Minimum requirements for self-monitoring of flow: MCERTS performance standard
Updated 24 July 2022
Applies to England and Wales
The Environment Agency set up the monitoring certification scheme (MCERTS) to provide guidance on the standards you must meet to monitor emissions that affect the environment.
This standard applies if you have a permit under the Environmental Permitting Regulations (EPR) and that permit says you must:
- monitor liquid flow (for example, sewage or trade effluent)
- collect and record the results of your monitoring
This standard specifies the minimum requirements for self-monitoring of flow where operators have installed meters to conform to the Environment Agency’s permit requirements.
Natural Resources Wales permits may also specify that flow monitoring systems are certified against this standard.
An operator can request that this standard is applied to other flow measurement systems.
The standard covers requirements for the:
- performance of flow-metering installations – in terms of a target measurement uncertainty (section 3)
- management system – to make sure flow metering installations continue to meet performance requirements (section 4)
For the purposes of this standard, a flowmeter is an instrument which either:
- measures the flow-rate, or totalised volume, of fluid passing along a pipe or channel
- calculates these quantities from measurements of 1 or more properties which have a defined relationship with the flow-rate
1. Installations this standard applies to
1.1. This standard currently applies to flow meters installed on sites with permits issued under EPR, including:
- industrial sites previously regulated under the pollution prevention and control regulations
- water utility sewage treatment works previously regulated under the Water Resources Act 1991
- other sites with permits transferred to EPR, if the flow monitoring arrangements are significantly changed
- new installations with permits issued under EPR
It also applies to flow meters installed on sites:
- falling under the Urban Wastewater Treatment Directive (91/271/EEC and 98/15/EEC)
- with permits issued under the radioactive substance regulations
- which require MCERTS certified measurement systems
1.2. This standard can also apply to flowmeters on sites where the operator has a permit condition that states they must measure absolute quantities of controlled substances (such as heavy metals or radioactivity) and must have appropriate flow monitoring.
1.3. This standard has prescriptive elements primarily based on British and international standards, supported by the professional judgement used by MCERTS inspectors during their inspection of the flow-monitoring arrangements.
1.4. Conformance with this MCERTS standard is based on assessment of both the:
- flow monitoring arrangements by MCERTS inspectors
- supporting management system by MCERTS management system auditors
MCERTS inspection certificates are issued to operators (permit holders regulated under EPR) following satisfactory assessment against this standard.
2. How this MCERTS standard operates
CSA (CSA Group Testing UK Limited) operates the scheme on behalf of the Environment Agency and Natural Resources Wales.
CSA appoint MCERTS inspectors after assessing them against the MCERTS standard MCERTS: competency standard for MCERTS inspectors and assistant inspectors – effluent flow monitoring.
The MCERTS inspectors use this standard (Minimum requirements for self-monitoring of flow: MCERTS performance standard) to assess flow monitoring arrangements.
MCERTS management system auditors carry out an assessment of the management system for an operator’s flow monitoring arrangements, also against this standard.
Management system auditors shall work on behalf of a certification body that is accredited by UKAS, or by an accreditation body that is a signatory of the International Accreditation Forum multilateral recognition agreement. Certification bodies should have Minimum requirements for self-monitoring of flow: MCERTS performance standard – Management system (section 4) – included in their schedule of accreditation.
You can find contact details for MCERTS inspectors on the CSA website and also bulletins with additional procedures and guidance.
2.1. Site inspection and management system audit
Here is the process for a site inspection and management system audit.
2.1.1. The operator chooses an MCERTS inspector from the list of service providers on the CSA website.
2.1.2. The MCERTS inspector inspects the on-site process configuration and flow monitoring arrangements and prepares an inspection report. The MCERTS inspector gives the operator a copy of the inspection report.
2.1.3. The MCERTS inspector shall use on-site and other evidence to make sure that the flow monitoring installation is being satisfactorily maintained. Installations with, for example, restricted access shall have specific maintenance procedures detailing how maintenance can be carried out. CSA cannot issue an MCERTS inspection certificate unless there is evidence that the installation is being maintained.
2.1.4. The MCERTS management system auditor assesses the management system requirements relating to flow monitoring and produces an audit report.
2.2. Applying for certification
2.2.1. If the MCERTS requirements are met, the operator can apply to CSA for an MCERTS inspection certificate. The MCERTS inspector can apply on behalf of the operator.
2.2.2. The application must include the MCERTS inspection report, the MCERTS management system audit report and the appropriate fee.
2.3. Review and certificate issue
2.3.1. CSA reviews the evidence included in the application. Provided the MCERTS requirements are met, CSA issues an MCERTS inspection certificate to the operator. MCERTS inspection certificates are valid for 5 years from the date of the initial site inspection.
2.3.2. The MCERTS certificate may be withdrawn or suspended where payment is not fulfilled (under the contract terms) for the:
- MCERTS inspection report
- MCERTS management audit report
- certificate (refer to clause 2.2.2.)
2.4. Management system surveillance and reassessment
2.4.1. To maintain certification throughout the certification period, the operator’s management system shall be subjected to periodic surveillance. The first surveillance visit will be conducted approximately 12 months after the initial assessment. The frequency of subsequent surveillance will be agreed with the operator, based on the audit findings. The management system is re-assessed every 5 years.
2.5. Flowmeter installations that fail requirements
2.5.1. If a flowmeter installation fails to meet the MCERTS requirements, operators shall carry out remedial work. The MCERTS inspector shall provide guidance on the remedial work needed.
2.5.2. When the remedial work has been done, the MCERTS inspector will re-inspect to confirm the flowmeter installation now conforms with MCERTS requirements.
2.5.3. If the MCERTS requirements have been met, the MCERTS inspector provides the operator with an MCERTS inspection report confirming that the flowmeter installation meets the MCERTS requirements.
2.5.4. The operator can then apply to CSA for an MCERTS inspection certificate.
2.6. Management systems that fail requirements
2.6.1. If the MCERTS management system auditor identifies significant deficiencies in the operator’s management system, they will record and present these to the operator during the audit. The operator will be given an opportunity to address the deficiencies and provide evidence of corrective action. Further audits may be required to collect evidence that the deficiencies have been resolved.
2.6.2. If the MCERTS management system requirements have been met, the auditor provides the operator with a report confirming their management system now meets the MCERTS requirements.
2.6.3. The operator can then apply to CSA for an MCERTS inspection certificate.
2.7. Dispensations
2.7.1. A flowmeter installation may fail to comply with MCERTS requirements in a relatively minor way but the cost to immediately address this can be high. In these exceptional cases an operator can request a dispensation agreement
2.7.2. A request for a dispensation agreement should be sent to the regulator with the following information:
- a copy of the MCERTS inspection report, which shall state why the flowmeter installation does not meet the MCERTS requirements and suggest the remedial work needed
- a business case with a cost benefit analysis for the recommended remedial work, or any alternative improvements, with a proposed timetable for the work
- other relevant information to support the application
- additional information requested by the regulator
The regulator will review the information provided and will consider the following:
- the technical justification
- the impact on the permit requirements and local environment
- other relevant information
2.7.3. The regulator may need to discuss the matter with the MCERTS inspector to clarify any points before making a decision.
2.7.4. The regulator and the site operator will discuss the options, including plans for remedial work to agree an appropriate timetable for completion.
2.7.5. If the regulator agrees with the request, the operator then applies to CSA. Their application shall include:
- the most recent MCERTS inspection report
- evidence that the regulator has agreed a dispensation
- a timetable for any remedial work
- evidence that they have met the MCERTS management system requirements
- the associated fee
2.7.6. When they receive the application, CSA will review the evidence submitted and confirm the dispensation agreement with the regulator. They will then issue an MCERTS dispensation certificate valid for the agreed timetable. This will be for up to a maximum of 5 years from the date of the site inspection. The certificate will refer to the dispensation agreement.
2.7.7. If the regulator grants a dispensation, the operator must still maintain a management system (section 4.2). The management system shall be subject to periodic surveillance.
