, and routine maintenance had not detected that it was present.
3.3 Uneven loading
If the payload carried by a wagon, such as bulk material or discrete items, is not centred both laterally and longitudinally, there will be uneven distribution of weight through the wheels of the wagon. The resulting unequal forces between wheel and rail can lead to some wheels becoming sufficiently unloaded to the degree that, on curves, they can climb up and over the head of the rail, resulting in derailment of the vehicle. If an unevenly loaded wagon encounters track with a twist fault, conditions for derailment may be set up.
While liquids will find their own level, bulk loads of sand, aggregate or stone may not settle and can remain offset. It is important that loading is done in a way that ensures as far as possible that the load is evenly distributed and centred. Following a derailment at Angerstein Junction in 2014 (report 11/2015), RAIB’s investigation found that a mineral load (crushed rock fines) had adhered to the interior of a wagon (from which the load was supposed to have been discharged) in a way that created significantly uneven wheel loads. Heavy, discrete items, such as electrical machines, may be presented for rail transport loaded in sealed containers, and so it is equally important that the position of the centre of gravity of the load is considered when the container is being packed. In our investigation of a derailment at Reading West Junction in 2012 (report 02/2013), we found that pallets loaded with automotive components, which had been placed along the centre line of a container, had moved to one side while the container was being transported by road, resulting in a significant lateral offset to the load when the container was placed on a rail wagon. We recommended that freight terminal operators should improve their arrangements for both reducing the likelihood that inadequately packed containers are presented for rail transport, and for detecting asymmetric loads when containers are being handled before loading.
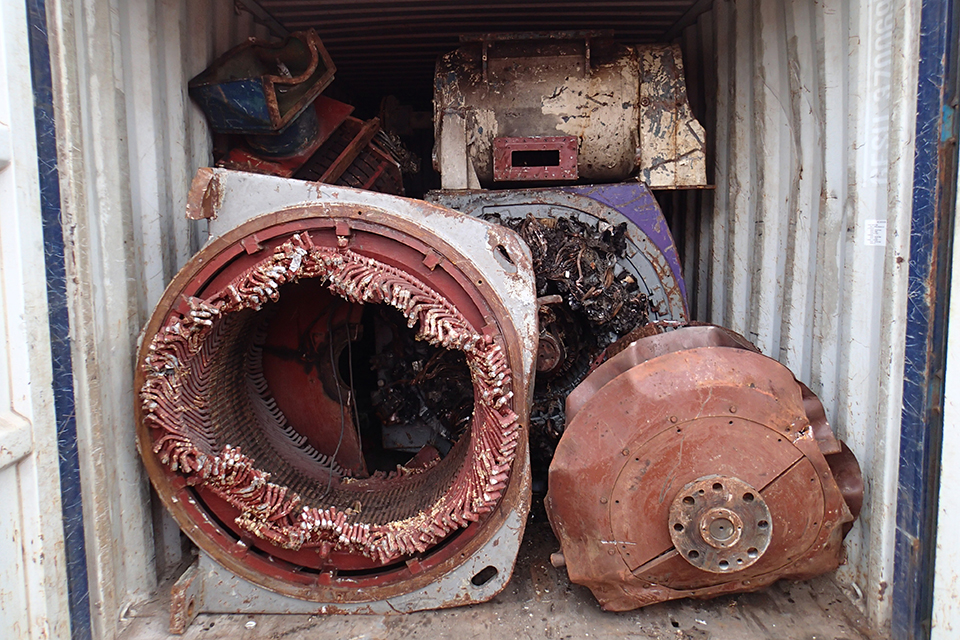
An example of asymmetric loading of heavy scrap electrical machinery.
RAIB’s investigation of the derailment near Camden Road in 2013 (report 21/2014) also found that the effects of asymmetric loading on the resistance of some types of wagon to derailment on twisted track had not been considered as part of the process for accepting the wagons for operation on the national network. We continue to believe that there is more to be done to address the risk of asymmetric loading.
3.4 Track condition
The geometry of the track, in terms of its vertical alignment (‘top’), horizontal alignment (‘line’), the change in relative height of the two rails (‘twist’), and the distance between the rails (‘gauge’), must be maintained to suitable standards to prevent derailments. Other factors, including rail wear and railhead condition, can also be among the causes of accidents. Many RAIB investigations have identified deficiencies in maintenance which have led to derailments, either on their own or in combination with vehicle defects.