2.7.8. Dispensation agreements are not a permanent provision and it is expected that operators will resolve the problem as soon as reasonably practicable. If a dispensation certificate needs to be extended, the operator shall provide an explanation and justification as to why it has not been resolved in the preceding 5 years. Normally, only one extension of a dispensation will be allowed.
2.8. Recertification
2.8.1. An MCERTS inspection certificate is valid for 5 years. Flowmeter installations shall undergo recertification within 5 years of the previous MCERTS certification. The flowmeter installation should meet the MCERTS requirements before the expiry of the current certificate, which includes a reassessment of the management system.
2.8.2. A flowmeter installation can be re-inspected up to 12 months in advance of the MCERTS inspection certificate renewal date. If it passes the re-inspection, then a new certificate can be issued to run for 5 years from the expiry of the old certificate.
2.8.3. If the flowmeter installation fails the re-inspection, remedial work shall be carried out as soon as is practicable. A further inspection by the MCERTS inspector is required to confirm that it meets the MCERTS requirements.
2.8.4. If there are any changes to the flow monitoring arrangements that may affect the measurement uncertainty, then recertification shall be required as soon as is practicable.
3. Flow monitoring installations
The regulator may include conditions in a permit requiring the operator to:
- measure discharged volume or flow-rate (or both)
- record flow data and make returns as specified in their permit or the regulator’s flow policy
The regulator allows operators to select the flow measurement system they believe best suits their operations. Any new or replacement flowmeters, fitted after April 2010, shall hold suitable product certification under the MCERTS standard Performance standards and test procedures for continuous water monitoring equipment – part 3. An exception can only be made if there is no suitable MCERTS certified product available for the specific installation and the regulator agrees this in writing. See a list of MCERTS certified products.
The operator can carry out flow measurement at any location that is appropriate to measure the required flow.
3.1. Performance requirements for effluent flow monitoring (volume)
3.1.1. For effluent flow monitoring, the total daily volume of the discharge specified in the permit shall be measured with a target uncertainty of ±8% (or better) at a confidence level of 95%, calculated as detailed in section 5.
3.1.2. The location of the flow-monitoring installation shall ensure representative measurement of the total flow.
3.1.3. For those sites that treat all incoming flows, rather than divert high flows to storm overflows, and have a dry weather flow (DWF) limit in their permit, the regulator will accept up to 9 x DWF as the monitoring limit.
3.1.4. Some permits specify more than one location for discharges from a site with specific limits and monitoring requirements for each location. Therefore, flow measurement will often be required for each separate process operated on the site. For example, a power station may have a large cooling water discharge and a smaller discharge for an effluent treatment plant. Where flow monitoring requirements are specified in the permit for each of these discharges, they will be measured separately and will be inspected separately. The discharge points will be listed on the inspection certificate.
3.1.5. The MCERTS inspection report shall include details of all the discharge flow monitoring arrangements on site where these are included in the permit. The inspector shall confirm the flowmeter suitability as described in section 3.4.
3.1.6. Each discharge included in the permit shall meet the ±8% target uncertainty.
The target uncertainty of ±8% therefore applies to each emission point and not to the sum of all the emission points.
3.1.7. Where the flow from a single discharge is measured by combining the readings from more than one flowmeter, all the relevant flowmeters shall be inspected and their individual uncertainties combined to obtain the uncertainty for the discharge measurement.
3.2. Performance requirements for instantaneous flow monitoring
3.2.1. Instantaneous flow refers to a flow-rate measurement which may be either:
- a spot reading
- an average rate of flow over a period of 15 minutes or less
This will depend on site-specific requirements.
3.2.2. Where the regulator includes conditions in a permit requiring the operator to measure instantaneous flow, for example flow passed forward (FPF), flow to full treatment (FFT), or the pass forward flow at a pumping station, the operator shall measure the flow with a target uncertainty of ±8% (or better) at the flow-rate specified in the permit.
3.2.3. If the operator’s permit conditions state they must measure the instantaneous flow of an intermittent discharge, they shall measure the flow to a target uncertainty of ±8% (or better) at 25% of the design flow-rate. They shall agree the design flow-rate with the regulator.
3.2.4. If the operator’s permit conditions state they must measure the instantaneous flow through a disinfection process, for the purpose of controlling the disinfecting dose, they shall measure the flow to a target uncertainty of ±8% (or better) at 25% of the design flow-rate. They shall agree the design flow-rate with the regulator.
Any exception to these requirements will be confirmed in writing by the regulator.
3.2.5 The MCERTS inspection report shall include details of all the instantaneous flow monitoring arrangements on site where these are included in the permit. The inspector shall confirm the flowmeter suitability as described in section 3.4.
3.3. The role of MCERTS inspectors and assistant inspectors
3.3.1. An MCERTS inspector is a technical specialist who can demonstrate considerable experience and expertise in assessing flow monitoring arrangements. An important part of their role is to exercise professional judgement.
An MCERTS inspector is able to assess the potential effects of deviations in flow monitoring arrangements and estimate these as part of an uncertainty calculation. An MCERTS inspector can work in isolation or may supervise the work of others.
3.3.2. Section 3 of the Competency Standard for MCERTS Inspectors and Assistant Inspectors – effluent flow monitoring specifies:
- the competency requirements for MCERTS inspectors and assistant inspectors
- the duties that they may perform
- a code of conduct
3.3.3. An assistant inspector has specific technical expertise, primarily in obtaining dimensional measurements of flow monitoring structures, or site process configuration, or both. They will have the necessary competence to carry out these measurements unsupervised. Data and information recorded by an assistant inspector must be quality checked and controlled by an MCERTS inspector. The MCERTS inspector must apply any further professional judgement needed.
3.3.4. It is not acceptable for an MCERTS inspector to simply conduct a desk review of an inspection carried out by an assistant inspector. The MCERTS inspector must visit the site.
3.3.5. An MCERTS inspector must accompany and supervise individuals, for example MCERTS trainees, not appointed as MCERTS inspectors or assistant inspectors.
3.4. Conformance assessment
3.4.1. The MCERTS inspector shall establish that the selection, installation and operation of the primary and secondary device (for example, flume or weir, plus level measuring devices) are fit for purpose.
3.4.2. If the flowmeters hold product certification class 1, 2 or 3, under the MCERTS standard Performance standards and test procedures for continuous water monitoring equipment – part 3 they shall be regarded as fit for purpose.
If the flowmeters hold product certification class 4 the inspector shall check and confirm that they are suitable for use at the location. The requirements of this MCERTS standard shall still apply to their installation and ongoing operation.
3.4.3. The MCERTS inspector shall assess conformance by using recognised standards with additional information in this document and by using their professional judgement.
Section 6 provides guidance on ‘concessions’ from international standards for open channel flow structures.
Section 7 provides guidance and requirements when using air firing ultrasonic level sensors.
Section 8 provides guidance on the uncertainties that can be found on installations using electromagnetic flowmeters.
Section 9 provides guidance and requirements for using area-velocity flowmeters.
The MCERTS inspector shall provide written justification if, in their opinion, target uncertainty will still be achieved despite exceeding the concessions outlined in section 6.
3.4.4. The MCERTS inspector shall assess the suitability of the flow monitoring installation by site inspection and examination of flow diagrams. The MCERTS inspector shall make sure that any flow diagrams provided are representative and accurate. The inspection shall include a full walking audit of the site to establish the process routes for all relevant inflows, overflows, re-circulation and process returns.
3.4.5. The MCERTS inspector shall assess the location of the measurement structure and the impact of hydraulic influences both upstream and downstream to cover the full range of flow conditions.
3.4.6. The MCERTS inspector shall confirm whether maintenance arrangements are adequate. They shall record any evidence of inadequate maintenance in the inspection report for further investigation during the management system assessment. An MCERTS inspection certificate cannot be issued unless there is evidence that the installation is being satisfactorily maintained.
3.4.7. The MCERTS inspector shall carry out calibration and set up checks on the measuring instruments. These checks shall record the set up programme of the measurement instrument to include, for example, the:
- zero set up
- calibration reference plate setting
- calculation method
- programmed dimensions
- range
3.4.8. The MCERTS inspector shall confirm that any local display agrees with the flowmeter output.
3.4.9. The MCERTS inspector shall, where possible confirm any telemetry systems are operating as expected. They can do this by contacting the appropriate control room or data team and comparing the reported value to the local measurement. This might not be possible at some locations because of poor phone coverage.
3.4.10. The MCERTS inspector shall record whether the flow measurement installation conforms with the requirements of this standard. They shall use the information gathered during the inspection to assess the suitability and uncertainty of the flow measurement installation. They will include this information in the inspection report which is then forwarded to CSA.
3.4.11. The inspection report shall include a flow uncertainty table or curve (or both) which provides the relationship between flow and uncertainty over the operational range of the flowmeter. For sites monitoring effluent flow this is used, together with dry weather flow data, to calculate the uncertainty in total daily volume (as detailed in section 5).
An estimate of measurement uncertainty at specific flow-rates can also be derived from the flow uncertainty table or curve (or both), when required.
3.4.12. CSA will only issue an MCERTS inspection certificate if all the relevant requirements of the MCERTS standard have been met. The date on the MCERTS inspection certificate shall be the date on which the flow monitoring arrangements were inspected.
4. Management system
Figure 1 shows a schematic of a typical open channel flow measurement system including connections to send data remotely to a central location. It indicates the division of responsibility for assessment of the 2 key areas:
- site process configuration and flow measurement system
- management system
The site assessment looks at the site process configuration, primary device, secondary device and telemetry functionality. The audit of the operator’s management system assesses data acquisition and telemetry.
Figure 1: schematic of a flow measurement system
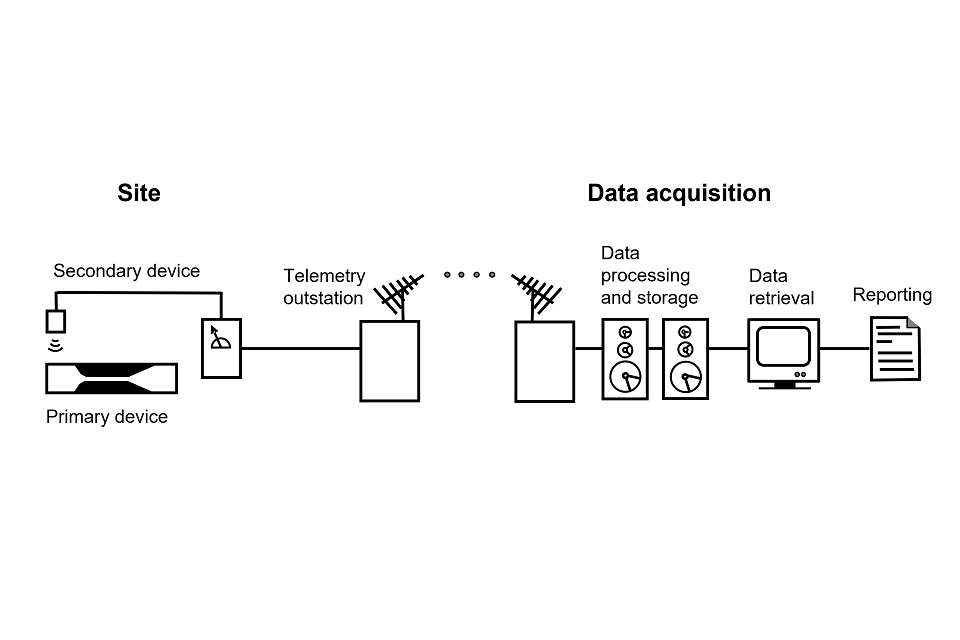
4.1. Establish and maintain a management system
The operator shall establish and maintain a management system for their flow monitoring arrangements to make sure that, at all times, they meet the performance requirements specified in section 3.2. Detailed guidance covering each of the management system requirements is available from the CSA website.
4.2. Contents of the management System
4.2.1. The management system shall include statements, information and documentation, as appropriate, covering:
- quality and environmental policy – section 4.4
- management responsibilities – section 4.5
- documentation – section 4.6
- operating procedures – section 4.7
- document control – section 4.8
- equipment inventory – section 4.9
- maintenance – section 4.10
- commissioning – section 4.11
- site changes – section 4.12
- verification – section 4.13
- data treatment – section 4.14
- corrective actions – section 4.15
- internal audit section – 4.16.
4.3. Possible extension of MCERTS
4.3.1. In the future this MCERTS standard may be extended and a simplified management system may be considered.
4.4. Quality and environmental policy
4.4.1. The operator shall establish and maintain a documented quality and environmental policy. The policy shall be issued under the authority of top management. A policy statement that complies with the requirements of ISO 14001 that includes a commitment to comply with applicable legal requirements, shall be considered to meet this requirement.
4.4.2. Those responsible for MCERTS related operations shall be made aware of the policy.
4.5. Management responsibilities
4.5.1. The operator shall make sure that they define responsibilities and authorities for MCERTS and communicate this to all relevant personnel. Designated personnel, irrespective of other responsibilities, shall have responsibility and authority for:
- making sure they establish, implement and maintain MCERTS management system procedures
- reporting to top management, and liaising with CSA and the regulator, on the performance of the flow-monitoring arrangements, including the management system and the need for any improvements
- making sure the requirements of the management system in relation to meeting the performance targets are communicated and understood
4.5.2. The operator shall make sure that those with MCERTS responsibilities receive appropriate training, are competent, and shall keep appropriate records and documentation of this. Internal training and self-study may be acceptable but shall still require detailed records of training received.
4.5.3. The operator shall maintain organisational charts and job descriptions of staff involved in flow monitoring. Job descriptions shall include:
- job title
- description of duties
- responsibilities
- qualifications, training and experience requirements
4.6. Documentation
4.6.1. Management system documentation shall include the following:
- the quality and environmental policy
- an overview of the MCERTS management system and the flow monitoring arrangements
- operating procedures
4.6.2. The current version of this MCERTS standard shall be accessible to all relevant personnel.
4.7. Operating procedures
4.7.1. The operator shall establish and maintain procedures and instructions as required by this MCERTS standard. Operating procedures can be in any form or type of media. The level of detail should be no more than is required by the complexity of the organisation or the flow monitoring arrangements.
4.8. Document control
4.8.1. Authorising and maintaining management system documentation shall be the responsibility of designated competent personnel.
4.8.2. Controlled documentation shall not be amended without the authorisation of designated competent personnel or their appointed deputies.
4.9. Equipment inventory
4.9.1. The operator shall maintain a list of major items of equipment and the location of each. A major item of equipment is defined as an item that is critical to the validity of flow monitoring for example, the sensor and electronics.
4.9.2. The operator shall keep equipment records for each major item. The records shall contain details of the equipment, its unique identifying code and any relevant calibration and maintenance requirements.
4.10. Maintenance
4.10.1. The operator shall make sure that appropriate maintenance of the flow monitoring arrangements is carried out. Equipment shall be maintained and serviced at pre-defined intervals (for example, according to manufacturers’ instructions or operating procedures) and whenever a significant deterioration is noticed.
4.10.2. The frequency of scheduled maintenance activities, such as removal of fouling, shall be supported by documented observations. Up to date maintenance records shall be completed in a timely manner and kept where they can be accessed. These records shall include any problems encountered, for example due to adverse weather conditions.
4.11. Commissioning
4.11.1. The operator shall establish and maintain a procedure for commissioning replacement or modified flow monitoring systems (such as a new flowmeter or associated instrumentation) to make sure that they continue to conform to the requirements in section 3.2.
4.12. Site changes
4.12.1. The operator shall establish and maintain a procedure to document any changes that could affect flow monitoring (for example, changes to manufacturing or effluent handling processes) and that a competent person shall assess the risk of these changes influencing the performance of the flow monitoring equipment. The operator shall maintain records of such assessments. The competent person shall determine whether the MCERTS inspection certificate has been invalidated.
4.12.2. If the competent person’s assessment indicates that the MCERTS inspection certificate has been invalidated then an MCERTS inspector shall carry out an inspection as soon as practicable.