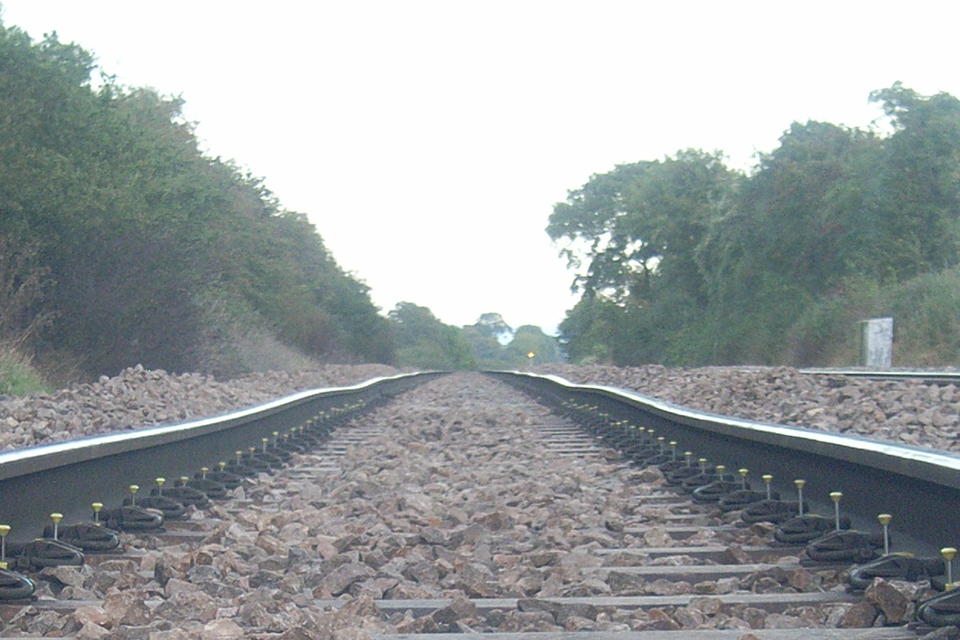
An example of poor track geometry which resulted in derailment of a freight train.
Measurement and monitoring of track condition, as well as inspection of the track itself, are increasingly carried out using digital systems. This has provided large amounts of data, which can be both difficult for maintenance staff to interpret and make it hard for teams to manage such quantities of reported faults. The correct response to track geometry measurements which indicate that faults are developing is crucial to the continued safety of the track. At Willesden High Level Junction in 2019 (report 07/2020) we found that the poor condition of the earth embankment supporting the track had led to a rapid deterioration in track geometry. At Wanstead Park in 2020 (report 12/2020), the longitudinal timbers supporting the track on a bridge had severely deteriorated because of rot, and this too had not been detected by the maintenance regime. Previous investigations have found examples, such as in the 2013 derailment at Gloucester (report 20/2014), of ineffective remedial work which has failed to cure faults, and a failure to impose speed restrictions which would have reduced the risk of freight vehicle derailments.
A factor in two recent investigations was the failure of rail fastenings under the weight of heavy freight trains on tight radius curves (Eastleigh, report 02/2021, and Sheffield, report 07/2021). The failure of rail fastenings can be very difficult to detect since the point of failure is often hidden from view. Once a fastening ‘loses its grip on the rail’, adjacent fastenings are subjected to higher forces and may well also fail. This progressive failure of fastenings can lead to gauge widening and, ultimately, derailment. RAIB has recommended that Network Rail reviews its measures for detecting excessive gauge widening under the weight of trains and improves its risk assessment processes.
4. Rail industry’s strategic safety groups
Relevant rail industry groups working in this field include the Cross-Industry Freight Train Derailment Prevention Working Group, which focuses on reducing the risks of freight derailment due to combinations of dynamic track faults, wagon faults, and offset loads. It reports to the National Freight Safety Group (NFSG), and details of how it is working to improve safety can be found in the RSSB Annual Health and Safety Report 2022.
RAIB is encouraged to learn that the NFSG is already working to better understand the risk posed by defective wagons, and to identify any additional control measures that may be needed to protect people, property and the environment.
5. Relevant RAIB publications
- Derailment at Hatherley, 18 October 2005 (report 08/2006)
- Broken Rails at Urchfont and Kennington, 5 January 2006 (report 27/2006)
- Derailment at Washwood Heath, 8 September 2006 (report 39/2007)
- Derailment at Ely Dock Junction, 22 June 2007 (report 02/2009)
- Derailment at Reading West Junction, 28 January 2012 (report 02/2013)
- Derailment near Gloucester, 15 October 2013 (report 20/2014)
- Derailment between Primrose Hill and Camden Road, 15 October 2013 (report 21/2014)
- Derailment at Porthkerry, 2 October 2014 (report 10/2015)
- Derailment at Angerstein Junction, 2 April 2014 (report 11/2015)
- Derailment at Heworth, 23 October 2014 (report 16/2015)
- Derailment at Washwood Heath West Junction, 23 March 2015 (report 01/2016)
- Derailment at Angerstein Junction, 3 June 2015 (report 10/2016)
- Derailment near Langworth, 30 June 2015 (report 11/2016)
- Derailment at East Somerset Junction, 20 March 2017 (report 19/2017)
- Derailment at Lewisham, 24 January 2017 (report 04/2018)
- Derailment at Ely West Junction, 14 August 2017 (report 09/2018)
- Track damage between Ferryside and Llangennech, 30 October 2017 (report 17/2018)
- Derailment near Dunkeld & Birnam, 29 October 2018 (safety digest 01/2019)
- Derailment at Carpenters Road North Junction, 11 June 2019 (safety digest 07/2019)
- Derailment at Willesden High Level Junction, 6 May 2019 (report 07/2020)
- Derailment near Wanstead Park, 23 January 2020 (report 12/2020)
- Derailment at Eastleigh, 28 January 2020 (report 02/2021)
- Derailment at Sheffield, 11 November 2020 (report 07/2021)
- Derailment at Morlais Junction, near Llangennech, 26 August 2020 (report 01/2022)