4.12.3. If the competent person’s assessment indicates that the MCERTS inspection certificate has not been invalidated, the operator shall document their justification. They shall make this justification available for examination by the MCERTS management system auditor at the next audit.
4.13. Verification
4.13.1. The operator shall undertake appropriate verification between MCERTS inspections over the entire certification period, to make sure that the flow monitoring equipment is operating satisfactorily.
4.13.2. Verification shall include at least one of the following methods:
- calibration (in a calibration laboratory)
- comparison with a secondary device, drop test or gravimetric calibration
- appropriate in-situ checks – such as reference plate for open channel flowmeters or level and velocity checks for area-velocity (AV) meters
4.13.3. Where the above methods are not possible, an alternative method is permitted. The operator shall agree, in writing, any alternative method with the MCERTS inspector. Section 8 includes further guidance on the verification of electromagnetic flowmeters.
4.14. Data treatment
4.14.1. Where applicable, the operator shall include procedures for data treatment in the management system. The operator’s management system shall define the maximum acceptable data treatment and telemetry error.
4.14.2. The management system auditor is not required to carry out data treatment and telemetry verification measurements, but is required to make sure that the:
- appropriate checks are specified in the operator’s operating procedures
- procedures are being implemented in a timely and appropriate manner
- results are being recorded and analysed
- results are included in the overall assessment of the total uncertainty
4.15. Corrective actions
4.15.1. If an operator has not complied with this MCERTS standard, or their operating procedures, a competent person shall instigate corrective action. A competent person, who may be different to the instigator, shall carry out corrective action in a timely manner. The action taken shall be proportional to the significance of the non compliance and shall include action to prevent recurrence. The operator shall maintain records of any non-compliance and the action taken.
4.16. Internal audits
4.16.1. Internal audits shall be performed according to a defined schedule to verify that operations continue to comply with the requirements of the management system and with the current version of this MCERTS standard. It is the responsibility of the designated competent person to plan and organise such audits. They shall be carried out by trained personnel who are operationally independent of the activity to be audited. Personnel shall not audit their own activities, unless the operator can demonstrate that it will be effective.
4.16.2. The operator shall keep a record of the audit findings and any corrective actions arising from them. The operator shall ensure that they implement corrective action in a timely manner.
4.17. Conformance assessment – management system
4.17.1. The certification body conducting the management system audit shall be a UKAS accredited certification body, or one accredited by an accreditation body that is a signatory of the International Accreditation Forum multilateral recognition agreement. Certification bodies should have Minimum requirements for self-monitoring of flow: MCERTS performance standard – Management system (section 4) – included in their scope of accreditation. The management system auditor shall work on behalf of an accredited certification body.
4.17.2. The management system auditor shall assess the operator’s management system to ensure that the requirements of sections 4.4 to 4.16 have been met in relation to the flow monitoring arrangements.
5. Estimating uncertainty
This section explains how to estimate the uncertainty:
- of the total daily volume for effluent flow monitoring
- for instantaneous flow monitoring
- for pumped or batch flows
5.1. Estimating uncertainty of the total daily volume for effluent flow monitoring
5.1.1. MCERTS requires that, for effluent flow monitoring, the total daily volume shall be measured with a target uncertainty of ±8% (or better) at a confidence level of 95%. This section gives a generic method for determining the uncertainty of total daily volume from the meter uncertainty curve and a set of representative flow data for a typical day’s discharge.
5.1.2. For wastewater treatment plants the typical representative day shall be a ‘dry’ day. For an industrial site, it shall represent a day when the plant is functioning within its normal operating capacity.
5.1.3. If the permit holder cannot provide flow data for these conditions (for example, if it is a new site) the MCERTS inspector may apply a diurnal flow pattern considered to be appropriate for the size of the plant and nature of the process.
The calculation shall be carried out as follows.
5.1.4. Use a flow weighted average that takes account of the diurnal flow pattern at the site to calculate the uncertainty for total daily volume.
5.1.5. Use the flow uncertainty curve that is the specific relationship between flow-rate and uncertainty for the metering system derived by the MCERTS inspector as a result of the site inspection.
5.1.6. The site flow data shall normally comprise a series of 96, 15-minute values for a typical day’s discharge; each value being the average flow-rate over a 15-minute period. In some cases the 15-minute values may represent the volume recorded in each period. If this is the case, you must convert the volume to a flow-rate by dividing by the time.
5.1.7. Calculate the total daily volume by adding the 96,15-minute volume values over the day (multiply flow-rate values by time to obtain the volume).
5.1.8. Determine the uncertainty for each average flow-rate value from the flow uncertainty curve, interpolating between points where appropriate.
5.1.9. Calculate the contribution to the total uncertainty for each value by multiplying the uncertainty at that value by the volume for the period, divided by the total daily volume.
5.1.10. Calculate the uncertainty of the total daily volume by adding the contributions over the day.
Worked example
5.1.11. A flume is used to measure the discharge from a works. The flow uncertainty curve derived from the site inspection is shown in figure 2.
Figure 2: flow uncertainty curve
5.1.12. The diurnal profile of flows from the works is shown by the solid line in figure 3. The 15-minute average flow-rates are shown by the blocks.
Figure 3: diurnal flow data
5.1.13. Table 1 shows the calculation of uncertainty for the 4 values circled in figure 3 only.
The first 2 columns show the site data provided. The uncertainty (uᵢ) at each flow-rate (qᵢ) was obtained from the curve in figure 2. The volume in each 15-minute period was calculated by multiplying the flow-rate in litres per second by 900 seconds and converting to cubic metres. These volumes were added over the day to give the total daily volume, in this case 1,000 m3 as shown at the foot of the table.
The contribution of each reading to the total daily uncertainty was calculated by multiplying the uncertainty at that point (uᵢ) by the 15-minute volume (vᵢ) and dividing by the total daily volume. These contributions were added over the day to obtain the uncertainty in total daily volume, in this case 6.49%. as shown at the foot of the table.
Table 1: example calculations
Time (from site flow data) | Average flow-rate (qᵢ) in litres/second (from site flow data) | % uncertainty at qᵢ (uᵢ) (from flow uncertainty curve) | Calculated volume in 15-minute period (vᵢ) m³ | Calculated % contribution to uncertainty (uᵢ x vᵢ / Ʃvᵢ) |
---|---|---|---|---|
06:15 | 5.64 | 10.75 | 5.08 | 0.0546 |
06:30 | 6.79 | 8.64 | 6.11 | 0.0528 |
06:45 | 8.17 | 8.07 | 7.36 | 0.0593 |
07:00 | 10.82 | 6.85 | 9.74 | 0.0667 |
Total daily volume = 1,000 | Total daily U = 6.49% |
5.2. Estimating uncertainty for instantaneous flow monitoring
5.2.1. If the operator has permit conditions requiring them to measure instantaneous flow (for example, flow passed forward or flow to full treatment), they shall measure the flow with a target uncertainty specified in section 3.2.
5.2.2. Determine the uncertainty for instantaneous flow monitoring from the flow uncertainty curve, interpolating between points where appropriate.
5.3. Estimating uncertainty for pumped or batch flows
5.3.1. Care should be taken when using flow data from pumped flows or batch processes.
Where flows have been averaged over a period that includes a pump or batch start stop, the average flow-rate may not reflect the actual flow-rate. This could lead to an incorrect estimation of uncertainty. This is illustrated in figures 4 and 5, and in Table 2: meter uncertainty based on average flow-rate.
In Table 2, the average flow-rates for each of the 15-minute periods shown in figure 4 have been calculated and the corresponding meter uncertainty read from the flow uncertainty curve in figure 5. The contribution to uncertainty for each volume is calculated. The contributions are summed and divided by the total volume passed to determine the apparent uncertainty.
Figure 4: sample pumped flow data
Figure 5: flow uncertainty curve
Table 2: meter uncertainty based on average flow-rate
Period | Volume passed in period in litres | Average flow-rate in litres/second | Apparent % meter uncertainty from figure 5 | Contribution to total volume uncertainty in litres |
---|---|---|---|---|
1 | 3,000 | 3.33 | 9.7 | 291 |
2 | 2,000 | 2.22 | 10.8 | 216 |
3 | 1,000 | 1.11 | 15.0 | 150 |
4 | 6,000 | 6.67 | 6.0 | 360 |
Total 12,000 | Total 8.48% | Total 1,017 |
This apparent uncertainty is a significant over-estimate as the actual flow-rate during each pumping cycle was 1,000 litres per minute (16.67 litres per second) so the actual meter uncertainty should be 6%, before allowing for any other factors
As can be seen from this example, flow data based on average flow-rates may not enable the flow-rate during the pumping cycle to be immediately identified. The MCERTS inspector should therefore establish an estimate of the flow-rate during the pumping cycle, for example, by observing the flow-rate shown by either the:
- meter
- secondary measurement
- rate of drop in a wet well or reservoir
- pump capacity data
5.3.2. The MCERTS inspector should consider whether they should include an additional component of uncertainty for factors such as the ramp up and down periods where the pump or batch is starting and stopping. Measurement during this period may be affected by factors such as the response time of the flowmeter to these changes and the hydraulic conditions of the installation. For example, a closed pipe with an open discharge may take time to fill, during which time the measurement will have a high uncertainty.
6. Open channel flow measurement system concessions
6.1. The concessions allowed under MCERTS will mainly apply to existing hydraulic gauging structures for determining flow. It is expected that new hydraulic structures will be constructed to the best tolerances that current engineering practices allow and will remain stable enough to maintain their dimensions for a minimum of five years.
6.2. The concessions described in this section are ‘permissible’ deviations from international standards. They recognise that the limits and tolerances prescribed are largely unachievable in the field. These concessions are based on expert knowledge currently available. They have no formal basis, nor are their effects on flowmeter uncertainty fully understood. As such, we may adapt the concessions in the future to reflect any improved knowledge.
6.3. These concessions cover thin-plate weirs and long-throated critical depth flumes as they are the most common types of open channel primary devices used for discharge measurement.
6.4. The concessions must not be regarded as a prescriptive ‘tick sheet’. There may be situations where more than one characteristic is present in a hydraulic structure. It is up to the MCERTS inspector to use their professional judgement when considering whether the combined effect of these characteristics is likely to have an adverse effect on flow measurement. There may be occasions when the concessions are exceeded but it can be demonstrated that the installation can still achieve the target uncertainty.
6.5. All concession items shall be logged and recorded, and some provision may be needed in the uncertainty budget (see section 3.4 – Conformance assessment).
6.6. Ratios and limits defined in standards must be followed where practicable. The MCERTS inspector shall exercise professional judgement to consider whether going beyond these limits has an adverse effect on flowmeter performance.
6.7. In the case of weirs, it is permissible to install and use drawdown penstocks to facilitate weir chamber cleaning provided they are not detrimental to weir performance when they are not being used.
6.8. Baffles are considered an acceptable solution to stabilise poor flow conditions. These must be fitted in a way that does not adversely affect the flow profile and conditions throughout the primary device’s operational range. Perforated plate flow straighteners will not be suitable for some applications (such as effluent flow monitoring) due to their fouling potential. In all cases operators should take measures to make sure that any risk of pollution is mitigated.
Concessions for primary device: thin-plate weirs (BS ISO 1438)
These are BS ISO 1438 requirements and the concessions allowed by MCERTS.
Weir plate edge thickness
Requirements and concessions:
- BS ISO 1438 states 1 to 2mm
- there is no MCERTS concession
- there must be no evidence of weir edge erosions
Weir chamfer angle
Requirements and concessions:
- as per BS ISO 1438
- there is no MCERTS concession
- there must be free discharge throughout the range with full ventilation
Verticality of weir plate – degree of uprightness
Requirements and concessions:
- BS ISO 1438 states this must be vertical
- MCERTS concession is no more than ±5 degrees from the perpendicular
Weir plate deflection (amount of bow)
Requirements and concessions:
- BS ISO 1438 states this must be straight
- MCERTS concession is no more than ±2% of maximum weir notch opening or full width for a fully contracted weir plate
Deviation of weir plate normal to the flow (amount of skew)
Requirements and concessions:
- BS ISO 1438 states this must be square
- MCERTS concession is no more than ±2% of weir width (B)
Centrality of weir plate (amount of off-centre)
Requirements and concessions:
- BS ISO 1438 states this must be central
- non-central is acceptable under MCERTS provided effects of sidewalls are minimal
- the width of a weir plate fitted in a circular structure is taken as the chord length
Deviation of the weir plate in the horizontal plane (sideways level)
Requirements and concessions:
- BS ISO 1438 states this must be true and level
- MCERTS concession is no more than ±2% of weir width (B)
Approach channel level (in the direction of flow)
Requirements and concessions:
- BS ISO 1438 states this must be level
- MCERTS concession is no more than 2° slope from horizontal
- if p is large in proportion to the gauged head, then the channel approach is less critical – account may need to be made for accurate referencing
Concessions for primary device: long-throated, critical depth flumes (BS ISO 4359)
These are the BS ISO 4359 requirements and the concessions allowed by MCERTS.
Throat width variation (includes parallax error and non-uniform cross section)
BS ISO 4359 states:
- this must be no more than ±0.2% with an absolute maximum of 10mm
- minimum throat width (b) = 100mm
MCERTS concessions are:
- no more than ±1.5% up to and including throat width of 300mm
- no more than ±5mm for throat widths greater than 300mm
- a minimum throat width of 50mm is acceptable provided that site conditions are appropriate. An additional 1% uncertainty will be added for structures where b<100mm
These apply to the critical area being measured where at least 12 transverse measurements are made (most importantly in the wetted area of the throat).
Throat transverse level variation
Requirements and concessions:
- BS ISO 4359 states this must be an average of ±0.1% slope from horizontal
- MCERTS concession is no more than ±1%
These apply over the measured length.
Throat longitudinal level variation
- BS ISO 4359 states this must be an average slope of ± 0.1% slope from horizontal
- MCERTS concession is no more than ± 1%
Approach level variation
Requirements and concessions:
- BS ISO 4359 states this must be ±0.1% of L slope from horizontal
- MCERTS concession is no more than ±1% (for a distance 10 x hmax upstream)
Longitudinal level variation
Requirements and concessions:
- BS ISO 4359 states this must be ±0.1% of L slope from horizontal
- MCERTS concession is no more than ±1%
Channel width variation
The MCERTS concession is no more than ±5%
Centrality of flume (amount off-centre)
Requirements and concessions:
- BS ISO 4359 states this must be central
- MCERTS concession is no more than ±5% of approach channel width
Staggered flume cheeks
Requirements and concessions:
- BS ISO 4359 states this must be ±0.1% of L
- MCERTS concession is no more than ±1% of L
- cheeks can be staggered on both the upstream or downstream side or both
Vertical skew
Requirements and concessions:
- BS ISO 4359 states the deviation from the plane of other vertical or inclined surfaces is ±1%
- there is no MCERTS concession
Horizontal skew
Requirements and concessions:
- BS ISO 4359 states the allowed deviation from the plane of other vertical or inclined surfaces is ±1%
- there is no MCERTS concession
Curvature of entrance transition
Requirements and concessions:
- BS ISO 4359 states arc governed by R >= 2(B-b) with an allowed deviation of ±0.1% of L
- MCERTS concession is deviation up to ±5%
Roughness value (Ks)
Requirements and concessions:
- as per BS ISO 4359
- there is no MCERTS concession
This can be subjective. We suggest use a Ks value of 0.6mm for all GRP, plastic and stainless steel devices and a Ks value of 1.5mm for all concrete devices.
Concessions for secondary device
These are the international standards’ requirements and the concessions allowed by MCERTS.
Position of sensor
The international standards’ requirements are:
- 3-4 hmax for flumes
- 2-4 hmax for weirs
Part 4A of the now superseded BS3680, required the head measurement to be 4-5 hmax upstream of the weir. Existing flowmeter installations that comply with the previous standard will keep their certification but with a recommendation that the measurement point is moved when the installation is replaced (if practical to do so).
For MCERTS concessions, any relaxation allowed is at the discretion of the MCERTS inspector.
The point of measurement can be taken from the radial distance from the weir notch provided disturbances and other influences are avoided.
Method of determining flow
The international standards’ requirement is to use the head to flow equations in the standard.
The MCERTS concession allows operators to use look-up table provided the relationship is originally determined using the appropriate standard.
Errors using look-up tables should be included in the uncertainty assessment.
7. Installing and using air firing ultrasonic level sensors for open channel flow measurement
This section of the standard applies to flowmeters which comprise a single air firing ultrasonic level transducer linked to a flow computer. In these flowmeters, the distance between the transducer face and the liquid surface is measured and then converted to head or stage (the depth of fluid above a set datum) upstream of a primary device, such as a weir or flume, and then to volumetric flow-rate.
The flowmeter shall incorporate a way of compensating for changes in the speed of sound through air due to temperature variation.
Any new or replacement flowmeter, fitted after April 2010, shall hold product certification under the MCERTS standard: Performance Standards and Test Procedures for Continuous Water Monitoring Equipment – Part 3 over a certification range appropriate to the installation.
An on-site inspection by an MCERTS inspector shall confirm that the level sensor has been installed and set up correctly and that the effects of any external influences have been assessed.
7.1. Installation
7.1.1. The operator shall make sure the transducer is located at an appropriate distance upstream of the primary device, as defined by the relevant international standard or manufacturers instructions.
7.1.2. The fluid surface beneath the transducer shall be calm and free from foam, significant ripples, waves, vortices and swirl.
Where possible, avoid installing:
-
in enclosed spaces where a humid or gaseous atmosphere may build up between the fluid surface and the transducer which may affect the speed of sound
-
where the liquid is at an elevated temperature leading to a significant temperature gradient between the transducer and the fluid surface – a separate temperature probe shall be used in such situations
-
on batch discharges where the initial surge may be highly turbulent – dampers or baffles upstream of the measurement point may be used to reduce this turbulence
If it is not possible to avoid these situations, allowance shall be made for additional uncertainty in the measurement.
7.1.3. The transducer shall be mounted directly onto a rigid frame or supporting bracket. The supporting structure shall be free from vibration.
7.1.4. The operator shall not use swinging or hinged mounting arms unless they are necessary to facilitate maintenance. For example, this could be in deep chambers or wide channels where the transducer cannot be accessed from the side, or from a walkway over the channel or chamber. They will also need to make sure the support is positively relocated into the same position after use.
7.1.5. Where a swinging or hinged arm is used, the MCERTS inspector shall consider including an additional component of uncertainty in the uncertainty budget to account for the repeatability of repositioning.
7.1.6. On unmanned and remote locations, steps shall be taken to prevent tampering.
7.1.7. There shall be a clear path between the transducer face and the fluid surface.
7.1.8. The operator shall make sure the transducer is mounted perpendicular to and vertically above the fluid surface, with the transducer face parallel to the fluid surface.
7.1.9. The operator shall make sure they observe the manufacturer’s instructions regarding the tightness of the transducer mounting nut. Over tightening the nut can cause ‘ringing’ and the instrument will either not measure, or the measurement will be of poor quality.
7.1.10. The operator shall make sure the transducer face is located as close to the fluid surface at the maximum depth or flow as practicably possible, taking account of the instrument’s blanking distance. (The blanking distance is the minimum separation distance between the transducer face and the fluid surface required to obtain a measurement).
Ideally, the sensor face should be at a distance of: Maximum fluid depth + instrument blanking distance + safety distance above the chamber or channel floor. (The safety distance, typically 50 to 100mm, provides a safety margin to allow an alarm to be raised if the fluid depth exceeds its maximum in the case of flooding, channel blockage, backing-up, or other reasons.)
7.1.11. If the transducer is in an exposed location where it will be subject to direct solar radiation for a significant part of the day, particularly around mid-day when solar intensity is at its greatest, then the operator shall make sure the transducer is fitted with an effective sunshade.
7.1.12. Where a transducer is installed beneath a grille or grating it will be partially shaded by the grating. However, the extent of shading will depend on several factors including:
- mesh size
- thickness of the grating
- any shading provided by the chamber or channel walls
- distance of the transducer beneath the grating
- orientation of the channel or chamber and mesh with respect to the passage of the sun
In such cases, a sunshade shall be fitted unless an MCERTS inspector agrees that the transducer is effectively shaded.
7.1.13. A sunshade is not required where the transducer is installed beneath a solid, opaque cover.
7.1.14. If the instrument has a separate temperature sensor, it shall be located between the transducer face and the fluid surface, sufficiently offset from the ultrasonic path to avoid any interference with the measurement. Ideally this would be midway between the transducer and the fluid surface at maximum flow.
7.1.15. Where a separate temperature sensor is used, the operator shall make sure that both the ultrasonic transducer and the temperature sensor are shaded from direct sunlight, using the guidance outlined in 7.1.11 to 7.1.13.
The operator should make sure that a submergence shield is fitted if the transducer is installed below the walls of a channel or chamber that could flood and submerge the transducer.
7.1.16. The operator shall make sure that the transducer mounting is designed in a way that allows the level measurement to be calibrated or verified using a reference plate, point gauge or gauge board. (A reference plate, also known as a swing plate, comprises a flat surface that can be repeatably set at a fixed known distance from the transducer face, and above the primary device (flow) zero datum.)
7.1.17. The operator shall make sure that the zero datum for the flow measurement is set appropriately for the primary device, as defined in the relevant international standard or manufacturer’s instructions. This may be different from the instrument datum used for the level measurement. If so, an offset will need to be programmed into the instrument to take account of any difference. It is not sufficient to rely on an empty chamber or channel as the floor may not be level.
7.1.18. The primary structure (flow) zero datum, the instrument datum and any reference plate value shall all be set relative to a fixed point by survey levelling.
7.1.19. Where batch discharges are likely to be of short duration, a rapid response time shall be required from the instrument to make sure the discharge is measured accurately.
7.2. Maintenance and verification
7.2.1. The flowmeter shall be maintained and calibrated in accordance with the manufacturer’s recommendations.
7.2.2. A way of verifying the level measurement, such as a reference plate, point gauge or gauge board, shall be available and used.
7.2.3. Where a reference plate is used, the surface shall be level, clean and dry when a verification measurement is taken.
A reference plate, also known as a swing plate, comprises a flat surface that can be repeatably set at a fixed known distance from the transducer face and above the primary device (flow) zero datum.
7.2.4. The transducer, temperature sensor (if present), mounting brackets and ultrasonic path shall be kept clear of cobwebs or other debris to avoid any possibility of interference with the measurement.
7.2.5. The transducer face shall be kept clean of any fouling or condensation.
7.2.6. Maintenance activities shall not affect the transducer operating position and alignment.
8. Electromagnetic flowmeters for flow in pipes
Electromagnetic flowmeters consist of 2 parts:
- the ‘sensor’ detecting the flow of water, generally provided as a pipe section
- the ‘transmitter’ (or converter) which provides calibrated measurement signals and a readout
If a factory or laboratory calibration certificate is available, include a copy of the most recent certificate in the MCERTS inspection report.
The MCERTS inspector shall carry out an on-site inspection to confirm that the flowmeter has been selected and sized correctly, is installed correctly and the effect of any external influences has been assessed.
The MCERTS inspector shall also assess the location of the meter (see section 3.2) and its performance.
8.1. Meter performance
8.1.1. The MCERTS inspector shall confirm meter performance either by inspection with appropriate verification or by secondary testing.
8.1.2. The operator shall make provision in the sensor installation for either verification or secondary testing to be carried out. This may take the form of:
- having a suitable length of pipe next to the meter to attach a temporary, clamp-on ultrasonic meter
- allowing access to the pipe end for basic volumetric tests (small flows), or to insert an area-velocity meter or other temporary device
- having a suitable drop or fill tank which can be used for the flow assessment when required
8.1.3. The operator shall provide new or replacement electromagnetic flowmeter installations with a means of access to allow inspections of the sensor to take place. The design shall enable removal of the sensor if required.
Sensor inspections will include:
- inspecting the general condition
- cable connections
- earthing and bonding
- confirmation of meter type, size, serial number and calibration factors
8.1.4. New installations must have enough exposed pipe available to install a clamp-on flowmeter for verification purposes. The recommended minimum is the greater of either 450 mm or 1.5 pipe diameters.
8.2. Meter performance confirmed by inspection
8.2.1. The MCERTS inspector shall inspect the flow measurement system to make sure that:
- the flowmeter has been selected and sized correctly for the application
- in situations where there is more than one flowmeter on site, the transmitter is connected to the correct sensor
- the liquid is not transporting entrained air
- there is a match between the sensor and the transmitter
- the transmitter is properly configured for the application, for example output scaling, meter bore and correct calibration factors read from the sensor head
- the flow readings are stable
- the sensor is running full and is not subject to fouling or surface deposition (or both)
- there are no external influences, for example another electromagnetic flowmeter installed alongside the unit being assessed
- the earthing and bonding of the measurement system is appropriate to the type of meter and the type of pipe work installed
8.2.2. The meter uncertainties due to flow disturbances and other effects should be included in the overall uncertainty calculation (see Table 3, sourced from authoritative works, for example WRc report CP259 and NEL documents).
8.2.3. The MCERTS inspector shall make sure that verification is carried out at appropriate flow-rates to confirm that the meter is performing satisfactorily and that there are no gross errors. Verification must demonstrate that that the meter is operating under full pipe conditions. It must also demonstrate that the pipe diameter is not compromised by, for example, contamination leading to partial blockage.
Significant errors could also be caused, for example, by the meter not being an appropriate size for the flow-rate or being a different size to ‘as installed’ information. For effluent flow monitoring, the agreement between the method of verification and the meter under test must be within ±8%.
The MCERTS inspector must record how verification was carried out.
8.2.4. If the system fails any of the criteria detailed in section 8.2.1 then an MCERTS inspection certificate cannot be issued unless the meter performance can be confirmed by secondary testing (see section 8.4). Section 2.7 of this standard outlines the procedures that need to take place if a dispensation is required.
8.3. Assessing uncertainties
The MCERTS inspector shall exercise their professional judgement in assessing the total uncertainty. The information in Table 3: uncertainties due to flow disturbances and section 8.3.2 (Uncertainties – other effects) provides guidance and sets out the range of uncertainties for each component of uncertainty. Each component of uncertainty shall be added in quadrature to determine the overall uncertainty for a particular installation.
8.3.1 Uncertainties – effects due to flow disturbances
Table 3 sets out the range of uncertainties for each component.
Table 3: uncertainties due to flow disturbances
Component | Uncertainty range | Guidance notes |
---|---|---|
Single or double bend | 1% to 2% | 0 to 5 diameters upstream or 0 to 2 diameters downstream from the sensor – orientation of the meter to the bends may affect the uncertainty |
Valve | 2% to 18% | 0 to 5 diameters upstream or 0 to 2 diameters downstream from the sensor – the most significant effect is with a gate valve 50% open |
Conical contraction | 0% to 1% | 0 to 5 diameters upstream from the sensor |
Conical expansion | 0% to 3.5% | 0 to 5 diameters upstream from the sensor |
Incoming branch flow | 0% to 1% | 0 to 5 diameters upstream from the sensor |
Pumps | 2% to 18% | 0 to 20 diameters upstream from the sensor – sensors should not be installed on the suction side of pumps |
There is no direct correlation between the diameters specified in the guidance notes and the specified uncertainty range.
8.3.2. Uncertainties – other effects
Basic meter uncertainty
The uncertainty range is 0% to 1%.
This is a fixed allowance for the basic uncertainty in the meter operation. You must make an allowance of 1% unless the factory calibration certificate shows otherwise.
Electronic verification uncertainty
The uncertainty range is 1% to 3%.
The electronic verification test will show several uncertainties for the meter, which indicate changes in the equipment since it was factory calibrated. These include the magnetism test (1% or 2%), mA output test and in some units a frequency test. These must all be added in quadrature independently. If no electronic verification test is available, then you shall allow 3% uncertainty for this item.
Reverse flow uncertainty
Calculating reverse flow uncertainty will overcome problems with, for example, leaky non-return valves. When a full pipe drains back to the wet well that volume is lost (not measured).
You must calculate reverse flow uncertainty as follows:
(Reverse flow total ÷ forward flow total) x100
You must read the reverse and forward flow totals from the meter.
Reverse flows can be a crucial component when calculating the overall performance of the flowmeter.
If a site has a high reverse volume reading then you shall take this into consideration when calculating the overall (forward) volume (for example, the reverse flows are being counted again or ‘double counted’).
You must subtract the reverse volume from the registered overall forward volume.
Some flowmeters have the facility to set readings to register ‘net volumes’ (for example, forward flows less reverse flows).
It is always good practice when carrying out an MCERTS inspection to re-set the forward and reverse totaliser readings to zero. This then enables you to assess the forward and reverse volumes.
Fouling (surface deposition) on the inside of the meter
You must assess this uncertainty and detail the method used. The MCERTS inspector will calculate this from the reduction in effective diameter of the meter.
Air entrapment
Entrapped air will displace water passing through the sensor causing over-reading of the flow.
You must assess this uncertainty and detail the method used.
8.4. Meter performance confirmed by secondary testing
8.4.1. Under this method an alternative (temporary) means of flow measurement, or a drop-test, can be used to assess the flowmeter performance. This method is suitable for buried meters or other installations where an inspection cannot be carried out.
8.4.2. Testing with an alternative means of flow measurement may be carried out by comparing the electromagnetic flowmeter with, for example, an insertion probe or clamp-on ultrasonic flowmeter. The measurement uncertainty of these reference methods may be considerably more than the manufacturer’s specification for an electromagnetic flowmeter.
The MCERTS inspector should be satisfied that the averaged results from the temporary means of flow measurement, and the meter under test, correlate adequately. The MCERTS inspector will use the results in the overall uncertainty calculation.
8.4.3. For the alternative meter method, a volumetric test combined with instantaneous readings shall be used. The volumetric check shall monitor the flow for a minimum of 10 minutes or 10 cubic metres, whichever is appropriate. The instantaneous readings shall be compared at different rates, typically at high, low and medium flows.
At least 10 instantaneous readings shall be taken and the average used for the comparisons. Where it is not possible to take high, medium and low instantaneous flows it may be necessary to base the verification on a single test run. In such cases the number of readings taken shall still be a minimum of 10 but the volumetric test shall be extended to 20 minutes or 20 cubic metres whichever is appropriate.
8.4.4. Drop tests or fill tests may be carried out using any suitable tank or chamber. The actual volume is at the discretion of the MCERTS inspector but must be sufficient to allow valid comparisons to be made.
The test shall run for a suitable period, at least long enough to allow flow conditions inside the pipe to stabilise. It is likely that the fill or empty period will be greater than one minute.
Wherever possible the chamber or tank shall be vertically sided with a small cross section relative to its depth allowing accurate depth measurement and minimising volume errors. Care shall be taken to avoid errors due to empty or part empty pipes.
If possible, the test should be repeated at high, medium and low flow-rates. The volume recorded by the meter under test shall be compared to the volume discharged or displaced. The test shall be repeated at least 3 times, more if required.
8.4.5. Other ‘off line’ techniques may also be possible, if there is no ready access to the flow meter, for example:
- comparing flows at different flow meters within the site
- installing a temporary flow meter at an appropriate location in the process
8.4.6. The MCERTS inspection report shall include a description of the equipment and the method(s) used. The report must include recorded data to substantiate the results.
8.4.7. In circumstances when verification or secondary testing cannot be carried out then evidence will need to be provided to demonstrate that the meter is installed correctly and that significant fouling or deposition is not taking place.
8.5. Keeping the meter full
8.5.1. The installation and design shall ensure that the pipe and sensor are running full of liquid at all times. Poor installation conditions may result in a partially filled pipe and sensor under certain conditions. Air entrapment will often result in rapidly fluctuating readings on the flow display.
8.5.2. Ideally the sensor should be orientated such that flow is always in an upwards direction. Any air contained within the water in the sensor will then be carried upwards through the sensor by the flow.
8.6. Fouling and surface deposition
8.6.1. The operator shall ensure that the sensor is located so that sediment cannot settle in times of low flow, for example in a vertical leg of pipe work (the bottom of an invert should be avoided). The installation shall allow access for appropriate, cleaning and maintenance to ensure that the meter’s performance is not affected. If the flowmeter is installed near the inlet or discharge point of the pipe, then jetting or brushing may be possible without separate access.
8.6.2. It is important to make sure that velocities through the meter are high enough to keep solids in suspension. Higher velocities will be required for untreated sewage than for final effluent. High velocities shall not be regarded as an alternative to regular cleaning.
8.6.3. The orientation of the sensor shall prevent the electrodes from becoming covered should silting occur on the bottom surface of the sensor pipe.
8.6.4. Table 4: errors due to deposition, shows the measurement errors for a 150mm electromagnetic flowmeter which result from surface deposition reducing the meter cross-sectional area. This demonstrates the need for a rigorous cleaning regime.
Table 4: errors due to deposition
Surface deposition (mm) | Resulting error % flow |
---|---|
1 | +3 |
2 | +5 |
3 | +8 |
4 | +10 |
5 | +13 |
8.7. Cabling, earthing and bonding
8.7.1. Electromagnetic flowmeters make use of magnetic and electric fields to generate an electrical signal proportional to the velocity of the fluid through the meter. This signal is very small and can be influenced by electrical charge carried in the fluid and electrical fields nearby. To minimise such effects, the operator should locate sensors and cables away from sources of strong electrical or magnetic fields, such as pumps, high voltage electrical cables and equipment.
8.7.2. The operator shall follow the manufacturer’s requirements for potential equalisation (also referred to grounding). These requirements vary between manufacturers and depend on pipe materials. BS EN ISO 20456 shows that for metallic pipes there should be an electrical connection between the sensor body and the metallic pipework up and downstream of the sensor. For non-metallic pipes equalising (or grounding) rings shall be fitted up and downstream of the sensor and electrically connected to the sensor body.
8.7.3. If cathodic protection is in place to prevent pipe corrosion, then the operator should take further precautions as specified by the manufacturer or by reference to BS EN ISO 20456 Appendix C.
8.8. Flow disturbances due to other equipment
8.8.1. Disturbances to the flow due to bends, valves, reducers or poor alignment will have a direct effect on the performance of the meter. Ideally, the operator should install the sensor in a straight length of pipe of the same nominal diameter, with at least 5 straight pipe diameters upstream and 2 downstream.
8.8.2. Valves can have a significant effect on the performance of the flowmeter, particularly when partially closed. Experimental evidence indicates that, for example, a partially closed gate valve located directly upstream of the sensor can produce an error in flow measurement of up to 18%. Within 5 diameters upstream or 2 diameters downstream of the sensor, valves shall be assessed using Table 3. Valves in this region which are intended to be permanently open shall be locked in this state.
8.8.3. Pumps can also have a very significant effect on the performance of the flowmeter. Ideally, the operator should not install pumps within 20 pipe diameters upstream of the sensor. However, some pump types may permit installation within ten diameters. The operator should not install sensors on the suction side of a pump.
8.8.4. If any of the above cannot be achieved due to physical constraints on site, then uncertainty allowances will be made for the flow disturbance sources. The MCERTS inspector will calculate these using Table 3.
8.9. Other sources of uncertainty
8.9.1. The MCERTS inspector shall ensure that by-pass valves are secure (preferably locked off) to prevent unplanned use.
8.9.2. Reverse flows due to leaky or badly maintained non-return valves, flap-valves or by-pass valves will have a significant effect on flow measurement. Depending on the set up, any backflow due, for example, to a leaking non-return valve may contribute towards a double-counting error.
8.9.3. Where possible, the MCERTS Inspector should establish that the flowmeter reads zero when no flow is passing through the flowmeter.
8.9.4. The operator should make sure the flowmeter is installed and operated in such a way that it is not affected by electromagnetic interference. Sources of such interference can include other electromagnetic flowmeters installed next to the unit under test (information from manufacturers indicates that there should be a space of at least 2 diameters between units), or mains cables run close by and parallel to the sensor cables of the unit under test. Other sources of interference may also exist.
8.10. Electronic verification
8.10.1. Electromagnetic flowmeters are individually calibrated at the factory. Some manufacturers have accredited calibration facilities to maintain traceability of calibration for all flowmeters they produce. During factory calibration, parameters are stored in a non-volatile memory within the flowmeter or transmitter. Therefore each flowmeter has its own ‘fingerprint’.
8.10.2. Electronic in-situ verification tools perform a series of tests to evaluate the status of the complete flowmeter. They record a number of parameters and compare them with the stored ‘fingerprint’ values obtained when the flowmeter was calibrated by the manufacturer. These tests include checks on the:
- transmitter
- sensor
- signal outputs
- system insulation
- cables
- magnetic circuitry
8.10.3. Electronic in-situ verification is considered to be a very useful tool for assessing the condition of installed electromagnetic flowmeters. However, electronic verification does not measure flow. It only indicates whether the meter characteristics, including fouling, are likely to have changed since the last time the meter was subject to verification. Only using electronic verification to assess whether the installation of an electromagnetic flowmeter complies with MCERTS is not acceptable.
8.10.4. The results of electronic verification and uncertainty are taken into account (see 8.3.2) and can be used as one element of an annual review procedure.
8.10.5. Where a flowmeter is buried, inspection of as-installed drawings or photographs (or both) may enable the operator to demonstrate that the flowmeter has been installed correctly and that the measurement still represents the correct flow. Inspecting as-installed drawings or photographs is not necessary when the flowmeter can be verified by an alternative method, for example, a drop test.
8.11. Additional information
8.11.1. Electromagnetic flowmeters have been widely used for many years. Further information and guidance can be found in BS EN ISO 20456, Measurement of fluid flow in closed conduits – Guidance for the use of electromagnetic flowmeters for conductive liquids.
9. Installing and using area-velocity flowmeters in free surface flows
This section of the standard provides information on installing, using and assessing flow measurement systems that use the AV measurement technique. It applies to flow measurement systems (flowmeters) which incorporate sensors for fluid velocity and fluid depth. These measurements are combined to give the volumetric flow-rate in an open channel or partially filled pipe.
An AV flowmeter is one which includes three principal components, a:
- level sensor which measures the depth of fluid in a channel or partially filled pipe
- velocity sensor that measures a characteristic fluid velocity
- flow computer that takes inputs from these sensors and uses those measurements to determine the volumetric flow-rate
There are a wide variety of AV meters using different combinations of sensor techniques. The sensors, both the level and velocity components, may be mounted above the fluid (non-contact) or within the fluid (contact).
We recommend that operators that are considering using an AV meter should carry out a site investigation before deciding on a particular technical approach. This should include identification of the velocity profile. Potential users should also refer to the relevant MCERTS product certificate to determine the suitability of a device for a particular application.
You can find further information on the use of AV flowmeters in MCERTS Bulletin 27. This includes information on:
- general requirements
- location and installation
- maintenance and verification
Research is planned to investigate the optimum installation requirements needed to ensure that AV meters can achieve the measurement uncertainty necessary to conform to the specifications of this standard.
When new information becomes available, Bulletin 27 will be updated to reflect the findings. This section will be updated at the earliest opportunity.
10. Status of this document
This MCERTS standard may be subject to review and amendment following publication. The latest version is available on the MCERTS page on GOV.UK.
CSA issues bulletins providing updates and additional guidance or instructions. These bulletins are available on the CSA website
If you have any questions regarding the inspection process, please contact CSA at:
CSA Group Testing UK Ltd
Unit 6
Hawarden Industrial Park
Hawarden
DEESIDE
CH5 3US
Telephone: +44 (0) 1244 670 900
email: mcerts@csagroup.org